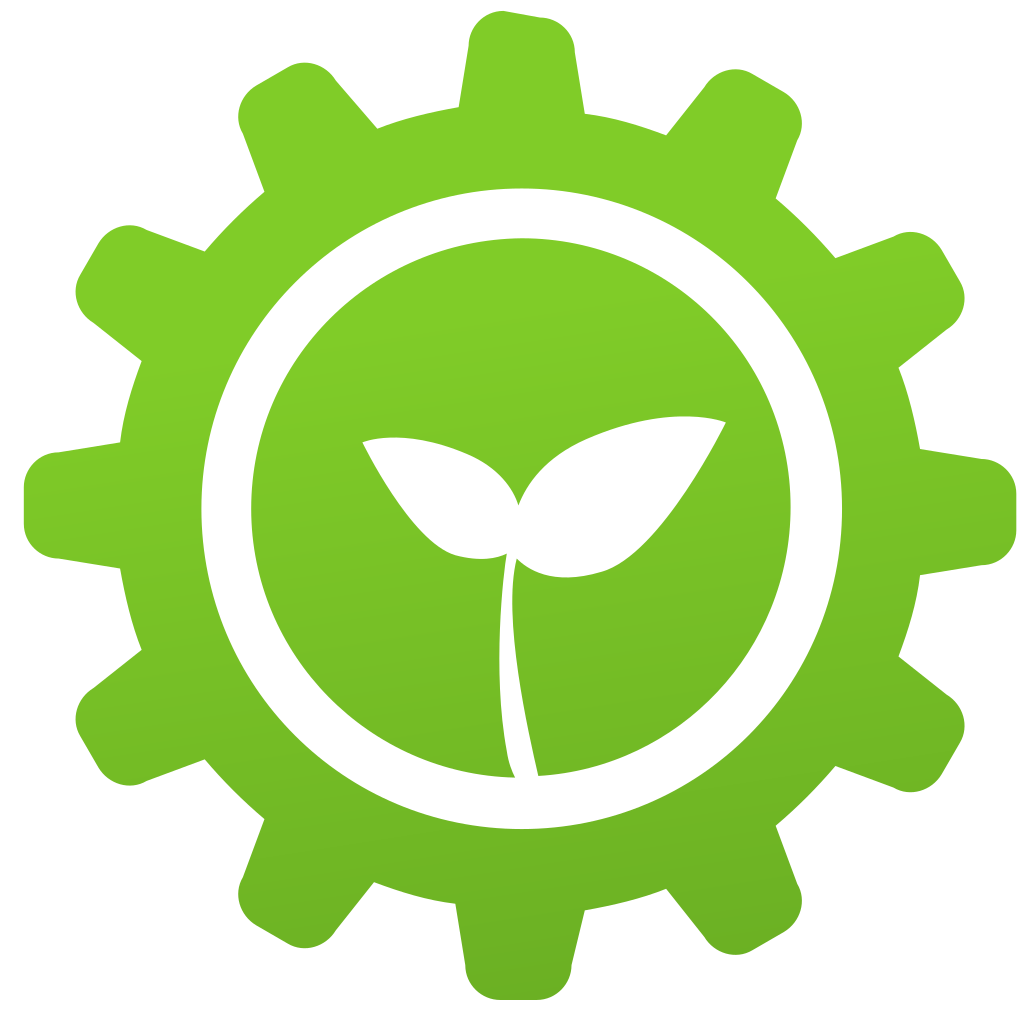
Digital Solutions for Energy Efficiency in Industry
Summary
The International Energy Agency's 4E Technology Collaboration Programme on Energy Efficient End-Use Equipment (4E TCP) report discusses the role of digital solutions in enhancing energy efficiency in motor systems across various industries. The implementation of simulation-based tools for production planning has enabled Smurfit Kappa in Sweden to lower energy intensity for paper production by 9% between 2017 and 2023. In Switzerland, Hamilton Bonaduz AG's integration of an adaptive air pressure management system in their compressed air systems resulted in a 16% reduction in electric energy consumption. Utilizing digital technologies outside operational hours allowed INNIO Jenbacher in Austria to decrease energy and compressed air use by about 30% on weekends. Coca-Cola HBC Austria achieved a 15% reduction in energy demand during normal operation with demand-based ventilation controls. BMW's Steyr plant in Austria utilized data acquisition and monitoring to reduce electrical and compressed air baseloads by 52% and 14%, respectively. Yorkshire Water in the UK applied electrical signature analysis to successfully manage pump operations and expect energy and CO2 savings up to 15%. Additionally, IoT solutions like PRiOT's sensor technology led to a 20% reduction in energy consumption by optimizing air filter maintenance at server sites. While digital solutions offer substantial benefits, companies need to address challenges such as investment costs, staff training, and process disruptions. Tailored strategies, comprehensive analysis, and continuous monitoring are essential for maximizing energy efficiency. Improvements in technology, such as artificial intelligence and machine learning, hold promise for future advancements in industrial energy optimization, potentially integrating with renewable energy sources.
