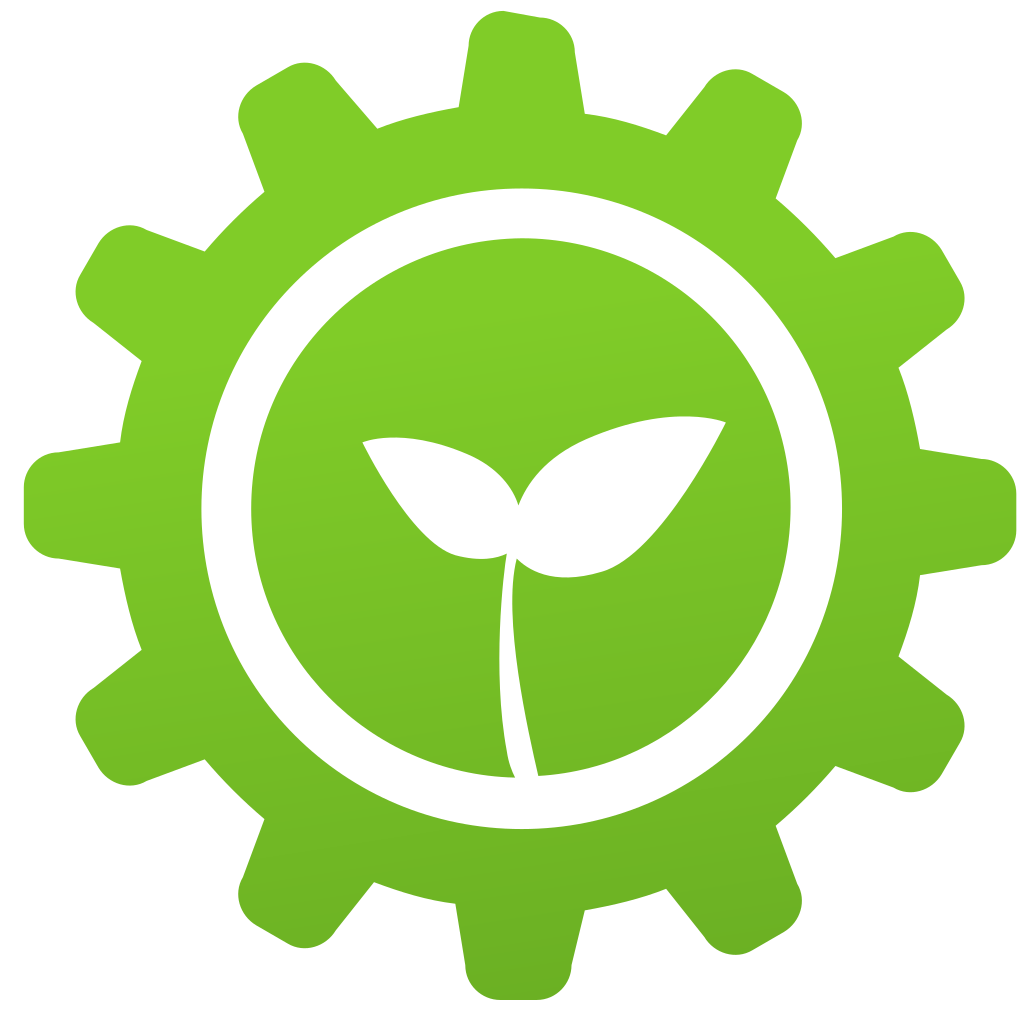
Chemical Industry could go totally carbon neutral
Summary
Switzerlands Federal Council has decided that the country should become carbon-neutral by 2050. Study: The goal of achieving net-zero CO2 emissions in the chemical industry is in fact attainable. All three concepts require more energy (in the form of electricity) than current production methods. A final option would be to use biomass (wood, sugar plants, oil plants) as raw material. The research project had funding from the Swiss Competence Center for Energy Research—Efficiency of Industrial Processes (SCCER-EIP)
It also informs the discussion about future aircraft fuels, Marco Mazz
The study shows that there are at least two viable alternatives to synthetic fuels: aviation could continue to use fossil fuels if the CO2 aircraft emitted were captured and sequestered elsewhere, or the fuels could be obtained from biomass. Mazzotti and the Swiss Federal Office of Energy Research has funding from SCCER.ORG and the PSI.
