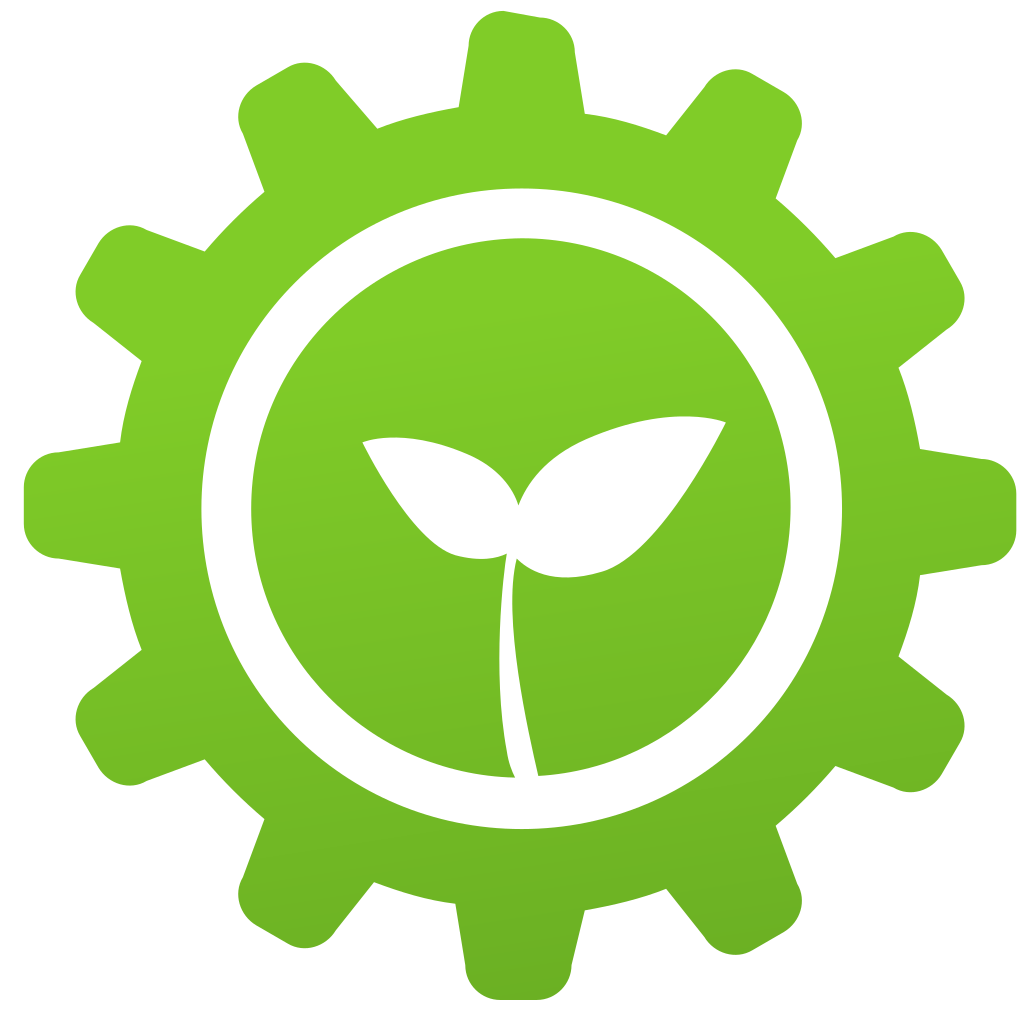
Práticas Comerciais
Powering Efficiency: Revolutionising Compressed Air Systems for a Sustainable Future
Resumo
Compressed air systems (CAS) are critical in manufacturing but are energy-intensive, accounting for 10% of industrial electricity. They offer potential energy savings of 20-60%, which translates to significant cost reductions and environmental benefits. Despite its convenience, most CAS are inefficient, with only 10-30% of the air produced being effectively used. The rest is lost through leaks, inappropriate usage, and other inefficiencies.
CAS consists of a supply side (compressors, storage tanks, dryers, filters) and a demand side (flow and pressure controls, distribution network). Optimizing each component can lead to substantial energy savings. Leaks are a major issue, often wasting 20-40% of air production, but can be mitigated through ultrasonic detection or soap-and-water tests. Proper storage tank sizing is also important, with a recommended capacity of 12-120 m³/m³/sec of air delivered, to avoid inefficiencies.
Additionally, the suction temperature affects energy consumption, with every 3°C increase leading to a 1% increase in energy use. Therefore, the location of compressors can have a considerable impact on efficiency. Improvements in CAS not only lead to energy savings but also increase production reliability, reduce maintenance costs, enhance product quality, and decrease the carbon footprint.
A systematic approach to CAS efficiency involves conducting air audits, fixing leaks, optimizing system pressure, sizing components correctly, implementing heat recovery, and regular maintenance. The highlighted case study in Barranquilla, Colombia, exhibited the tangible benefits of such measures, with potential energy consumption savings of 43.1% and annual cost savings of over 25 million Colombian pesos. Overall, optimizing CAS is a key way that industries can achieve sustainability and improve cost-effectiveness.
