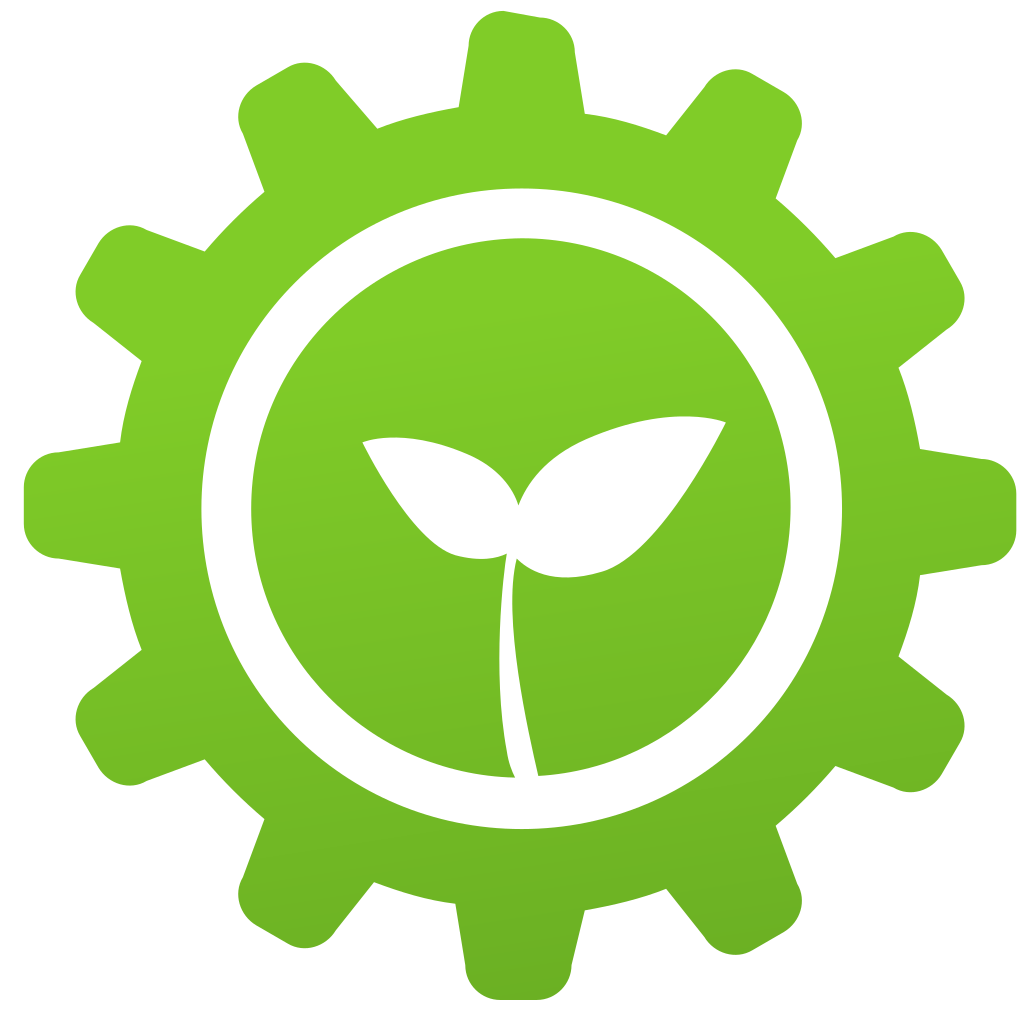
Farewell to Traditional Compressor-Based Refrigeration?
Summary
ULT freezers with a compressor-based cascade refrigeration system can use as much energy as a typical U.S. household annually. C Cascade systems use synthetic refrigerants which cause ozone depletion. The technology can achieve this degree of cooling by using 100% natural refrigerants. A freezer with a Stirling cooling system became the industry's first Energy Star Certified ultra-low temperature freezer, setting the standard. Some utilities and institutions are paying incentives for Stirling Cooling Freezers to influence the market. These systems contain only two moving parts (a piston and a displacer), have no valves, and
No oil and gas bearings, which also reduces the maintenance costs. A 2015 My Green Lab Study, Market Assessment of Energy Efficient Opportunities in Laboratories identified that there are 440,000 to 890,000 ULT Freezers in the ULT freezer energy savings. California labs alone could save up to $59 million per year by replacing compressor based on estimated ULTFreezers.
