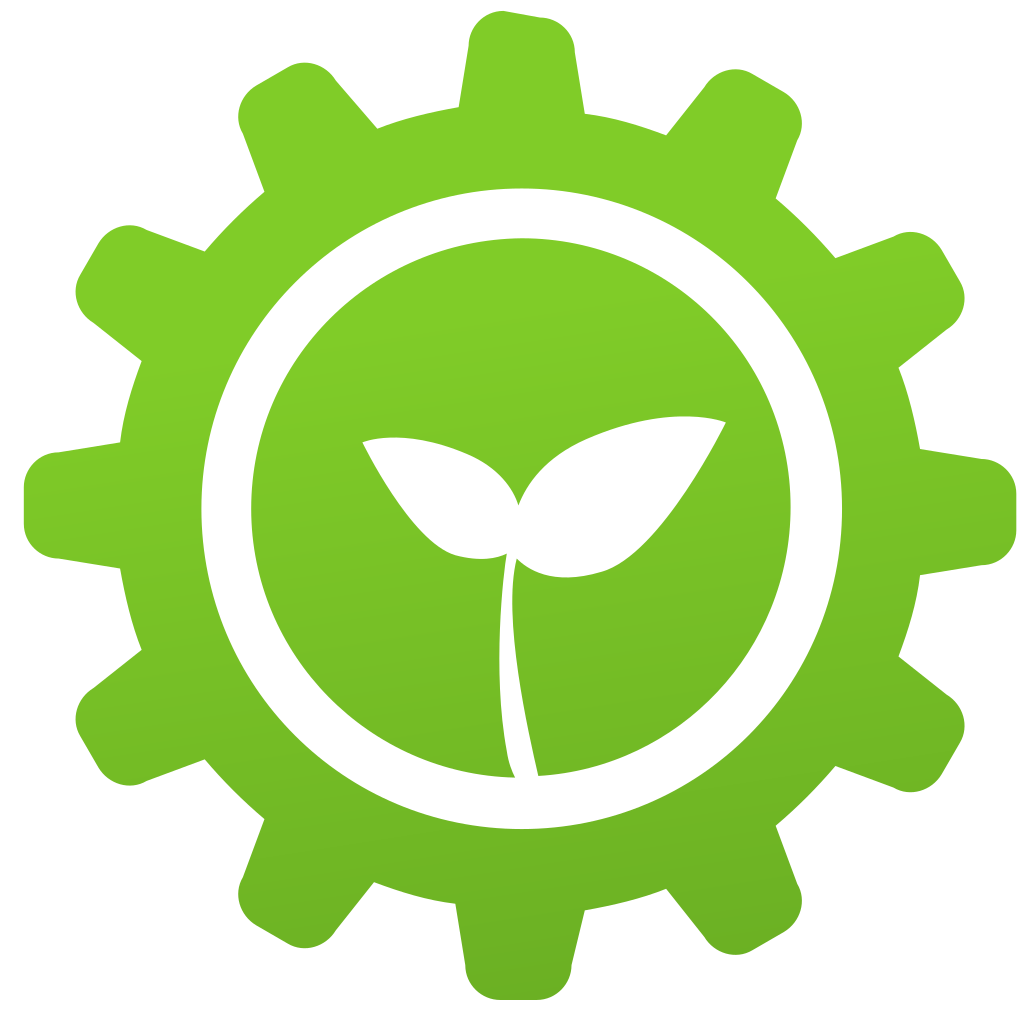
Choosing the best techniques for waste heat recovery
Summary
The UK government has recognised through its ‘Industrial Decarbonisation and Energy efficiency Roadmap to 2050’ that the cost for Energy Intensive Industries to prepare the feasibility study is substantial. The department for Business Energy and Industrial Strategy is expected to launch the first phase of the ‘ industryrial Heat Support Programme later this year’
There is a growing interest in WHR solutions for glass manufacturing and stakeholder pressure to decarbonise the sector there is a.
growing interest. In November the British Glass Manufacturing Confederation hosted a Knowledge Transfer workshop on WHR that was attended by many senior company representatives, keen
An investment grade document is needed for the board to decide if the project is to be directly funded from their capital expenditure budget or externally funded under a Power Purchase Agreement (PPA)
The UK Government has recognised that the. Cost for EnergyIntensive Industries is substantial. the cost for. the project is substantial and the project will be funded by the project.
