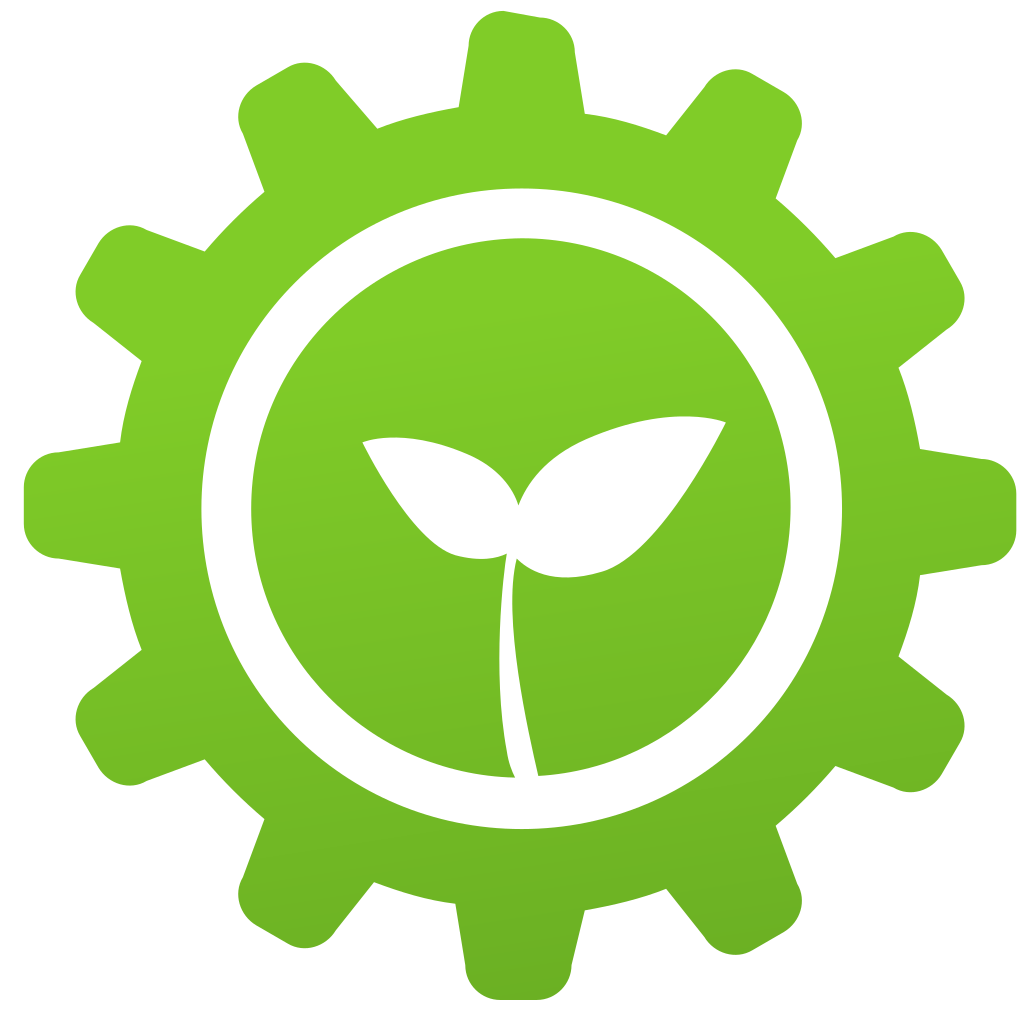
Four young scientists talk about the future of waste heat recovery
Summary
Scientists in four European countries have been working on the ETEKINA project. They have developed three new heat pipe heat exchangers (HPHE)
They aim to recover between 57% and 70% of waste heat streams in three specific sectors: steel, aluminium and ceramics. Their names are Matevz Pusnik, Nerea Nieto, Lujean Ahmad and Matteo Venturelli. The four agree that one of the most valuable features of the project is the creation of a revolutionary tool that will benefit energy intensive industries with an untapped potential to reutilise waste heat. They expect HPHE will contribute to the momentum that is building around waste heat utilisation systems as climate change awareness grows, so does the global market for waste heat recovery technologies. This industry is expected to register annual increases of 6% in the next few years and reach US$16.8 bn in 2023, according to Technavio.
