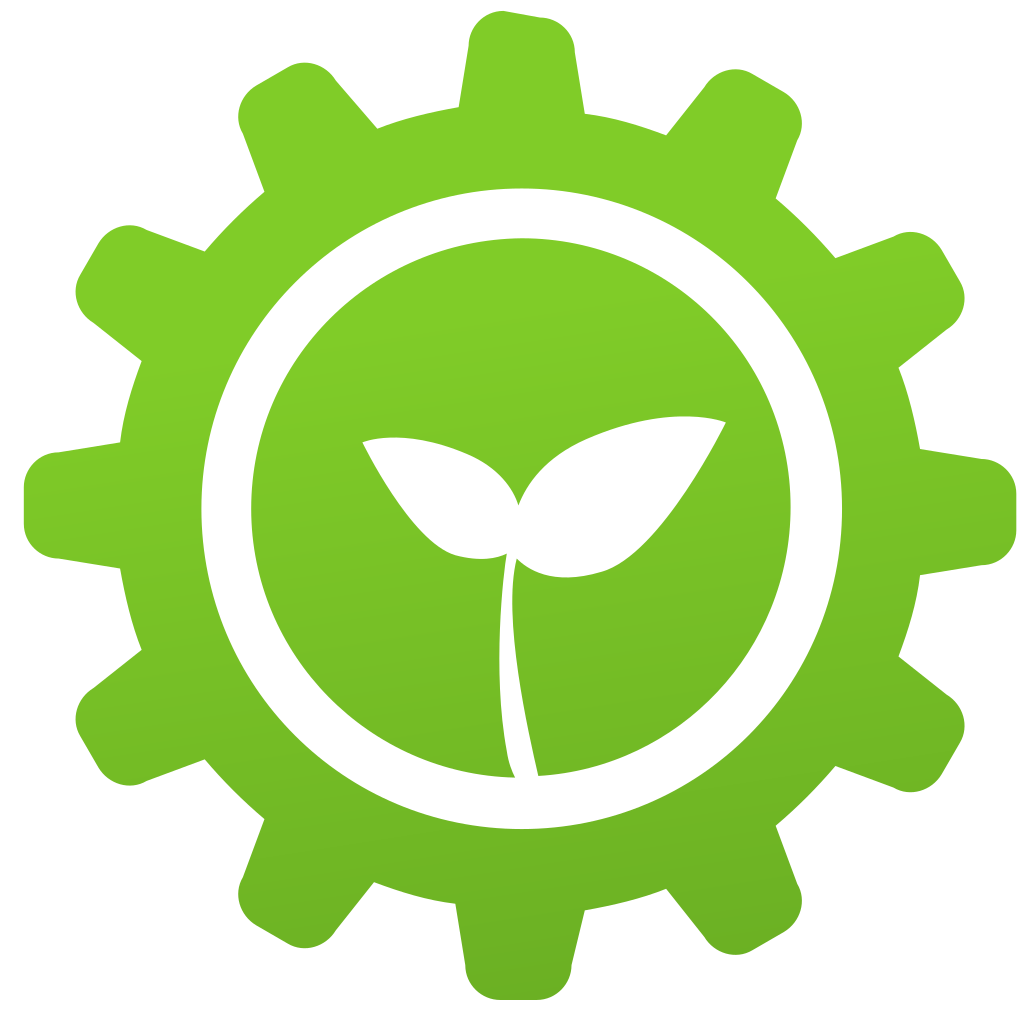
La pneumatique intelligente : 3 grandes étapes vers une production durable.
Résumé
Les systèmes pneumatiques se distinguent par le fait qu'il s'agit d'une technologie fiable largement utilisée et dont le coût d'investissement est faible. La grande durabilité des systèmes d'air comprimé cache souvent des fuites et des pertes de charge croissantes, qui peuvent être évitées grâce à une maintenance prédictive. La mise en œuvre de technologies intelligentes conformément à l'industrie 4.0 n'est pas seulement une étape tendance vers la numérisation, mais une mesure nécessaire. Pour la plupart des fabricants, le coût d'un capteur supplémentaire sur un système pneumatique peut augmenter le coût total de la machine, mais quels sont les avantages qu'il procure en retour ?
Ouvrir l'article complet
La pneumatique intelligente : 3 grandes étapes vers une production durable.
L'industrie 4.0, la maintenance conditionnelle et la maintenance prédictive sont les tendances actuelles dans le secteur industriel. Lorsque je vous interroge à leur sujet, qu'est-ce que vous imaginez ? La réponse à cette question se situe probablement entre les systèmes cyber-physiques et la réalité augmentée qui combine le monde réel de la production avec le monde virtuel des technologies de l'information et de la communication.
Et si je pose la question de l'industrie 4.0 en application aux systèmes pneumatiques ? La réponse mettra probablement en doute l'utilisation de technologies et de capteurs avancés pour des composants aussi simples et peu coûteux.