Open full article
Choosing the best techniques for waste heat recovery
Choosing the best techniques for waste heat recovery
Darren Bryant, CEO of Heatcatcher UK, discusses best available waste heat recovery techniques for the glass industry and outlines UK government initiatives to help manufacturers with funding.
Heatcatcher started designing, building and operating Waste Heat Recovery (WHR) systems in the lime and cement industry, commissioning its first plant using Organic Rankine Cycle (ORC) technology in 2013 by recovering the exhaust gases from a rotary kiln to generate 0.5MW of electricity for the UK Lhoist site near Durham.
The opportunities and challenges of integrating the best available waste heat recovery techniques into the float and container glass furnaces are similar to the lime and cement industry, except the return on investments are improved because the annual operating hours of the glass furnaces are higher.
All energy intensive industry sectors face increased energy prices and the Heatcatcher team of engineers have applied their knowledge and experience to match the best available ORC and steam expander technologies to recover the heat energy from glass furnace exhausts.
With increased environmental legislation to limit exhaust gas emissions, plants anticipate higher capital costs of additional flue gas treatment (FGT) equipment.
These are often required to operate with lower exhaust gas temperatures and so additional cooling is required. The cost of new FGT equipment and cooling equipment to lower the temperature can be mitigated by a WHR system, removing the heat and converting to low carbon electricity prior to the FGT equipment.
WHR integration
Selecting the Best Available Techniques (BAT) for heat exchanger integration and matching it to the best commercially available ORC or Steam Expander is an area of expertise crucial to meeting the technical and economic conditions of a WHR integration project.
Technical considerations include:
- How variable is the temperature and mass flow rate of the exhaust gas?
- What is the exhaust gas chemical composition limiting the minimum operating temperature?
- Plant space constraints determining heat exchanger location and ductwork integration.
- Ductwork changes if combining exhaust streams of more than one furnace.
- Heat exchanger cleaning method and pressure system pressure drop.
- Additional WHR system pressure drop effect on process and induced draft fan.
- Variation in exhaust stack efflux velocity from lowering the temperature.
- Future demands on reduced emissions limits and flue gas treatment.
WHR economic value
Once the technical aspects of integration are assessed then the economic considerations of how to gain the greatest value for the typical 15 to 20 year life of a WHR system.
Is the value in producing large quantities of hot water, with a small amount for site usage and the rest to be sold over the fence to a neighbouring plant or a district heating system?
Finding a neighbouring host to consume large quantities of hot water is commercially challenging and the connection to aplanned District Heating Network may receive local government incentives but can be a lengthy process.
Converting the recovered heat to all low carbon electricity or a combination of electricity and a small amount of heat for site usage has been the preferred choice of glass plants that operate WHR systems.
WHR systems in operation include the 1.3MWe ORC generator installed in 2013 at the AGC flat glass plant in Cuneo, Italy; the 0.5MWe ORC generator at the O-I Glass container plant in Villotta di Chions, Italy; the Guardian Glass steam cycle generator being installed at the Goole float glass plant in the UK; the 5.5MWe ORC generator at the Sisecam plant in Bulgaria; and the 0.4MWe steam screw expander installed at the Vetrobalsalamo plant in Milan, Italy.
Summary
With an increased need to mitigate against rising energy costs of glass manufacturing and stakeholder pressure to decarbonise the sector there is a growing interest in WHR solutions.
For example, in November the British Glass Manufacturing Confederation hosted a Knowledge Transfer workshop on WHR that was attended by many company senior representatives, keen to understand about WHR systems.
While many of the technical integration aspects must be satisfied with a feasibility study before a business case can be presented to the board, an investment grade document is needed for the board to decide if the project is to be directly funded from their capital expenditure budget or externally funded under a Power Purchase Agreement (PPA) or Energy Services Contract (ESCo).
The UK government has recognised through its ‘Industrial Decarbonisation and Energy Efficiency Roadmap to 2050’ that the cost for Energy Intensive Industries to prepare the feasibility study are substantial.
The department for Business Energy and Industrial Strategy is expected to launch the first phase of the ‘Industrial Heat Support Programme’ later this year, offering up to 40% funding support for these feasibility studies.
The second phase of the IHSP in 2018 could fund up to 30% of the capital costs of implementing the best projects identified from the feasibility studies.
(Originally posted here)