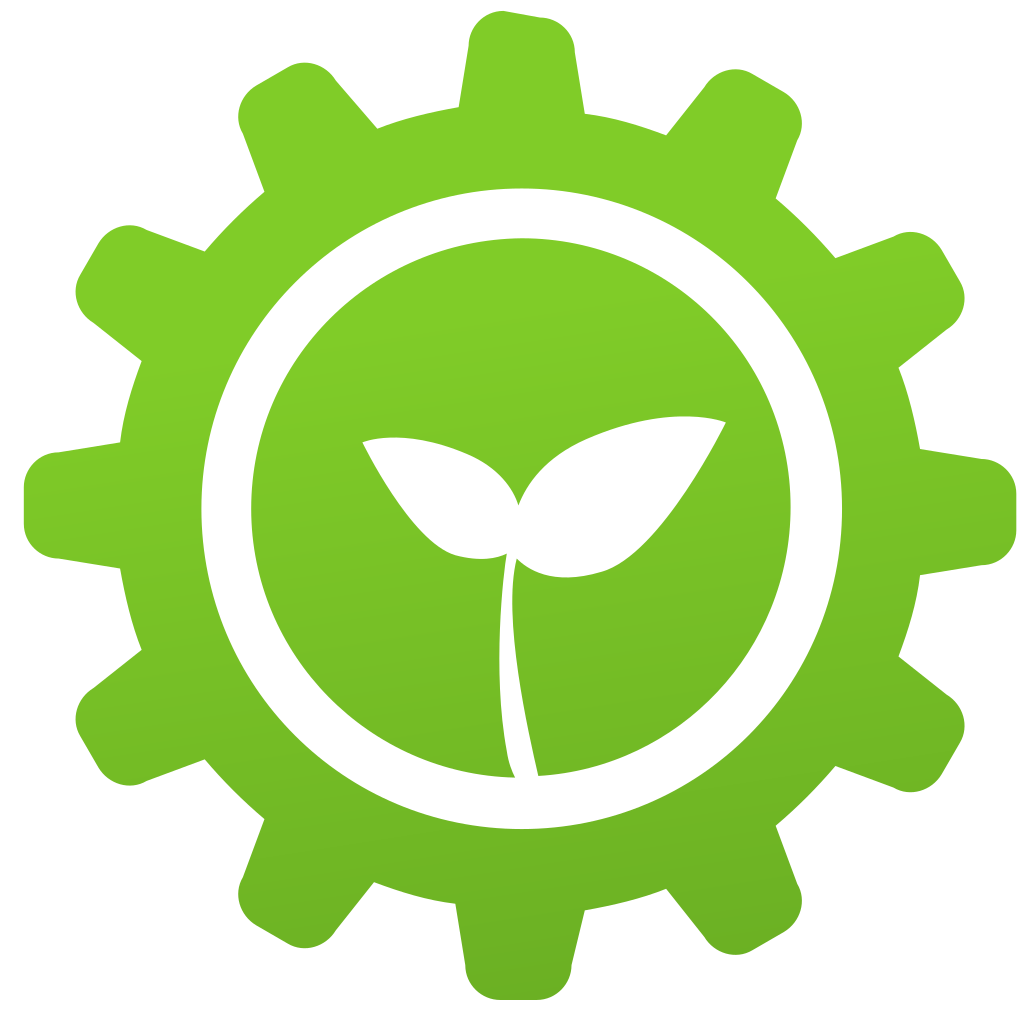
Revolutionizing Pump Systems: The Power of Life Cycle Cost Analysis
Resumo
Efficient management of pumping systems is crucial in the industrial sector, as they account for a significant portion of energy consumption. The comprehensive guide by the Hydraulic Institute and Europump emphasizes the necessity of considering the entire Life Cycle Cost (LCC) of pumping systems rather than just the initial investment, as this approach can lead to considerable savings. LCC includes varied costs from installation to decommissioning, including energy, operation, maintenance, downtime, and environmental impacts. Studies identify that 30% to 50% of energy used in pump systems could be saved through modifications and control system updates. To optimize pumping systems, strategies such as proper system design, avoiding pump oversizing, using Variable Frequency Drives (VFDs), regular maintenance, and ongoing performance monitoring are recommended. LCC analysis identifies the most cost-effective solutions over the system's lifespan, as illustrated in the guide by an example where a plant engineer addressed a control valve issue. By applying LCC analysis to compare options, they achieved significant long-term savings and enhanced system efficiency, demonstrating the benefits of this holistic approach to pumping system management. This LCC-centric perspective is essential for energy efficiency, cost savings, and environmental sustainability in the industrial sector.
Artigo aberto completo
Revolutionizing Pump Systems: The Power of Life Cycle Cost Analysis
In today's competitive industrial landscape, optimizing operational costs while maintaining peak performance is crucial for success. One often overlooked area with significant potential for improvement is pumping systems. These vital components account for nearly 20% of the world's electrical energy demand and can constitute up to 50% of energy usage in certain industrial plant operations. As energy costs continue to rise and environmental concerns grow, understanding and implementing Life Cycle Cost (LCC) analysis for pumping systems has become more critical than ever.
