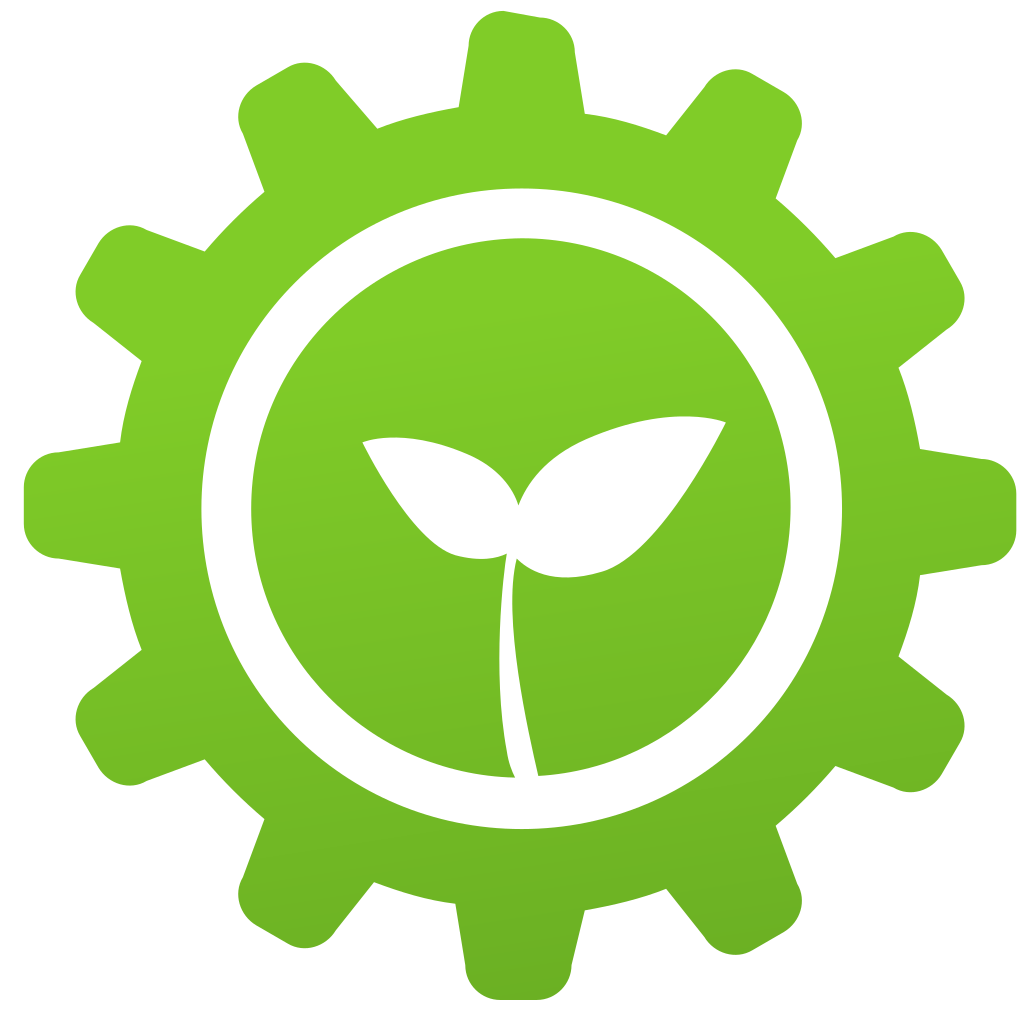
Are ZNE-ready manufactured homes on the horizon
Summary
Tina Aardemae is a senior engineer with DNV GL. She has been working in energy efficiency and sustainability since 2009. Incentives could be offered to move the production line entirely to ENERGY STAR®-levels (or ZNE-ready, in places like California where it will soon be code for permanent homes, including modular)
The benefit of a single production line is reduced cost for both the manufacturer and consumer. In just two more years, ZNE will become the residential code for California, with several other states and regions also on the path to setting more aggressive building codes. The author enjoys trail running, eco-travel, and learning about passive house and zero net energy. For more information, go to www.dNV GL.com/sustainable Buildings and Communities. You can visit www.zero net energy.org/ zne.org.uk/zne.uk. You can find out more.
