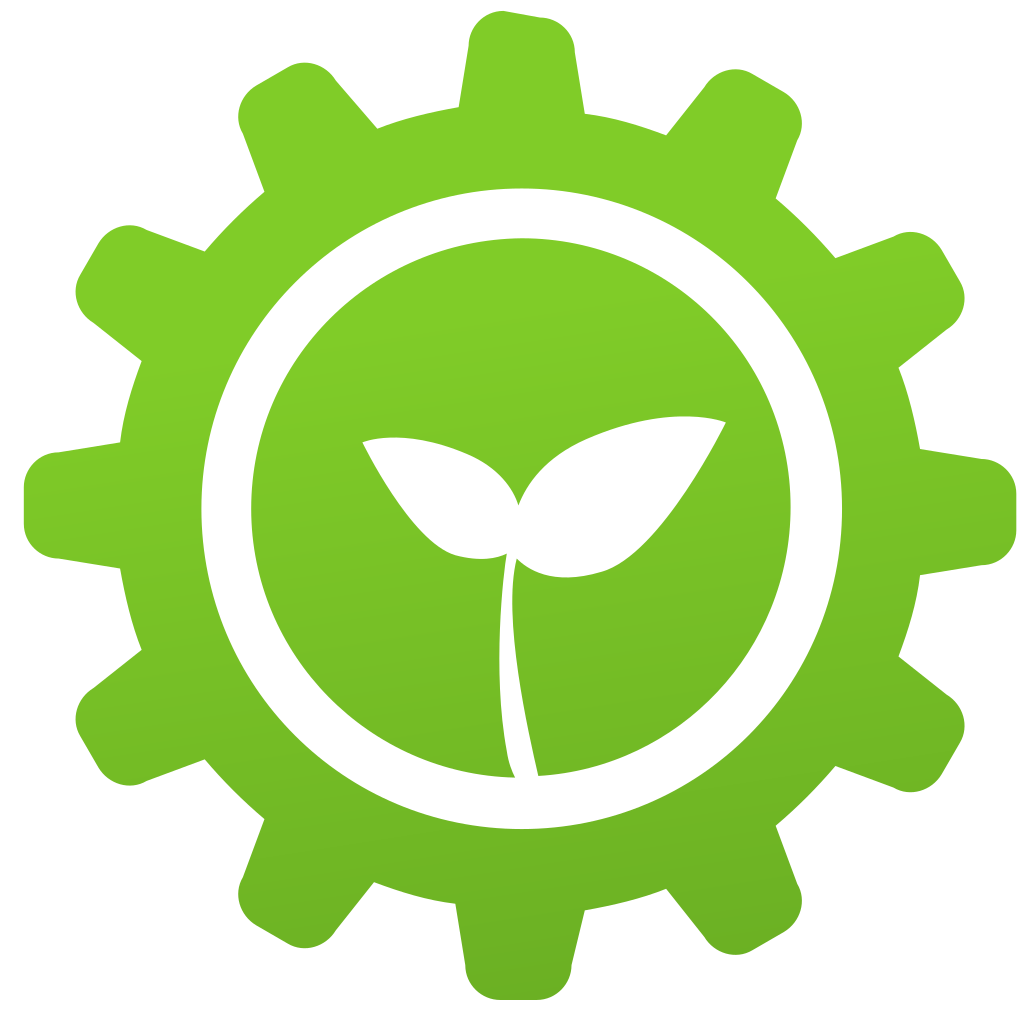
Choisir les meilleures techniques de récupération de la chaleur perdue
Résumé
Le gouvernement britannique a reconnu, dans sa feuille de route sur la décarbonisation industrielle et l'efficacité énergétique à l'horizon 2050, que le coût de l'étude de faisabilité pour les industries à forte consommation d'énergie est considérable. Le ministère des affaires, de l'énergie et de la stratégie industrielle devrait lancer la première phase du programme de soutien à la chaleur industrielle dans le courant de l'année.
Il y a un intérêt croissant pour les solutions WHR pour la fabrication du verre et la pression des parties prenantes pour décarboniser le secteur ; il y a un.
intérêt croissant. En novembre, la Confédération britannique de la fabrication du verre a organisé un atelier de transfert de connaissances sur le WHR auquel ont participé de nombreux représentants d'entreprises de haut niveau, désireux de s'impliquer dans la décarbonisation du secteur.
Le conseil d'administration a besoin d'un document de qualité pour décider si le projet doit être financé directement par le budget des dépenses d'investissement ou par un financement externe dans le cadre d'un contrat d'achat d'électricité (CAE).
Le gouvernement britannique a reconnu que le . Cost for EnergyIntensive Industries is substantial. le coût pour. le projet est substantiel et le projet sera financé par le projet.
Ouvrir l'article complet
Choisir les meilleures techniques de récupération de la chaleur perdue
Choisir les meilleures techniques de récupération de la chaleur perdue
Darren Bryant, PDG de Heatcatcher UK, parle des meilleures techniques de récupération de la chaleur résiduelle disponibles pour l'industrie du verre et présente les initiatives du gouvernement britannique pour aider les fabricants à obtenir des financements.
Heatcatcher a commencé à concevoir, construire et exploiter des systèmes de récupération de la chaleur résiduelle (WHR) dans l'industrie de la chaux et du ciment, mettant en service sa première usine utilisant la technologie du cycle de Rankine organique (ORC) en 2013 en récupérant les gaz d'échappement d'un four rotatif pour générer 0,5 MW d'électricité pour le site britannique de Lhoist près de Durham.
