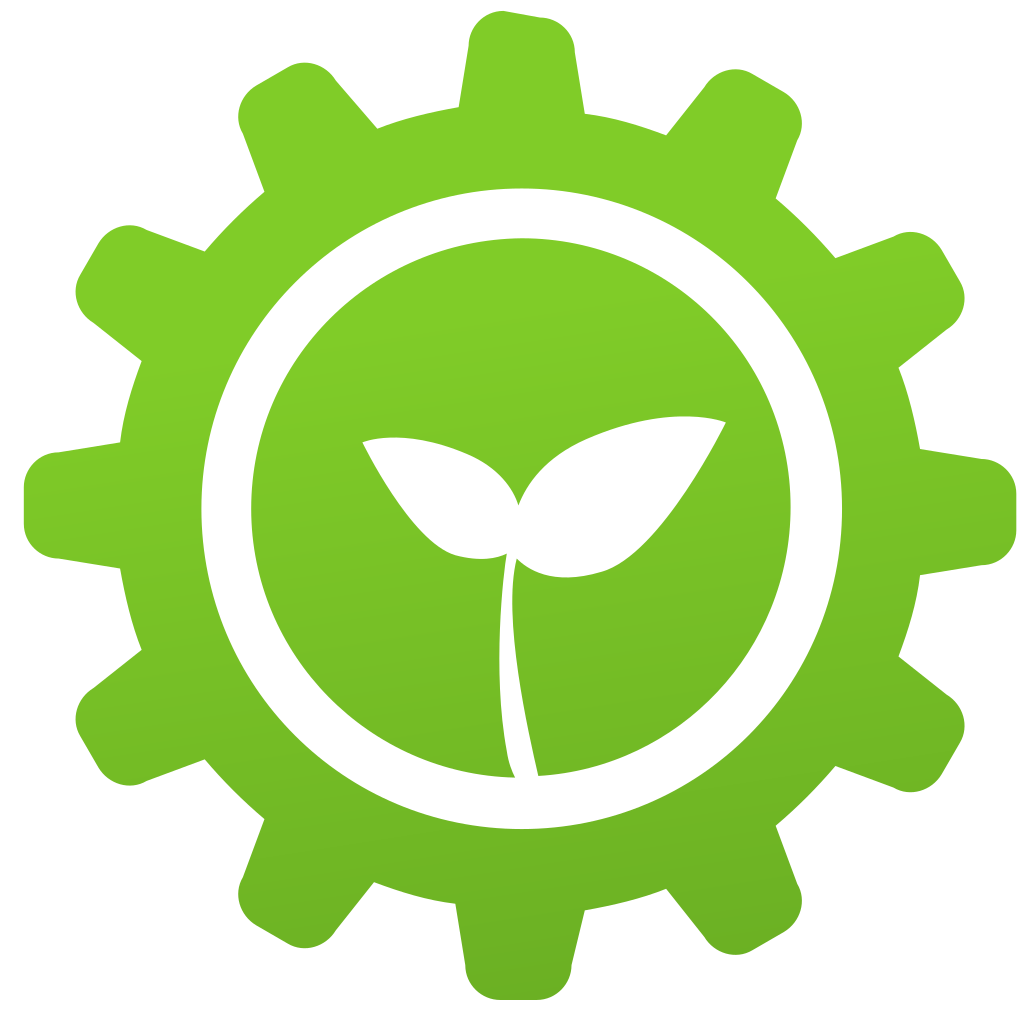
Industrial heat: An emission free energy source
Summary
There is 20-50% of the energy consumed by US industry is ultimately lost as heat. Many facilities around the world can increase their overall effciency and bottom lines by installing waste heat recovery technologies. Waste heat recovery can enhance pro?tability in the industrial sector and improve competitiveness. One of the?rst steps in initiating a heat recovery project is understanding the quality and quantity of heat available. HeatCalc, we are doing for waste heat what the solar industry has done for calculating home solar output: automating estimates, maximizing knowledge sharing, and streamlining connections to the most relevant solution providers
Our goal is to enable more waste heat utilization projects, which make the most out of energy we are already consuming. There are CHP (combined heat and power) projects delivering electricity and heat to hospitals, campuses, and industrial facilities that use waste heat to power projects that use the energy we already consume. We hope you can save time and money in the process.