Open full article
Farewell to Traditional Compressor-Based Refrigeration?
From Ozgun Danaci, DNV GL
Until recently, the healthcare industry relied on ultra-low temperature (ULT) freezers with compressor-based cascade refrigeration systems. Cascade systems are simply two separate compressor-driven refrigeration cycles in a cascade arrangement that achieves ultra-low temperatures by removing heat from the freezer in two stages. The first cycle removes heat from the freezer cabinet with its evaporator and rejects that heat in the second cycle with its condenser. Since there is a significant temperature difference between the condenser of the first cycle and the evaporator of the second cycle, ultra-low temperatures can be achieved. The second cycle then returns this heat to the atmosphere to complete the refrigeration cycle.
![]() |
---|
Figure: Compressor Based Cascade Refrigeration System [1]
ULT freezers with a compressor-based cascade refrigeration system can use as much energy as a typical U.S. household annually. Cascade systems can emit more than 70 tons of CO2 over its lifetime[2], contributing significantly to global warming. Cascade systems use synthetic refrigerants which cause ozone depletion. On top of the environmental drawbacks, these systems require a significant amount of maintenance due to the number of moving parts and start-stop operation of the compressors.
Recently, freezers using a Stirling cooling system were introduced to the market as an alternative to compressor based refrigeration systems for ultra-low temperature applications. These new freezers are compressor-free and utilize a beta type Stirling cooler that is driven by an integral linear motor. The system consists of a piston, which is moved by the linear motor, and a displacer, which is moved by the working fluid (the piston and displacer are not mechanically coupled). The displacer has a hot and a cold side, where compression and expansion occurs during the heat transfer cycle. The cold side of the cooler is connected to a gravity-driven thermosiphon where refrigerant flows down through the tube as liquid, absorbs the heat from the freezer, transitions to vapor, flows up the tube and condenses back to liquid on the cold side of the Stirling cooler. The Stirling cooler piston/displacer assembly moves the heat to the hot side by a refrigerant and then disperses the heat into the atmosphere with a fan.
![]() |
---|
Figure: Stirling Cooling System [3]
A Stirling cooling system uses 60% less energy on average than a cascade refrigeration system. Energy and cost savings from replacing a cascade system with a Stirling cooling system can be as high as 75%, depending on the baseline equipment and operating conditions. Stirling coolers can continuously modulate, thus allowing operations between -20oC to -86oC, compared to the -60oC to -86oC operation of cascade systems. As a bonus, these systems can achieve this degree of cooling by using 100% natural refrigerants which can eliminate the need for ozone depleting chemicals. These systems contain only two moving parts (a piston and a displacer), have no valves, and no oil and gas bearings, which also reduces the maintenance costs.
A 2015 My Green Lab Study, Market Assessment of Energy Efficient Opportunities in Laboratories[4] identified that there are 440,000 to 890,000 ULT freezers in the U.S., 58,000 of which are estimated to be in California alone. Based on estimated ULT freezer energy savings, California labs alone could save up to $59 million per year by replacing compressor based ULT freezers with Stirling cooling freezers [3].
A freezer with Stirling cooling system became the industry’s first Energy Star Certified ultra-low temperature freezer, setting the standard. Some utilities and institutions are paying incentives for Stirling cooling freezers to influence the market. The healthcare industry is already benefiting from this technology.
The challenge: Can this technology replace compressor-based refrigeration systems for commercial applications and should utility energy efficiency programs move in this direction?
Originally posted here
Related articles
- The 4th utility - compressed air
- Compressed air - Hannover Messe 2017 follow up
- Artificial Intelligence in Energy Management Software
Best ideas for Energy Efficiency
About the author
Ozgun is an Energy Engineer with six years of experience in energy assessment, carbon emission reduction and renewable energy systems. Ozgun holds a master’s degree in Renewable Energy and a bachelor’s degree in Chemical Engineering. He is a Certified Energy Manager, and is a LEED Accredited Professional in Building Design and Construction.
Sources
[1],2,3 Stirling Ultracold, Global Cooling Inc.
[4] www.etcc-ca.com/sites/default/files/reports/ceel_market_assessment_et14pge7591.pdf