Pour la plupart des fabricants, le coût d'un capteur supplémentaire sur un système pneumatique peut augmenter considérablement le coût total de la machine. Mais quels sont les avantages qu'il procure en retour ?
Les systèmes pneumatiques se distinguent par le fait qu'il s'agit d'une technologie fiable, largement utilisée et dont le coût d'investissement est faible.
La grande durabilité des systèmes d'air comprimé dissimule souvent des fuites et des pertes de pression croissantes, ce qui permet d'éviter une éventuelle maintenance prédictive. Cela entraîne non seulement une augmentation de la facture énergétique et de l'impact sur le climat, mais influe directement sur les conditions de travail et de sécurité (la note assure des applications à haute pression et le niveau de bruit). En somme, la mise en œuvre de technologies intelligentes conformément à l'industrie 4.0 n'est pas seulement une étape tendance vers la numérisation, mais une mesure nécessaire. Les entreprises qui ont mis en œuvre les technologies de l'industrie 4.0 obtiennent les résultats suivants dans les aspects valeur-risque-coûts :
Augmentation de la valeur :
- Environnement de travail plus sûr et de meilleure qualité.
- Capacité de production plus élevée
- Gamme de produits à faible teneur en carbone
- Amélioration de la qualité et de la cohérence des produits.
Réduction des coûts :
- Réduction des coûts énergétiques
- Réduction des coûts de maintenance
- Réduction des coûts d'assurance accident
Réduction des risques :
- Réduction des risques de blessures pendant le fonctionnement des machines
- Réduction du risque de non-respect de l'ordonnance sur le bruit
- Réduction du risque climatique
- Réduction du risque de non-conformité aux réglementations/normes (directives sur le bruit)
Comment entamer une transition numérique en douceur avec le délai d'amortissement le plus court des mesures mises en œuvre ?
Pour commencer la mise en œuvre de la pneumatique intelligente, 3 étapes principales sont nécessaires :
Lapremière étapeest un système cyber-physique représentant des capteurs embarqués et des protocoles de communication simples envoyant des signaux sur des voyants lumineux. Ces types d'alarmes sont généralement mis en œuvre au niveau des composants ou des systèmes à un seul axe. Il est important de rappeler qu'un avertissement visuel est fondamental pour le dépannage. Même si le signal d'erreur est envoyé par logiciel à des systèmes de gestion de niveau supérieur, la possibilité pour les ingénieurs de maintenance de voir immédiatement ce qui se passe, et où, permet de gagner un temps considérable.
Figure 1 : Une architecture du concept de pneumatique intelligente
Ladeuxième étapeconsiste à simuler, modéliser et virtualiser les systèmes d'air comprimé et les paramètres physiques. Ce niveau de diagnostic comprend également un ensemble d'algorithmes qui permettent au logiciel de vérifier le fonctionnement d'un système.
N'oublions pas que l'analyse du fonctionnement des composants pneumatiques peut normalement être effectuée à l'aide d'interrupteurs de fin de course et de capteurs de pression.
Les informations sur la distance parcourue et les variations de vitesse peuvent, par exemple, être dues à une augmentation de la friction, à des fuites ou à des modifications des charges appliquées.
Une baisse inattendue de la vitesse peut entraîner une chute de la productivité, tandis qu'une augmentation brutale peut provoquer la rupture d'actionneurs ou de pièces mécaniques de la machine.
Ces informations peuvent être utilisées pour la maintenance prédictive du système, par exemple pour commander des pièces de rechange, mieux planifier le temps de maintenance afin de réduire les temps d'arrêt de la machine. Ces informations peuvent être lues par n'importe quel appareil distant, comme un smartphone, en lisant simplement le code QR du système en question.
La deuxième étape peut être mise en œuvre au niveau de la machine, ainsi que pour une usine entière permettant la surveillance des systèmes d'air comprimé.
Le système d'alarme intégré et les rapports destinés au responsable de la maintenance fournissent des informations complètes sur les principaux indicateurs clés de performance du système et garantissent une maintenance sans stress.
Figure 2 : Exemple de jumeau numérique d'un système pneumatique.
La troisième étapede la surveillance implique la collecte de grandes quantités de données, ainsi que leur analyse et leur exploitation, soit immédiatement sur le site de l'usine, soit par le biais de l'analyse des données massives et du cloud computing. Elle peut être réalisée en envoyant des données à distance à un système de gestion centralisé, ou via le cloud à l'aide d'une passerelle, à des opérateurs qui peuvent voir ce qui se passe à tout moment et fournir une assistance à distance.
Les communications en réseau, notamment les technologies sans fil et Internet, qui servent à relier les machines, les produits, les systèmes et les personnes, tant au sein de l'usine de fabrication qu'avec les fournisseurs et les distributeurs, ouvrent un nouvel horizon pour de nouveaux modèles d'entreprise vers un avenir durable.