Les possibilités et les défis liés à l'intégration des meilleures techniques disponibles de récupération de la chaleur résiduelle dans les fours de verre flotté et de verre creux sont similaires à ceux de l'industrie de la chaux et du ciment, sauf que le retour sur investissement est amélioré car les heures de fonctionnement annuel des fours de verre sont plus élevées.
Tous les secteurs industriels à forte intensité énergétique sont confrontés à une augmentation des prix de l'énergie et l'équipe d'ingénieurs de Heatcatcher a appliqué ses connaissances et son expérience pour égaler les meilleures technologies disponibles en matière de CRO et de détendeur de vapeur afin de récupérer l'énergie thermique des gaz d'échappement des fours à verre.
Avec le renforcement de la législation environnementale visant à limiter les émissions de gaz d'échappement, les usines prévoient des coûts d'investissement plus élevés pour les équipements supplémentaires de traitement des gaz de combustion (FGT).
Ces derniers sont souvent nécessaires pour fonctionner avec des températures de gaz d'échappement plus basses et un refroidissement supplémentaire est donc nécessaire. Le coût des nouveaux équipements FGT et des équipements de refroidissement pour abaisser la température peut être atténué par un système WHR, qui élimine la chaleur et la convertit en électricité à faible teneur en carbone avant l'équipement FGT.
Intégration du WHR
La sélection des meilleures techniques disponibles (MTD) pour l'intégration des échangeurs de chaleur et leur mise en correspondance avec les meilleurs ORC ou élargisseurs de vapeur disponibles dans le commerce est un domaine d'expertise crucial pour répondre aux conditions techniques et économiques d'un projet d'intégration de RSF.
Les considérations techniques comprennent :
- Quelle est la variabilité de la température et du débit massique des gaz d'échappement ?
- Quelle est la composition chimique des gaz d'échappement qui limite la température minimale de fonctionnement ?
- Les contraintes d'espace de l'usine déterminent l'emplacement de l'échangeur de chaleur et l'intégration des conduits.
- Les conduits changent si l'on combine les flux de gaz d'échappement de plus d'un four.
- Méthode de nettoyage des échangeurs de chaleur et chute de pression du système.
- Effet supplémentaire de la chute de pression du système WHR sur le processus et le ventilateur à tirage induit.
- Variation de la vitesse d'écoulement de la cheminée d'échappement due à l'abaissement de la température.
- Demandes futures concernant la réduction des limites d'émissions et le traitement des gaz de combustion.
Valeur économique du système WHR
Une fois que les aspects techniques de l'intégration sont évalués, les considérations économiques sur la manière d'obtenir la plus grande valeur pour la durée de vie typique de 15 à 20 ans d'un système de RHS sont prises en compte.
La valeur réside-t-elle dans la production de grandes quantités d'eau chaude, une petite quantité étant destinée à l'utilisation du site et le reste étant vendu par-dessus la clôture à une usine voisine ou à un système de chauffage urbain ?
Trouver un hôte voisin pour consommer de grandes quantités d'eau chaude est un défi commercial et le raccordement à un réseau de chauffage urbain planifié peut bénéficier d'incitations de la part des autorités locales mais peut être un long processus.
La conversion de la chaleur récupérée en électricité à faible teneur en carbone ou en une combinaison d'électricité et d'une petite quantité de chaleur pour l'utilisation du site a été le choix préféré des verreries qui exploitent des systèmes de chauffage urbain.
Les systèmes de récupération de chaleur en fonctionnement comprennent le générateur ORC de 1,3 MWe installé en 2013 à l'usine de verre plat AGC à Cuneo, en Italie ; le générateur ORC de 0,5 MWe à l'usine de récipients O-I Glass à Villotta di Chions, en Italie ; le générateur de cycle de vapeur Guardian Glass en cours d'installation à l'usine de verre flotté de Goole au Royaume-Uni ; le générateur ORC de 5,5 MWe à l'usine Sisecam en Bulgarie ; et le détendeur à vis à vapeur de 0,4 MWe installé à l'usine Vetrobalsalamo à Milan, en Italie.
Résumé
Avec un besoin accru d'atténuer la hausse des coûts énergétiques de la fabrication du verre et la pression des parties prenantes pour décarboniser le secteur, il y a un intérêt croissant pour les solutions de RSM.
Par exemple, en novembre, la Confédération britannique de la fabrication du verre a organisé un atelier de transfert de connaissances sur les RSF auquel ont participé de nombreux représentants de haut niveau des entreprises, désireux de comprendre les systèmes de RSF.
Bien que de nombreux aspects de l'intégration technique doivent être satisfaits par une étude de faisabilité avant qu'une analyse de rentabilité puisse être présentée au conseil d'administration, un document de qualité investissement est nécessaire pour que le conseil puisse décider si le projet doit être financé directement par son budget de dépenses d'investissement ou par un financement externe dans le cadre d'un accord d'achat d'électricité (PPA) ou d'un contrat de services énergétiques (ESCo).
Le gouvernement britannique a reconnu, dans sa "Feuille de route pour la décarbonisation industrielle et l'efficacité énergétique à l'horizon 2050", que le coût de la préparation de l'étude de faisabilité par les industries à forte intensité énergétique est considérable.
Le ministère de la stratégie énergétique et industrielle des entreprises devrait lancer la première phase du "Programme de soutien à la chaleur industrielle" dans le courant de l'année, en offrant un soutien financier pouvant aller jusqu'à 40 % pour ces études de faisabilité.
La deuxième phase du PSSI en 2018 pourrait financer jusqu'à 30 % des coûts d'investissement pour la mise en œuvre des meilleurs projets identifiés à partir des études de faisabilité.
(Publié initialement ici)