
Case study cement industry: increased fuel efficiency
This short case study shows how data mining has led to significant and recurrent savings in a cement plant located in Belgium. In this example, the fueling of the multi-step-heating process of production lines was analyzed and optimized. A good case to show that data analytics might be capable to deliver the next step in energy efficiency.
Read Full Business PracticeEuropean Heat Pump Association (EHPA)
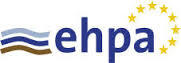
The European Heat Pump Association (EHPA) represents the majority of the European heat pump industry. Its members comprise of heat pump and component manufacturers, research institutes, universities, testing labs and energy agencies. Its key goal is to promote awareness and proper deployment of heat pump technology in the…
Hannover Messe - HM19
All key technologies and core areas of industry – from research and development, industrial automation, IT, industrial supply, production technologies and services to energy and mobility technologies – can be found in Hannover. Take advantage of all…
DetailsNew - automated predictive maintenance using unstructured data
In this announcement, Warwick Analytics briefly describes their next level software developments leading to automated predictive maintenance including scheduling of corrective maintenance. Whereas benefits of such tools like reduced downtime and a reduction of energy and waste is not new in general, Warwick Analytics also claims to solve implementation barriers like unstructured data or complex IT…
Read Full Business PracticePrayon case study: with data mining to energy efficiency improvements
Prayon is the world leader in production of phosphate salts. This short case study describes how Engis, the main plant of Prayon, saves EUR 500.000 per year on energy costs. Prayon has applied three main steps delivered by specialist PEPITe: advanced data mining techniques, real-time visualization and cross department training.
Read Full Business PracticeBeverages: Frueh Koelsch - oil free compressed air
The most economic configuration for oil-free compressed air generation: An excellent set of metrics supported the brewery‘s decision to improve its compressed air generation. “We always record the compressed air energy consumption and the volume flow generated. This gives us a precise overview of the compressed air costs and enables us to carry out targeted optimisation measures.”
Read Full Business Practice5 Things you need to know about 5G Heat (Fifth Generation Heat!)
In my blog ‘ How will energy look in 2030? My 10 predictions for the next 10 years! ’ I predicted that by 2030 all city centres will have some form of fifth generation heat network – taking heat…
Read Full articleH2020-funded project RETROFEED kicks off in Brussels
Implementing smart retrofitting frameworks in the process industry towards its operation with variable, biobased and circular feedstock The 26 th and 27 th November 2019 mark the official launch of…
Read Full articleOutokumpu Cools Machine Shop using natural Elements
To cool the rolling mill's machine shop, Outokumpu has chosen a solution that saves energy compared with more conventional alternatives. There are two ways to cool the machine shop. One is to use outdoor air, the other to use industrial water from a nearby river and cool the air through existing cooling coils and a SWEP B649 brazed plate heat exchanger.
Read Full Business PracticeBakery UK - production air with heat recovery
Just three months after installing two fixed-speed L110s and one regulated-speed L132RS compressor, along with a heat recovery system from CompAir, a leading supplier of bread products is on target to achieve annual energy savings in the region of £188,000, with a payback on investment in less than two years.
Read Full Business Practice