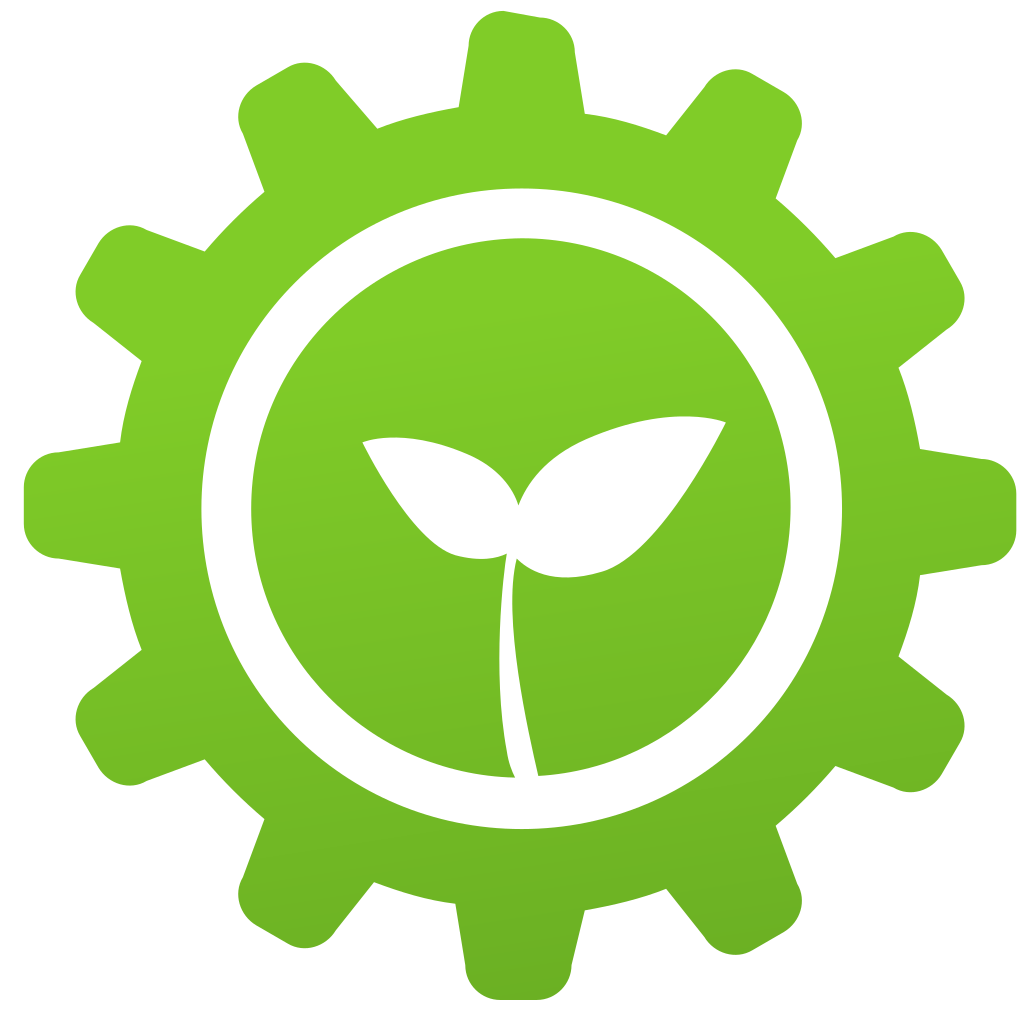
Práticas Comerciais
Harnessing Hydrogen: The Promise of Catalytic Methane Decomposition
Resumo
The paper discusses catalytic methane decomposition (CMD) as a technology to produce hydrogen without associated CO2 emissions. CMD utilizes transition metal catalysts, such as nickel, iron, and cobalt, to break down methane into hydrogen gas and solid carbon at temperatures between 450-750°C, which are lower than the reaction's natural temperature due to catalysis. Despite its benefits, CMD faces the challenge of rapid catalyst deactivation caused by carbon accumulation.
Strategies to combat this include the use of bimetallic catalysts, optimized catalyst supports, catalyst regeneration, and novel reactor designs like fluidized bed reactors. The STORMING project aims to enhance CMD technology by integrating advanced reactor designs.
The paper discusses different reactor configurations such as plasma reactors, molten metal reactors, and membrane reactors. Fluidized bed reactors show promise for industrial-scale hydrogen production, balancing methane conversion, catalyst stability, and ease of carbon removal.
Techno-economic analyses suggest that CMD hydrogen production costs could be competitive with steam methane reforming, especially when considering carbon taxes. CMD could also achieve carbon-negative hydrogen production using biogas or synthetic methane.
The carbon byproduct has economic value as well, especially if carbon nanostructures are produced. CMD could significantly contribute to providing low-cost, low-emission hydrogen in various sectors. Its ability to leverage existing natural gas infrastructure while reducing emissions positions CMD as a potential key player in the transition to renewable hydrogen sources and achieving climate targets.
