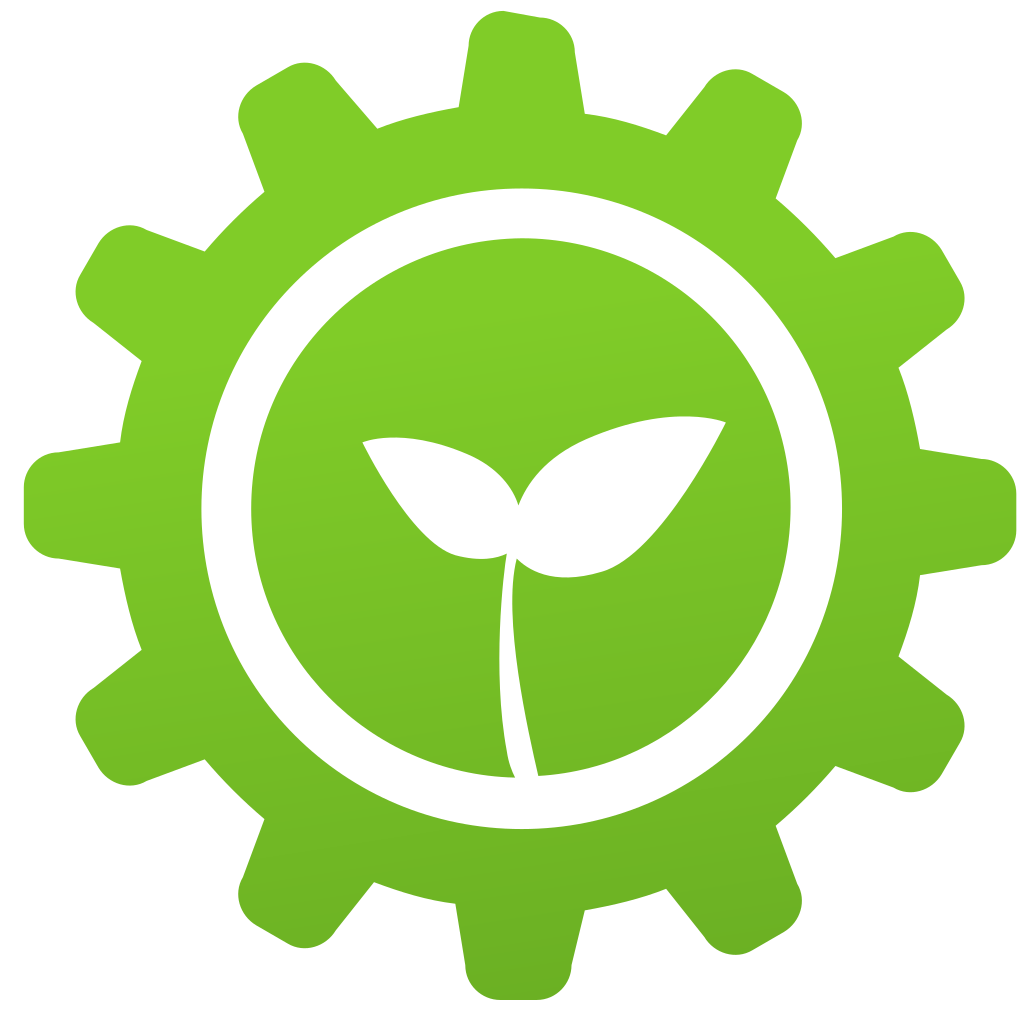
Top 5: How to increase energy efficiency of pumps – start with the system
Summary
Pumps currently account for 10% of the world's total electricity consumption. Pumps are designed to meet many requirements, energy efficiency not always being one of them. Some plants are built with poor system design where pumps are not properly matched to the system. Bad plant layout resulting in inefficient routing of pipes frequently exacerbates the situation as well. Existing systems are often modified to optimise suction head, gather measurement information or change suction and/or discharge flanges. variable speed pumping solutions can be retrofitted into a system already in service. Throttle valves, pressure relief mechanisms and flow bypass
bypasses used for control will all reduce operating efficiency and increase energy consumption. Additional costs may be caused by cooling or heating circuits, liquid flush lines or fluid barrier arrangements. A systems overall frictional resistance can be minimised and the monetary savings maximised if attention is paid to reduce energy costs. Click here for more information on how to read more.
Open full article
Top 5: How to increase energy efficiency of pumps – start with the system
Top 5: How to increase energy efficiency of pumps – start with the system
Everybody knows that pumps consume a lot of energy. But do you know that pumps currently account for 10% of the world´s total electricity consumption?
Here is an overview of Top 5 approaches to reduce energy consumption.
- System Planning
- Pumps
- Impellers
- Motors
- Drives
System Planning
Pumping systems are designed to meet many requirements, energy efficiency not always being one of them. As a result, some plants are built with poor system design where pumps are not properly matched to the system, pipe diameters are incorrectly sized and flow velocities are too high. Bad plant layout resulting in inefficient routing of pipes frequently exacerbates the situation as well.
As all these factors increase frictional resistance, larger pumps than necessary are needed to deliver liquid to the required service.
Existing systems
Changing a running system already in place is often difficult. Sometimes pumps, valves and measuring instruments are modified, for example to optimise a system’s available net positive suction head (NPSH), gather measurement information or change suction and/or discharge flanges, when retrofitting differently sized new pumps. Due to the heavy expenditure for engineering and materials, such modifications are usually limited in scale and often have little impact on the energy efficiency of an existing system.
One significant exception is to employ variable speed pumping solutions that can be retrofitted into a system already in service. Another viable option is to check whether any duty points can be subsequently rescaled, because each system is designed with safety margins added to the calculated system curves to ensure that sufficiently large pumps are selected for the job. As a result, the pumps installed are often oversized and then operate at excessive flow rates or in throttled conditions, increasing energy usage and reducing pump life.
New systems
Competent planning of new pumping systems to minimise energy consumption is one of the keys to reducing life cycle costs (LCC). Some energy use may not be output-dependent. For example, a control system sensing output changes may itself generate a constant energy load, whereas a variable speed drive can consume different levels of energy at different operating settings. Throttle valves, pressure relief mechanisms and flow bypasses used for control will all reduce operating efficiency and increase energy consumption. Additional costs may be caused by cooling or heating circuits, liquid flush lines or fluid barrier arrangements. While such costs often do not vary for different types of systems, they can be influenced by the selection of materials and designs.
Carefully selected pumping systems will reduce energy costs. A system’s overall frictional resistance can be minimised and the monetary savings maximised if attention is paid to the following points:
- Pumps must be optimally matched to the system in an early stage.
- Variable speed drives should be chosen, pipe diameters and distances correctly selected and flow velocities optimally designed for each position where they will help reduce energy consumption.
How this looks in practice?
Here is a presentation from CP Pumps on the impact of focussing on the system as a whole. Smart Engineering of Pump Systems in chemcial processes
Let us know what you think. Do you have any great examples of how you improved energy efficiency while saving cost?
Coming soon: Top 2-5 (Pumps and impellers, motors and drive)
Sources: CP Pumps, Grundfos: MEET THE ENERGY CHALLENGE