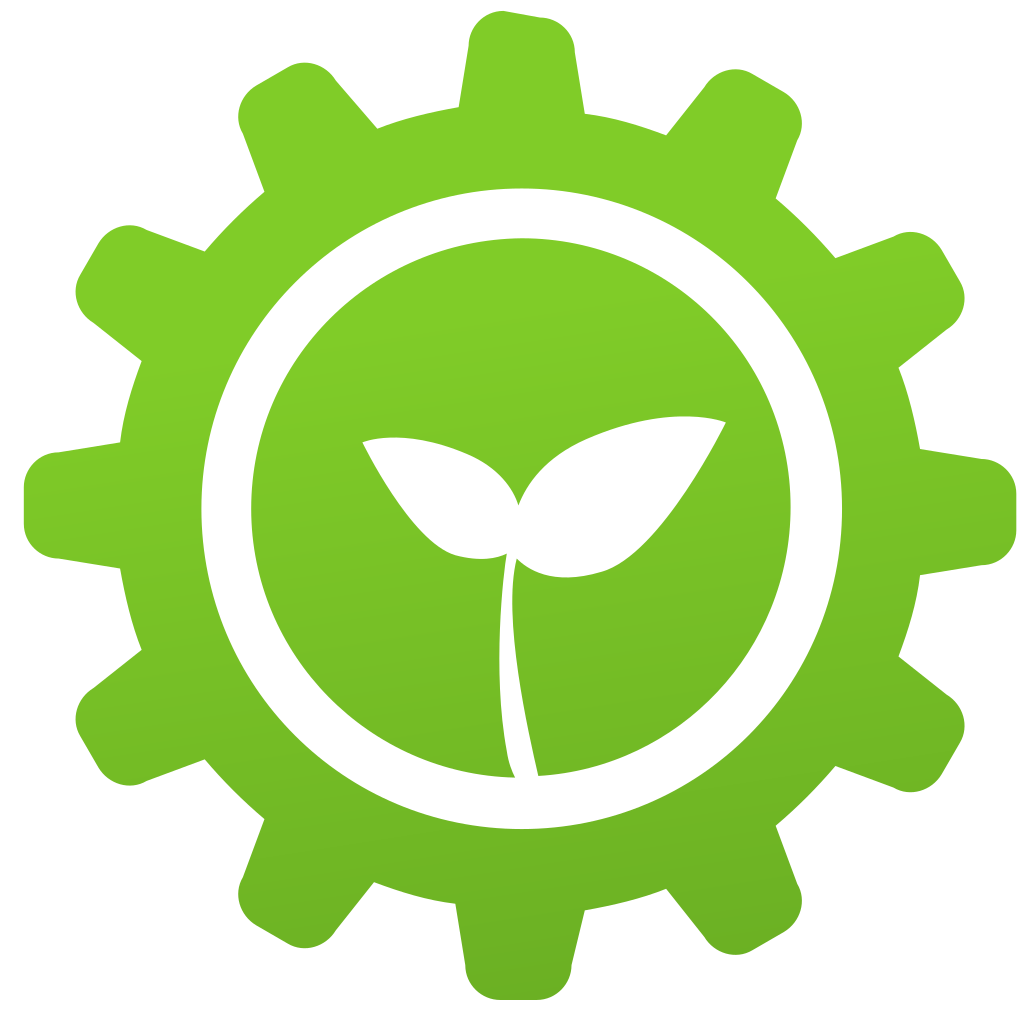
Business Practices
Decarbonisation of industrial heat: The iron and steel sector
Summary
Achieving deep decarbonisation by 2050 is only possible through new production processes. Electricity demand of the sector could increase three-fold by 2050, from a shift to steel made by hydrogen reduction or direct electrolysis. By 2050, the production of steel from recycled scrap increases by a range of +30% to +70% versus 2018, which translates in a potential share of 50% to 77% of total steel production by 2050. The European Commissions ambitions of net-zero greenhouse gas emissions by 2050 need to be considered. An increase of recycled steel is estimated to only further reduce CO2 emissions by
To achieve the European commissions ambitions, new breakthrough technologies, CCS/U (carbon capture and storage/utilisation and an increase of recycling steel need to. be considered. The production of iron and steel sector represented 4% of all EU emissions in 2017, eight scenarios from four publications (Figure 2) are compared to the EAF (ECF,ECF.