Artigo aberto completo
Harnessing Hydrogen: The Promise of Catalytic Methane Decomposition
As the world grapples with the urgent need to decarbonize our energy systems, hydrogen has emerged as a promising clean fuel of the future. However, current industrial hydrogen production methods like steam methane reforming still rely heavily on fossil fuels and generate significant carbon dioxide emissions. Enter catalytic methane decomposition (CMD) - an innovative process that directly converts methane into hydrogen and solid carbon, without producing any CO2. This breakthrough technology could play a pivotal role in enabling a smooth transition to a hydrogen-based economy while actively removing greenhouse gases from the atmosphere.
The Mechanics of Methane Cracking
At its core, CMD involves the relatively simple chemical reaction of breaking down methane (CH4) molecules into hydrogen gas (H2) and solid carbon:
CH4 → C + 2H2
While this reaction can occur at very high temperatures around 1300°C, the use of catalysts allows it to proceed at much lower and more practical temperatures between 450-750°C. Transition metal catalysts like nickel, iron and cobalt have shown the highest activity for CMD. The reaction takes place on the surface of the catalyst, with methane molecules adsorbing and decomposing to form hydrogen gas which is released, while carbon deposits build up on the catalyst.
One of the key advantages of CMD is that it produces no COx byproducts, resulting in a very pure stream of hydrogen that requires minimal downstream processing. The solid carbon byproduct can also potentially be used in various industrial applications or safely sequestered. This gives CMD a significant edge over conventional hydrogen production methods in terms of both economics and environmental impact as carbon capture and storage technologies become more strictly regulated and costly.
Overcoming Catalyst Deactivation
The major hurdle that has prevented widespread adoption of CMD thus far is rapid catalyst deactivation due to carbon accumulation. As carbon deposits build up, they eventually block the active sites on the catalyst surface, causing hydrogen production to drop off. Researchers have explored various strategies to enhance catalyst stability:
Combining multiple metals: Bimetallic catalysts like Ni-Fe and Ni-Cu have shown improved stability compared to monometallic versions.
Optimizing supports: Catalyst supports like SiO2 and Al2O3 play a crucial role in metal dispersion and carbon diffusion.
Regeneration: Periodically removing carbon deposits through gasification with steam, CO2 or hydrogen can reactivate spent catalysts.
Novel reactor designs: Fluidized bed reactors allow continuous carbon removal and have shown promise for long-term stable operation.
With continued research and optimization, achieving thousands of hours of stable hydrogen production via CMD may soon be within reach. The EU-funded STORMING project is exploring innovative structured reactor designs heated by renewable electricity to further enhance the viability of CMD technology.
Reactor Configurations for Scaling Up
As CMD moves closer to commercial viability, reactor engineering becomes crucial for industrial-scale hydrogen production. Several reactor types have been investigated:
Fluidized bed reactors: These allow easy removal of carbon products and maintain uniform temperature, emerging as a favored design. Variations like two-stage fluidized beds have shown enhanced catalyst lifetime.
- Plasma reactors: Using plasma can lower the required temperature, but suffers from poor hydrogen selectivity.
- Molten metal reactors: Liquid metal catalysts enable facile carbon separation, but still require very high temperatures.
- Membrane reactors: Integrating hydrogen-selective membranes can drive the reaction towards higher conversions.
The most promising configuration will likely combine fluidized bed operation with optimized catalysts and in-situ regeneration capabilities. Careful reactor design is essential to balance methane conversion, catalyst stability, and ease of carbon removal.
Economic Viability and Future Outlook
Recent techno-economic analyses estimate hydrogen production costs via CMD to be around 1.7-1.85 €/kg H2 when using natural gas feedstock. This is already competitive with steam methane reforming (1.4 €/kg H2) once carbon capture costs are factored in. CMD becomes even more attractive as carbon taxes increase, potentially emerging as the most economical route for large-scale hydrogen production.
Moreover, CMD opens up exciting possibilities for carbon-negative hydrogen production. By using biogas or synthetic methane derived from atmospheric CO2, the process could actively remove greenhouse gases while generating clean hydrogen fuel. Early estimates suggest this may be achievable for just 2.1 €/kg H2 - a small premium for enormous environmental benefit.
The solid carbon byproduct from CMD also holds economic potential. While currently valued at less than 100 €/ton as a basic filler material, more advanced carbon nanostructures could fetch much higher prices in speciality applications. Optimizing carbon quality alongside hydrogen yield will be key to maximizing the overall economics.
As the hydrogen economy takes shape, CMD is poised to play a vital role in providing low-cost, low-emission hydrogen to sectors like heavy industry, long-distance transport, and grid-scale energy storage. With its ability to harness existing natural gas infrastructure while eliminating CO2 emissions, CMD offers a pragmatic bridge between fossil fuels and fully renewable hydrogen. Continued advancement of catalyst and reactor technologies promises to unlock the full potential of this elegantly simple yet powerful process.
The journey towards sustainable energy is complex, but catalytic methane decomposition shines as a beacon of innovation - cracking open new possibilities for clean hydrogen production and carbon management. As we strive to meet ambitious climate goals, CMD may well prove to be a crucial piece of the decarbonization puzzle.
Source: https://www.sciencedirect.com/science/article/abs/pii/S1364032120307516