Open full article
Digital Solutions for Energy Efficiency in Industry
In an era of increasing energy costs and growing environmental concerns, industries worldwide are seeking innovative ways to optimize their energy consumption. A recent report by the International Energy Agency's Technology Collaboration Programme on Energy Efficient End-Use Equipment (4E TCP) highlights several case studies where digital solutions have enabled significant energy savings in motor systems across various industries. These examples demonstrate how the integration of smart technologies can lead to substantial improvements in energy efficiency, operational flexibility, and cost savings.
The Power of Data-Driven Decision Making
One standout case involves Smurfit Kappa, a major producer of kraft paper liner in Sweden. The company implemented a simulation-based tool for production planning that utilizes real-time data instead of relying solely on historical information and experience-based decisions. This shift to data-driven planning has resulted in higher operational flexibility, lower electricity consumption, smoother plant operations, and reduced maintenance costs. Remarkably, the energy intensity for paper production decreased by 9% between 2017 and 2023, showcasing the tangible benefits of embracing digital solutions in industrial processes.
Intelligent Control Systems: A Game-Changer for Compressed Air
Compressed air systems, often referred to as the "fourth utility" in industrial settings, present significant opportunities for energy savings. The case of Hamilton Bonaduz AG in Switzerland illustrates how digital technologies can revolutionize these systems. By implementing an adaptive air pressure management system combined with a mix of compressors with and without variable speed drives, the company achieved a 16% reduction in electric energy consumption for compressed air production.
Similarly, INNIO Jenbacher in Austria leveraged digital solutions to optimize their compressed air usage during non-operational hours. By setting new thresholds for energy and compressed air demand during weekends and implementing a comprehensive monitoring system, the company reduced its weekend energy and compressed air consumption by approximately 30%. This achievement translates to annual savings equivalent to the energy consumption of about 200 households.
Ventilation Systems: Breathing New Life into Energy Efficiency
Ventilation systems, crucial for maintaining air quality in industrial settings, often consume substantial amounts of energy. Coca-Cola HBC Austria demonstrates how integrating ventilation systems into a building management system can lead to significant energy savings. By equipping ventilation systems with variable speed drives and implementing demand-based control strategies, the company reduced energy demand during normal operation by about 15%. This project, with a payback period of less than three years, underscores the economic viability of such digital upgrades.
Monitoring and Control: The Key to Unlocking Savings
The power of monitoring and control systems is evident in the case of BMW's plant in Steyr, Austria. The company established a comprehensive data acquisition and monitoring system covering electricity and compressed air consumption. By visualizing energy consumption at the production line level and setting baseload targets for non-production times, BMW achieved remarkable results. The electrical baseload was reduced by 52%, while the compressed air baseload saw a 14% reduction.
Yorkshire Water in the United Kingdom provides another compelling example of how advanced monitoring can drive energy efficiency. The company implemented electrical signature analysis (ESA) for condition monitoring of its pumps. This technology allows for real-time energy and performance insights, enabling the elimination of unplanned downtime and energy waste. The project, covering 4,000 assets monitored 24/7, is expected to yield energy and CO2 emission savings of up to 15%.
IoT Solutions for Targeted Optimization
The Internet of Things (IoT) is opening new avenues for energy optimization in specific applications. PRiOT, a Swiss company, deployed IoT sensors to detect clogged air filters in ventilation systems at server sites. This solution allows for more accurate timing of filter replacements, resulting in energy savings, reduced maintenance needs, and extended filter lifespans. In one instance, this approach led to a 20% reduction in electric energy consumption.
Challenges and Considerations
While the benefits of digital solutions for energy efficiency are clear, implementing these technologies is not without challenges. Companies must consider factors such as initial investment costs, the need for staff training, and potential disruptions to existing processes. However, the case studies demonstrate that with proper planning and execution, these hurdles can be overcome, and the returns can be substantial.
Furthermore, it's important to note that digital solutions are not a one-size-fits-all approach. Each industry and facility has unique characteristics that require tailored solutions. The success stories highlighted in the report emphasize the importance of thorough analysis, strategic implementation, and continuous monitoring to achieve optimal results.
The Future of Industrial Energy Efficiency
As digital technologies continue to evolve, the potential for further energy efficiency gains in industrial settings is immense. Artificial intelligence and machine learning are poised to play increasingly significant roles in optimizing energy consumption by predicting maintenance needs, automating complex processes, and identifying new opportunities for efficiency improvements.
Moreover, the integration of renewable energy sources and energy storage systems with these digital solutions could pave the way for even more sustainable industrial operations. As companies strive to meet ambitious carbon reduction targets, the synergy between digital technologies and clean energy will likely become a focal point for future innovations.
In conclusion, the case studies presented by the 4E TCP Electric Motor Systems Platform demonstrate that digital solutions are not just theoretical concepts but practical, implementable strategies that can deliver substantial energy savings and operational improvements. As industries worldwide face the dual challenges of reducing energy costs and minimizing environmental impact, embracing these digital technologies will be crucial for staying competitive in an increasingly energy-conscious global market. The success stories from companies like Smurfit Kappa, Hamilton Bonaduz AG, and BMW serve as powerful examples of what can be achieved when traditional industrial processes are enhanced with cutting-edge digital solutions.