Open full article
Chemical Industry could go totally carbon neutral
The chemical industry could become carbon neutral, new research indicates.
Switzerland’s Federal Council has decided that the country should become carbon-neutral by 2050. This may be challenging as far as car traffic and the entire power sector are concerned, but not impossible—with systematic electrification and the exclusive use of carbon-neutral energy sources, for example.
A switch of this kind will be more difficult for the chemical industry. While for many other industrial sectors one of the primary concern is their energy efficiency, the chemical industry must also address the question of raw materials.
“Polymers, plastics, synthetic textile fibers, and medicines all contain carbon. It has to come from somewhere,” explains Marco Mazzotti, professor of process engineering at ETH Zurich. As things stand, the vast majority of this carbon comes from oil and natural gas. During production, and when the chemical products are burned or decompose at the end of their life, they release CO2.
Using concrete figures and methanol production as a case study, Mazzotti and colleagues from ETH Zurich and Utrecht University have now systematically compared various approaches that aim at reducing net CO2 emissions from the chemical industry to zero. The main conclusion from the new study is that the goal of achieving net-zero CO2 emissions in the chemical industry is in fact attainable.
All the approaches the study examined for achieving this target, however, have both advantages and disadvantages, which manifest themselves differently in different regions of the world. In addition, all three concepts require more energy (in the form of electricity) than current production methods.
The researchers’ three proposed methods are as follows:
- One approach involves continuing to use fossil resources as raw materials, but systematically capturing CO2 emissions and sequestering them underground using a process known as carbon capture and storage (CCS). The big advantage here is that today’s industrial production processes would not need to be changed. However, the storage sites must be suitable in terms of their geology, offering for example deep sedimentary layers that contain salt water. Such sites are not found all over the world.
- Another approach would see industry using carbon from CO2 captured in advance from air or from industrial waste gases. This process is called carbon capture and utilization (CCU). Hydrogen required for chemical products could be obtained from water using electricity. The approach would involve a major overhaul of chemical production processes and rebuilding large parts of the industrial infrastructure. In addition, it requires an extremely large amount of electricity—six to ten times more than CCS.”This method can be recommended only in countries with a carbon-neutral electricity mix,” Mazzotti explains. “We clearly demonstrate that using large quantities of electricity from coal or gas-fired power stations would, in fact, be much worse for the climate than the current production method based on fossil fuels.”
- A final option would be to use biomass (wood, sugar plants, oil plants) as raw material for the chemical industry. Although this method requires less electricity than the others, it involves very intensive land use to grow the crops—requiring 40–240 times more land than the other approaches.
Mazzotti and his coauthors based their study on the production of methanol, which is similar to the process used for producing fuels.
Their work therefore also informs the discussion about future aircraft fuels, Mazzotti says. “We hear it time and again, even from experts, that the only way aviation can become carbon-neutral is through the use of synthetic fuels,” he says. “But that’s not true.”
Producing synthetic fuels is an extremely energy-intensive process. If electricity from coal or gas-fired power stations were to be used for this purpose, synthetic fuels would have an even larger carbon footprint than fossil fuels. The study shows that there are at least two viable alternatives to synthetic fuels: aviation could continue to use fossil fuels if the CO2 aircraft emitted were captured and sequestered elsewhere, or the fuels could be obtained from biomass.
The research appears in Industrial and Engineering Chemistry Research.
This research project had funding from the Swiss Competence Center for Energy Research—Efficiency of Industrial Processes (SCCER-EIP) and the Swiss Federal Office of Energy.
Source: ETH Zurich via FUTURITY.ORG
Original Study DOI: 10.1021/acs.iecr.9b06579