Open full article
Decarbonisation of industrial heat: The iron and steel sector
Headlines
- Current primary steel production is highly integrated; incremental efficiency improvements can only further reduce emissions by about 10%. The analysis of scenarios published recently by various sources shows that:
- Achieving deep decarbonisation by 2050 is only possible through new production processes.
- Electricity demand of the sector could increase three-fold by 2050, from a shift to steel made by hydrogen reduction or direct electrolysis.
- By 2050, the production of steel from recycled scrap increases by a range of +30% to +70% versus 2018, which translates in a potential share of 50% to 77% of total steel production by 2050.
Policy recommendations
- Increased RD&D support for technologies compatible with deep decarbonisation of the sector (H-DRI, electrolysis, CCS/U).
- Monitor and enhance the impact of policies aimed at maximising the reuse of steel scrap.
- Establish demand-pull policies to create a market for “green steel”, such as green public procurement for publicly funded infrastructure.
Iron and steel sector overview
The production of iron and steel is a major contributor to EU greenhouse gas emissions. The sector represented 4% of all EU emissions in 2017, and 23% of the manufacturing industry. Crude steel production in the EU has been constant since 2010, at around 170Mt per year, and by 2050 ranges between 153Mt and 172Mt in the FORECAST model scenarios, which fed the industry analysis of the European Commission’s Long Term Strategic Vision. There are two main steelmaking routes in the EU:
- 60% of steel is made via the integrated route, which produces virgin steel from iron ore. Iron, in the form of sinter, is reduced in the presence of coke in a blast furnace (BF), and then converted into crude steel in a basic oxygen furnace (BOF).
- 40% of steel is made through the recycling route, where scrap steel is rep
Process heat overview
Some 95% of process heat demand in iron and steelmaking occurs at very high temperatures (>500oC), and coal/coke is the major energy input into the process, serving both as a fuel source and as a feedstock in the form of coke.
While both the integrated and recycling route require very high temperature processes, their emission and energy intensities differ significantly:
- The integrated route relies on the production of coke as a feedstock to reduce iron in the blast furnace, and the iron ore itself needs to be converted to sinter before being fed into the blast furnace. Both coking and sintering occur at the steelmaking plant and require temperatures above 1000oC. These materials are fed into a blast furnace, where hot air at over 1000oC forms reducing gases from coke, which react with the ore to form reduced iron; CO2 emissions from this process are an inevitable product of the chemical reduction of iron ore. With 1.2tCO2 emitted per tonne of steel, the blast furnace is responsible for over 60% of CO2 emissions in the integrated route. The coke oven emits ~15%, the sinter plant just over 10% and the other processes (basic oxygen furnace, pellet plant) ~10% of the total CO2 emissions (own estimate, based on emissions data from).
- Attributing emissions to specific processes, however, is not straightforward. Waste gases from the coke oven and blast furnace are recovered to provide heat and also to fire onsite power plants, in a highly optimised circuit. Eliminating or replacing any waste gas emissions with alternative processes would disrupt the entire steelmaking route.
- Heat demand in the recycling route is nearly fully electrified. An electric arc at 1600oC directly smelts scrap to produce liquid steel. At the current average CO2 intensity of electricity in the EU, the EAF route emits 0.2 to 0.3 tCO2 per tonne of steel, or 80% less than the integrated route.
Limited potential for improvement
Integrated steel plants have optimised their material and energy flows over the years, and best performers in the EU are already operating at close to optimum levels. Implementing further incremental efficiency improvements and best practices is estimated to only further reduce CO2 emissions by about 10% (own estimate, based on emissions data from). To achieve the European Commission’s ambitions of net-zero greenhouse gas emissions by 2050, new breakthrough technologies, CCS/U (carbon capture and storage/utilisation) and an increase of recycled steel need to be considered.