Open full article
Industrial heat: An emission free energy source
Heat is a form of energy that is all around us. There’s heat from the sun (solar thermal), and from the earth (geothermal), but for this post, I want to talk about industrial heat - heat that is a byproduct of manufacturing, re?ning, smelting, generating electricity, etc. - and its many bene?cial uses.
There’s a lot of industrial heat
20-50% of the energy consumed by US industry is ultimately lost as heat, which equals 5 to 13 quadrillion BTU per year of unused energy (US DOE). For perspective, that’s somewhere between the entire energy consumption of Turkey and Germany (EIA).I’d like to note that this is not an indication of unusual waste at the facilities, but more an indication of the large size of US industry. Other countries would likely have similar ratios of heat available.
While some waste heat losses are inevitable and unavoidable, many facilities around the world can increase their overall effciency and bottom lines by installing waste heat recovery technologies.
Heat utilization options
Waste heat comes in many forms, including exhaust heat, hot air, water and steam. Once the heat is recovered or captured, typically with a heat exchanger, there are 3 primary options for putting it to more effcient use:
- For heating (e.g. fuel pre-heating, space heating, water heating, etc.)
- For cooling (e.g. air conditioning or refrigeration with absorption chillers)
- For generating electricity (e.g. rankine cycle, thermoelectrics, etc.)
![]() |
---|
Economic and environmental benefits
All of the options above represent emission free substitutes for costly purchased fuels or electricity. Accordingly, heat utilization can reduce the operating costs, potentially the capital costs (by displacing boilers or chillers), and carbon footprint of a business simultaneously.
The World Bank commissioned a study on waste heat recovery in the cement industry and found the that deploying waste heat recovery had signi?cant environmental and economic benefits for the cement plants. “Waste Heat Recovery can reduce the operating costs and improve EBITDA margins of cement factories by about 10 to 15 percent.” - International Finance Corporation (IFC) The study also notes that waste heat recovery “improves plant competitive position in the market” (IFC). I’ve also seen benefits first hand at sawmills, steel plants, power generation plants, oil re?neries, and other industrial facilities.
Waste heat recovery can enhance pro?tability in the industrial sector and improve competitiveness. It helps governments meet ef?ciency and/or clean power standards. It creates local jobs with the installation and operation of the equipment. And, because the energy is both produced and consumed on site or nearby, it’s a distributed energy resource that can reduce peak energy loads and strain on the grid.
![]() |
---|
Projects
So why aren’t more heat utilization projects occurring? Many are. There are CHP (combined heat and power) projects delivering electricity and heat to hospitals, campuses, and industrial facilities. Absorption chillers use waste heat to provide cooling at warehouses, malls and food storage facilities. Heat to power projects generate electricity at cement plants and small wood stoves charge cell phones in remote villages.
But with all that heat energy available, there could be more. One of the barriers to enabling projects is access to information and immediate feedback on individual heat sources. Industrial heat comes from an array of sources (engines, boilers, kilns, furnaces, turbines, ?ares, incinerators, ovens, etc.) and each source has a different heat makeup, which affects what you can do with it.
Overcoming project barriers
One of the ?rst steps in initiating a heat recovery project is understanding the quality and quantity of heat available. Estimating the quantity of heat in your heat source used to be a bit like estimating solar output on a home’s roof: it required getting in touch with a solar manufacturer or an engineer in the industry to crunch the numbers. Today, you can plug your address into a site like NREL’s and get an instant solar output estimate (NREL).
At HeatCalc, we are doing for waste heat what the solar industry has done for calculating home solar output: automating estimates, maximizing knowledge sharing, and streamlining connections to the most relevant solution providers. Anyone that has a heat source - from air compressors to large kilns and exhaust stacks can get feedback on their heat source for free and discover ways they can utilize their heat that save time and money. Most importantly, based on your unique heat source we can connect you to the most relevant solution providers, saving you time and money in the process. Our goal is to enable more waste heat utilization projects, which make the most out of the energy we are already consuming.