Open full article
Four young scientists talk about the future of waste heat recovery
On the crossroads to sustainability, energy intensive industries face huge challenges – waste heat recovery is one of the most promising options to save energy, feed a circular economy and go green. For over three years, a group of scientists in four European countries have been working on the ETEKINA project to reinvent an incredibly efficient technology to recover and reuse excess heat.
Within the ETEKINA project, researchers have developed three new heat pipe heat exchangers (HPHE) to address the specific challenges of different energy intensive industries. Now, only months away from the completionof the EU Project, four of the youngest minds involved in this project gathered on a video call last month to share their thoughts and hopes on the impact they expect from the innovative HPHE to have in sectors that register some of the largest carbon footprints in the world.
Their names are Matevz Pusnik, Nerea Nieto, Lujean Ahmad and Matteo Venturelli. The four of them agree that one of the most valuable features of the project is the creation of a revolutionary tool that will benefit energy intensive industries with an untapped potential to reutilise waste heat. “The HPHE is a compact and robust solution for energy intensive industries in a moment when waste heat utilisation is a hot topic across the world,” says Matevz. “And it’s very innovative.”
ETEKINA’s HPHE have been designed with the objective of recovering between 57% and 70% of waste heat streams in three specific sectors: steel, aluminium and ceramics. These researchers expect HPHE will contribute to the momentum that is building around waste heat utilisation systems — as climate change awareness grows, so does the global market for waste heat recovery technologies. This industry is expected to register annual increases of 6% in the next few years until reaching US$16.8 bn in 2023, according to the market research company Technavio. Matevz, Nerea, Lujean and Matteo believe that, in the future, all energy intensive industries will have to use some sort of heat recovery system. “That’s the hope and the aim”, says Lujean.
Joining forces from across Europe
For over three years, the young researchers have combined efforts from four different countries. In Slovenia, 39-year-old Matevz Pusnik is the person responsible for developing a multiuse heat recovery software managment tool be employed in one of ETEKINA’s case studies, a steel production company in the city of Ravne na Koroškem. “The tool is a customised tool which provides cost optimisation and can be used by other energy intensive industries for process optimisation and scenario-based assessment”, he explains. Matevz is a researcher at the Jožef Stefan Institute, where he also applies his expertise in industrial energy management to the preparation of models supporting national strategic and policy documents.
From more than 1,600 kilometres away, in the North of Spain, 34-year-old engineer Nerea Nieto is linked into this conversation. She is a member of the Ikerlan research institute’s team that oversees the implementation of HPHE in an aluminium die casting facility in Arrasate-Mondragón. She has actively participated in ETEKINA from the beginning, helping prepare the proposal and developing a tool to identify if HPHE will suit the client’s needs. “We work with industrial partners to identify which waste heat stream has the highest potential for our technology as well as the internal process where this recovered heat can be reused”, explains Nerea. All of this while looking for new ideas with the potential of becoming an EU project.
Scientists like her and Matevz are used to multitasking, splitting their time between different projects. Matteo, a 29-year-old PhD student at the University of Modena and Reggio Emilia, is currently taking part in two EU projects, including ETEKINA. “I’m in direct contact with the ceramics tile producerAtlas Concorde, one of the three end-users where HPHE will be installed and tested”, he says. His duties include validating the HPHE unit that will be installed in the factory the company has in the Italian city of Fiorano Modenese.
In the United Kingdom, the findings reached by these three researchers and their teams will let 31-year-old Lujean design the best strategy to put ETEKINA’s HPHE in the market. She’s the business development manager of the Heat Pipe and Thermal Management Research Group of Brunel University London. “We analyse the market identifying the trends and highlighting the value and competitive advantage that ETEKINA’s HPHE can bring. We also develop the value proposition, customer life cycle and business models,” she explains. Lujean is involved in six Horizon 2020 projects related to heat pipe technologies, where she provides a business focus and takes part in the dissemination of results.
These researchers acknowledge the economic advantages their project can bring to energy intensive industries, but it is the green benefits that they highlight enthusiastically. “ETEKINA’s HPHE aim to reduce in cost of energy due to lower consumption as companies will now be reutilising the recovered waste heat energy. It will aid in the reduction of greenhouse gas emissions, enabling companies to adhere to the energy efficiency directives,” explains Lujean, “this will offer great help to about 450,000 companies in the 27 member states of the EU”.In countries with heat district systems, like Slovenia, these benefits can be extended to the community, as her colleague Matevz Pusnik adds– “In our case study, we are integrating into the unit technology to produce heat that can be transferred to the local district heating network. This is a hot topic in Europe right now.”