2050 decarbonisation scenarios
To explore possible pathways to achieve deep decarbonisation of the sector by 2050, eight scenarios from four publications (Figure 2) are compared. While the final energy demand in 2050 decreases in all scenarios, between around -10% (ECF, Carbon Capture) and -50% (ECF, Circular Economy and ICF, Mix80 and Mix95), the demand for steel varies broadly, from -17% (ECF, Circular Economy) to +10% (ECF, New Processes and Carbon Capture) compared to 2015.
New steelmaking processes
New hydrogen steelmaking technologies currently under research aim to replace the natural gas used in the direct reduction of iron (DRI), an existing process, by green hydrogen (H-DRI). If renewable electricity is used both by the hydrogen plant and by the EAF, which further processes the iron to steel, this process could emit up to 95% less CO2 than the current integrated route. Four European projects, HYBRIT, SALCOS, H2Future/SuSteel (investigating hydrogen plasma smelting reduction) and ThyssenKrupp, are developing the entire value chain for hydrogen steelmaking; the earliest demonstration project is not expected to start before 2025.
The direct electrolysis of iron ore, or “electrowinning”, to produce raw steel is being developed by the SIDERWIN project. If using solely renewable electricity, steel production could emit up to 87% less CO2 than the current integrated route. It is still at an early stage of development and has only been proven at laboratory scale.
By 2050, hydrogen steelmaking and electrowinning is deployed in 7 out of 8 scenarios; accounting for up to 35% (65Mt) of the total steel production (ECF, New Processes). Including the production of hydrogen, the yearly electricity demand of the sector could grow up to 3 times the current demand, to 360TWh in 2050 (ECF, New Processes and EC, 1.5TECH). This amount is equivalent to 35% of the EU’s current renewable electricity production. Further key challenges will be the scale-up of hydrogen infrastructure and the necessary investments for extensive brownfield conversions or greenfield deployments.
Carbon capture and storage utilisation
Two European projects, Steelanol and Carbon2Chem, are exploring the valorisation of waste gases from the blast furnace to produce bioethanol and chemical raw materials. While at a more advanced stage of development – the Steelanol demonstration plant is currently under construction in Belgium – maximum emission reductions from these processes are more limited (up to 65% if fully deployed) and will depend on whether the carbon is released again at the end-of-life of the resulting chemical products.
New smelting technologies combined with CCS, such as the HIsarna process, generate CO2-rich waste gas to facilitate carbon capture. Compared with the current route, emissions could be reduced by up to 80%. Implementing these technologies, however, would require profound changes to the steelmaking processes, of a similar scale to breakthrough hydrogen or electrolysis technologies.
Carbon capture technologies are heavily deployed in 2 out of 8 decarbonisation scenarios (IEA, B2DS and ECF, Carbon capture) with up to 30% (54Mt) of the total steel production in 2050 coming from plants equipped with CCS/U (ECF, Carbon capture).
Increased share of recycled steel
By 2050, in 7 out of 8 scenarios recycled steelmaking becomes a more important route, with an increase in production that ranges from +30% (91Mt) to +70% (118Mt) compared to 2018 (70Mt) (scenarios ECF, Carbon Capture and ICF, Mix95 respectively). This corresponds to a share of 50% to 77% of total crude steel production in these scenarios (versus 42% in 2018).
Key challenges to achieve a higher production of secondary steel hinge on increasing steel’s recycling rate (which is currently already between 70%-95%, depending on the end use) and on improving the quality of scrap. Recycled scrap is often contaminated with other tramp elements, of which copper is the most important. Copper contamination limits steel’s use to applications which tolerate lower-quality steel, such as rebar in construction. While the construction sector used 34% (54Mt) of the total finished steel demand in 2018, the demand for higher quality-steel (notably in the automotive sector) is likely to increase at a faster rate in the future. The quality of scrap can be increased downstream, by improving the dismantling and sorting of end-of-life products. Upstream, design changes to reduce the use of copper or to facilitate the disassembly of end-of-life products, can reduce the need for downstream interventions. The EU policymakers can contribute to facing these challenges by monitoring and enhancing the impact of policies aimed at maximising the reuse of steel scrap.
Contact: