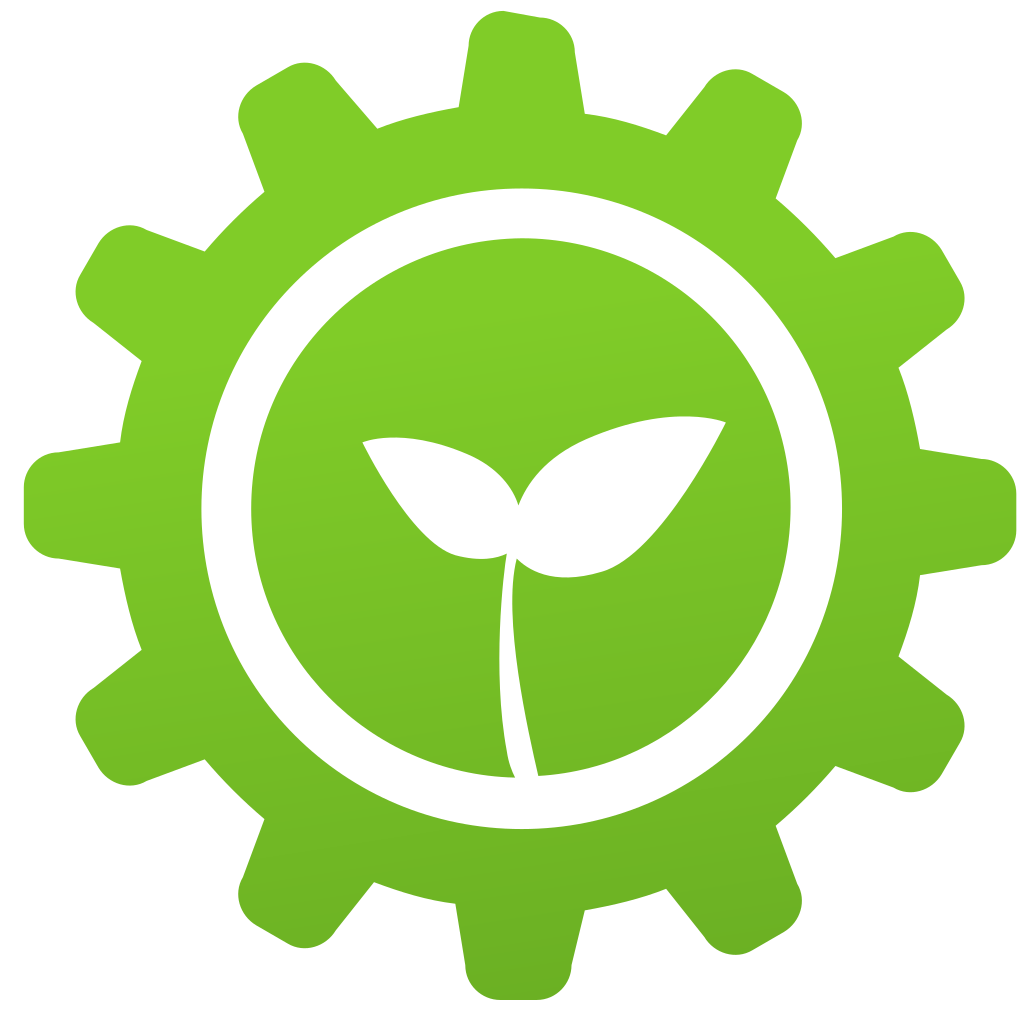
Smart pneumatics: 3 main steps towards sustainable production.
Summary
Pneumatic systems stand out for being a widely used reliable technology with low investment cost. High durability of compressed air systems often hides increasing leakages and pressure drop which can be avoided through predictive maintenance. The implementation of smart technologies in compliance with Industry 4.0 is not only a trendy step towards digitalization but a necessary measure. For most manufacturers, the cost of an additional sensor on a pneumatic system may increase the total cost of the machine, but what are the benefits it provides in return?
Open full article
Smart pneumatics: 3 main steps towards sustainable production.
Industry 4.0, condition monitoring, and predictive maintenance is the trend in the industrial sector nowadays. When I ask you about them, what do you imagine? The answer to this question probably lies between cyber-physical systems and augmented reality that combines the real world of production with the virtual world of information and communication technology.
What if I ask about Industry 4.0 in application to pneumatic systems? The answer will probably doubt the use of advanced technologies and sensors to such simple and low-cost components.
For most manufacturers, the cost of an additional sensor on a pneumatic system may dramatically increase the total cost of the machine. But what are the benefits it provides in return?
Pneumatic systems stand out for being widely used reliable technology with low investment cost.
The high durability of compressed air systems often hides increasing leakages and pressure drop avoiding possible predictive maintenance. That leads not only to an increased energy bill and higher climate impact, but directly influences a working and safety condition (note insures from high-pressure applications and noise level). All in all, the implementation of smart technologies in compliance with Industry 4.0 is not only a trendy step towards digitalization but a necessary measure. Companies that implemented the Industry 4.0 technologies achieve following results in the value-risk-costs aspects:
Increased value:
- Safer and higher-quality work environment
- Higher production capacity
- Lower carbon product line
- Improved product quality and consistency.
Reduced costs:
- Reduced energy costs
- Reduced maintenance costs
- Lower accident insurance cost
Lower risks:
- Reduced injury risks during operation of machines
- Reduced risk of non-compliance with noise ordinance
- Reduced climate risk
- Reduced risk of regulatory/standards non-compliance (noise directives)
How do we begin a smooth digital transition with the shortest pay-back period of implemented measures?
To start implementation of smart pneumatics, 3 main steps are necessary:
The first step is a cyber-physical system representing embedded sensors and simple communication protocols sending signals on LED warning lights. These types of alarms are usually implemented on the level of components or single-axis systems. It is important to remember that a visual warning is fundamental in troubleshooting. Even if the error signal is sent via software to higher-level management systems, the ability of maintenance engineers to immediately see what is happening, and where, saves considerable time.
Figure 1: An architecture of smart pneumatics concept
The second step involves simulation, modeling, and virtualization of the compressed air systems and physical parameters. This level of diagnostics also includes a set of algorithms that enable the software to check the operation of a system.
We shouldn’t forget that analysis of the operation of pneumatic components, normally can be done with limit switch and pressure sensors.
The information about distance traveled and speed changes could, for example, be due to increased friction, leaks, or changes to applied loads.
An unexpected drop in speed can cause a fall in productivity, whereas an abrupt increase can cause the breakage of actuators or mechanical machine parts.
This information can be used for predictive maintenance of the system, for example, to order spare parts, better planning of maintenance time to reduce downtime of the machine. This information can be read by any remote device, such as a smartphone, by simply reading the QR code for the system in question.
The second step can be implemented on the machine level, as well as for an entire plant enabling the monitoring of compressed air systems.
Integrated alarm system and reports for maintenance manager gives comprehensive information about system main KPI’s and ensures stress-free maintenance.
Figure 2: Example of a digital twin of the pneumatic system.
The third step of monitoring involves the collection of vast quantities of data, and their analysis and exploitation, either immediately on the factory floor, or through big data analysis and cloud computing. It can be realized by sending data remotely to a centralized management system, or via the cloud using a gateway, to operators who can see what is happening at any time and provide remote support.
Network communications including wireless and internet technologies that serve to link machines, work products, systems, and people, both within the manufacturing plant and with suppliers, and distributors open a new horizon for new business models towards a sustainable future.