The Hidden Costs of Pumping Systems
When considering the costs associated with pumping systems, many organizations focus solely on the initial purchase and installation expenses. However, this narrow view often leads to suboptimal decisions that can result in higher long-term costs. The Life Cycle Cost of a pumping system encompasses much more than just the upfront investment. It includes energy consumption, maintenance, repairs, downtime, and even environmental impacts over the entire lifespan of the equipment.
According to studies cited in the Hydraulic Institute and Europump's comprehensive guide, "Pump Life Cycle Costs: A Guide to LCC Analysis for Pumping Systems," a staggering 30% to 50% of the energy consumed by pump systems could be saved through equipment or control system changes. This revelation highlights the immense potential for cost savings and efficiency improvements that can be achieved through proper LCC analysis and implementation.
Understanding Life Cycle Cost Analysis
Life Cycle Cost analysis is a powerful management tool that enables companies to minimize waste and maximize energy efficiency in their pumping systems. The LCC methodology takes into account various cost elements, including:
- Initial investment costs (Cic)
- Installation and commissioning costs (Cin)
- Energy costs (Ce)
- Operation costs (Co)
- Maintenance and repair costs (Cm)
- Downtime and loss of production costs (Cs)
- Environmental costs (Cenv)
- Decommissioning and disposal costs (Cd)
By considering all these factors, organizations can make more informed decisions when designing new systems or optimizing existing ones. The goal is to find the most cost-effective solution over the entire lifespan of the equipment, rather than simply choosing the option with the lowest initial price tag.
Key Strategies for Optimizing Pumping Systems
To leverage the power of LCC analysis and improve pumping system efficiency, consider the following strategies:
- Proper System Design: The most critical factor in minimizing LCC is ensuring proper pumping system design from the outset. This involves carefully matching the pump, driver, piping installation, and operating controls to the specific application requirements.
- Avoid Oversizing: One common pitfall is the tendency to oversize pumps, which can lead to increased energy consumption and premature equipment wear. Accurate calculation of system requirements and proper pump selection are essential.
- Utilize Variable Frequency Drives (VFDs): In systems with varying flow requirements, VFDs can offer significant energy savings by allowing pumps to operate at optimal efficiency points across a range of conditions.
- Regular Maintenance: Implementing a proactive maintenance program can help prevent unexpected failures, reduce downtime, and maintain optimal system efficiency throughout the equipment's lifespan.
- Monitor and Optimize: Continuous monitoring of pump system performance can help identify opportunities for optimization and ensure that efficiency gains are maintained over time.
Case Study: Solving a Control Valve Problem
To illustrate the power of LCC analysis, consider a real-world example from the guide. A plant engineer was experiencing recurring failures of a fluid control valve due to cavitation-induced erosion. The valve required costly repairs every 10-12 months. Instead of simply replacing the valve with a more robust model, the engineer conducted an LCC analysis to explore alternative solutions.
Four options were considered:
A. Installing a new, properly sized control valve
B. Trimming the pump impeller to reduce head and pressure drop across the valve
C. Installing a variable frequency drive and removing the control valve
D. Maintaining the status quo with yearly valve repairs
After analyzing the life cycle costs over an 8-year period, the results were striking. Option B – trimming the impeller – emerged as the most cost-effective solution with a present LCC value of 59,481 euros. This was significantly lower than the next best option (C) at 74,313 euros, and less than half the cost of continuing with the current approach (D) at 113,930 euros.
This case study demonstrates how LCC analysis can reveal unexpected solutions and lead to substantial cost savings over the long term. By considering factors beyond just the immediate repair costs, the plant was able to identify a solution that not only solved the valve problem but also improved overall system efficiency and reduced energy consumption.
Embracing a Holistic Approach to Pumping System Optimization
As industries face increasing pressure to reduce energy consumption, cut costs, and minimize environmental impact, the importance of Life Cycle Cost analysis in pumping system design and operation cannot be overstated. By adopting this holistic approach, organizations can unlock significant savings, improve reliability, and contribute to a more sustainable future.
The key lies in shifting perspective from short-term fixes to long-term optimization. This means considering all aspects of a pumping system's lifecycle, from initial design and installation through operation, maintenance, and eventual decommissioning. By doing so, companies can make more informed decisions that balance upfront costs with long-term benefits, ultimately leading to more efficient, cost-effective, and environmentally friendly pumping systems.
As we move towards a future where energy efficiency and sustainability are paramount, embracing Life Cycle Cost analysis for pumping systems is not just a smart business decision – it's an essential step towards a more resilient and competitive industrial sector.
Source: https://www.europump.net/files/Publications/Guides/LCC_Executive_Summary.pdf