Lujean says feedback from partners and experts has been very positive, especially, when comparing HPHE with shell and tube heat exchangers, the standard technology in the sector. “There are so many different elements that shell and tube exchangers can’t cope with but this HPHE can, such as recovering waste heat even with challenging aspects in the heat streams like fouling management, high operating temperatures and multi-sink capability to name a few. I see Matteo agreeing with me on this… Furthermore our replicability analysis tool that has been developed is great because the customer can come to research centres, add in data like temperatures and flow rates for example, and the tool will provide a comparison: ‘This is what you’ll get with an HPHE and this is what you’ll get with a shell and tube heat exchanger’. And it’ll also do a rough comparison of the economics”, she explains.
“HPHE enable waste heat recovery from very challenging streams”, adds Matteo. “For example, in Italy, we’re recovering heat from exhaust gases that contain particles… As Lujean says, a traditional heat exchanger may have issues like fouling or acid condensates. But the HPHE technology prevents this because the temperature inside the system is uniform, so there are no cold spots where the exhaust could condensate. HPHE addresses heat recovery from very difficult streams while heat is not usually recovered from industrial exhaust gases because of the harsh environment”.
An unexpected challenge
In these three years, the team has overcome challenges such as persuading industrial partners to participate in the project. “It wasn’t easy”, admits Nerea Nieto, “their business is to produce, that’s their main objective. So even if energy efficiency is a hot topic, it’s not their priority and getting involved in EU projects goes beyond the technical part—you need to prepare economic reports and there are many other tasks.”
“I would like to add that energy intensive industries tend to be quite traditional when it comes to new technologies”, says Matevz Pusnik. “They prefer to implement things that have been working for a couple of years or even decades and, as Nerea mentioned, there’s the administrative part, they need to have support on that.”
“But I believe the biggest challenge is quite obvious”, he says referring to the Covid-19 pandemic, “it’s a really unfortunate time for visiting places and, as Nerea said, timing is crucial for industries. For our partners, every stoppage can be translated into money. A lot of coordination is needed… but we are on a good path.”
Matteo agrees: “There have been some delays due to the pandemic but we were able to install two out of three units in our industrial partners’ facilities (Spain and Slovenia). I think this is a great achievement.”
HPHE units have been designed by Brunel University London’s professor Hussam Jouhara and his team needs to be present during hot commissions, which has turned out complicated due to international travel restrictions to prevent the spread of Covid-19. “Travelling to install and commission these units is a crucial point in our project to ensure correct procedures are followed”, explains Lujean. “Despite the challenges, we travelled twice in December 2020 and went the extra mile to make sure we were present in Spain when they experienced some technical issues. A lot of quarantining was involved for Brunel’s staff, let’s put it that way.”
At the moment, some European companies like these three case studies are having their first contact with excess heat recovery technologies but many others are still to learn the economic and environmental benefits they can provide. However, the four researchers are convinced that this is a market trend that is here to stay.
“I’d say that every energy intensive company will have to utilise their waste heat in some way. This is a fact since energy and CO2 coupon prices are going up”, says Matevz. “Many European countries have already put waste heat utilisation in their national energy and climate plans. So it’s going to be done, it just depends on which technology specifics. HPHE tackle a certain niche and I believe that waste heat utilisation technologies will be subject to an important push in the next 10 years… So it’s a bright future for waste heat utilisation.”
Nerea, Matevz, Lujean and Matteo still have seven months to test and optimise ETEKINA’s HPHE units designed for the steel, aluminium and ceramics industries and they’re excited about seeing the results of a project they started back in 2017. “Young researchers’ motivation is usually very high. When you’re at the beginning of your career, you want to assume this kind of challenges, prove new things and learn a lot,” says Nerea.
“I think it’s because you’re part of such a big innovative research project that will, hopefully, go to the market,” agrees Lujean. “You’re motivated to achieve this and to go further.”
For Matevz, projects like ETEKINA offer young scientists a rare opportunity to work in industrial environments they would not get otherwise: “You can go to their facilities, see the machines and everything. It leaves a mark on you and you learn a lot from the people who are working there— they face problems that are completely different from what you thought. It’s important that young researchers have an insight into the real industrial environment.”
Author: Stefania Gozzer