Open full article
Are ZNE-ready manufactured homes on the horizon
First published here.
Earlier this year, we looked at how zero net energy can make life more comfortable as the weather gets weirder, and how utilities can strategically use ZNE to address the changing grid. In this blog, I’ll highlight some of the latest research from my colleague Jennifer McWilliams on the potential for utility-sponsored ZNE-ready manufactured housing. If you’re attending this year’s ACEEE Summer Study on Energy Efficiency in Buildings, stop by the Net Zero panel to hear the full presentation on ‘Manufactured Housing: It is Easy and Enticing, is it Energy Efficient?’ or download the whitepaper afterward.
Prefab as a solution for places with bad weather
Offsite, or prefab, construction continues to be a key trend for the construction industry, allowing for faster construction timelines that aren’t as dependent on weather as traditional construction projects. This provides an opportunity for quick and inexpensive housing for an increasing number of people displaced by weather events, such as wildfires, hurricanes and floods.
Some of the highest incidents of natural disasters in the US have been in California, Texas, Louisiana, and Florida. These states also have the highest volume of manufactured (including modular and mobile) homes purchases. It would make sense for these homes to provide comfort and be resilient during future weather events. Even if the homes were initially purchased as temporary disaster relief housing, they are often resold and have a second life as permanent housing.
Current hurdle for mass-producing energy efficiency and resiliency
ENERGY STAR® currently offers an ENERGY STAR Certified Homes Program that includes modular and manufactured homes. The Department of Energy built upon ENERGY STAR® Homes v3 and is offering a Zero Energy Ready Home program. DOE has also partnered with builders to develop Zero Energy Ready manufactured mobile homes.
Although many factories are certified to produce ENERGY STAR® homes, and some have also started producing prefab zero energy homes, the consumer demand for these homes is still low due to the increased capital required. This drives a Catch 22 situation — due to the low production volume for more efficient and resilient homes (which follow a different production line process than standard homes), these homes are more costly for the manufacturer, making them more costly for the consumer.
Opportunity for utilities, manufactured home factories, and communities
This provides an opportunity for the utility to step in by providing an upstream new construction program for the manufactured homes factories. Incentives could be offered to move the production line entirely to ENERGY STAR®-levels (or ZNE-ready, in places like California where it will soon be code for permanent homes, including modular). The benefit of a single production line is reduced cost for both the manufacturer and consumer.
This allows the utility to achieve new construction savings at a low incremental cost, target and transform an underserved market, and support communities with resiliency and carbon reduction goals. To help facilitate this and optimize the incentives, utilities and municipalities across the manufactured homes factory territories are encouraged to develop a combined offering.
In just two more years, ZNE will become the residential code for California, with several other states and regions also on the path to setting more aggressive building codes. Resiliency is also taking ‘center stage’ in the construction industry, and more utilities and communities are placing their focus on how to survive the next big storm. ZNE-ready manufactured housing can provide a more durable and resilient housing solution, and allow utilities and builders to partner and create more resilient grids and communities.
Interested in learning more about how DNV GL can support your ZNE efforts around building and program design, energy storage, or renewables?
- Design assistance for ZNE – Sustainable Buildings & Communities
- Implementing utility-run incentive programs that support ZNE – Energy Efficiency Program Implementation & Design
- Energy storage advisory
- Renewables integration
_____________
Related articles
- Offshore wind rising to challenge king coal in Polish eergy market. By Offshore Wind Journal
- The hidden benefits of solar power. By Kerry Kilpatrick
- The next wave of renewable energy? By Chris Bentley
Stay tuned! Best ideas for energy efficiency and energy transition...
About the author
Tiina Aardemae is a senior engineer with DNV GL, and has been working in energy efficiency and sustainability since 2009. Her experience includes technical strategy, new construction, energy efficiency program design and implementation, quality management systems, data management, and software product management. She is also a Quality Management Systems Auditor, LEED® Accredited Professional and a Certified Scrum Product Owner®. Prior to joining DNV GL, Ms. Aardemae worked as a distribution grid engineer and utility customer project manager. Outside of work, Ms. Aardemae enjoys trail running, eco-travel, and learning about passive house and zero net energy.