Artigo aberto completo
Powering Efficiency: Revolutionising Compressed Air Systems for a Sustainable Future
In the quest for sustainable industrial practices, compressed air systems (CAS) have emerged as a prime target for energy efficiency improvements. These systems, vital to many manufacturing processes, often consume 10% of industrial electricity worldwide. However, with the right approach, companies can slash their energy usage by 20-60%, unlocking substantial cost savings and environmental benefits.
The Hidden Energy Consumer in Your Factory
Compressed air, often dubbed the "fourth utility" after electricity, natural gas, and water, is a ubiquitous power source in manufacturing. Its popularity stems from its versatility, cleanliness, and safety. But this convenience comes at a cost – compressed air is one of the most expensive forms of energy in a plant due to significant inefficiencies.
Most industrial facilities use only 10-30% of the compressed air they produce effectively. The rest is lost through leaks, pressure drops, heat, and misuse. This inefficiency translates to wasted energy and unnecessary expenses, making CAS a prime candidate for energy-saving initiatives.
Anatomy of a Compressed Air System
To understand how to optimize these systems, it's crucial to know their components. A typical CAS consists of two main sides:
- Supply Side: This includes the compressor (which increases air pressure), storage tanks (both humid and dry), dryers, and filters.
- Demand Side: This encompasses the flow and pressure controls, along with the distribution network that delivers air to various machines and tools.
Each component plays a vital role in the system's efficiency, and optimizing each can lead to significant energy savings.
Plugging the Leaks: The Low-Hanging Fruit of Energy Savings
Leaks are the arch-nemesis of an efficient CAS. In a well-maintained system, leaks should account for no more than 5-10% of compressed air production. However, in many industrial settings, leaks can waste 20-40% of produced air, and in extreme cases, up to 60%.
Common leak points include joints, connections, and elbows in the compressed air pipelines. Identifying and fixing these leaks can lead to immediate and substantial energy savings. Companies can use techniques such as ultrasonic leak detection or simple soap-and-water tests to locate leaks.
In one case study, a glass manufacturing plant in Barranquilla, Colombia, found that leaks were responsible for 33% of their compressed air usage. By reducing this to an acceptable 5%, the company could save over 3,000 kWh per month – translating to annual savings of over 16 million Colombian pesos.
Size Matters: The Importance of Proper Storage
Storage tanks play a crucial role in CAS efficiency. They provide capacity to avoid short start/stop cycles, condense air humidity, cover pressure peaks, maintain system pressure, and allow for more efficient system control.
Experts recommend a storage capacity of 12-120 m³ for each cubic meter per second of air delivered by the compressor at full load. However, many systems are undersized, leading to inefficiencies.
In our case study, the glass manufacturer's storage tank was significantly undersized. By increasing their storage capacity to meet manufacturer recommendations, they could potentially save 12% on their compressed air energy consumption – equating to over 7 million Colombian pesos annually.
Keeping Your Cool: The Impact of Suction Temperature
The temperature of the air entering the compressor has a significant impact on efficiency. For every 3°C increase in inlet air temperature, energy consumption increases by 1%. Many compressors are located in hot areas of the plant, sucking in warm air and reducing efficiency.
In our case study, the compressor was poorly located on a second floor above an oven and next to a hot electric motor. The average suction temperature was 10°C above ambient, with peaks of 15°C difference. By relocating the compressor to draw in cooler air, the company could save 3.1% on their compressed air energy consumption – about 1.8 million Colombian pesos per year.
Beyond Energy: The Ripple Effects of Efficiency
While the energy savings from optimizing CAS are significant, the benefits extend far beyond lower electricity bills. Improved efficiency can lead to:
- Increased Production: A more reliable and efficient compressed air supply can boost productivity and reduce downtime.
- Lower Maintenance Costs: Well-maintained systems with fewer leaks and more appropriate sizing require less frequent repairs and replacements.
- Improved Product Quality: Consistent air pressure and quality can enhance manufacturing processes, leading to better end products.
- Reduced Carbon Footprint: Lower energy consumption translates directly to reduced CO2 emissions, helping companies meet sustainability goals.
The Road to Efficiency: A Step-by-Step Approach
Improving CAS efficiency doesn't have to be daunting. Companies can follow these steps:
- Conduct an Air Audit: Understand your current system, including leak rates, pressure requirements, and usage patterns.
- Fix Leaks: This is often the quickest and most cost-effective improvement.
- Optimize System Pressure: Many systems run at higher pressures than necessary. Reducing pressure can lead to significant energy savings.
- Right-Size Components: Ensure compressors, storage tanks, and distribution networks are appropriately sized for your needs.
- Implement Heat Recovery: Compressors generate a lot of heat. This can be captured and used for space heating or other processes.
- Regular Maintenance: Consistent upkeep ensures your system continues to operate at peak efficiency.
Compressed air systems represent a significant opportunity for energy savings in the industrial sector. By addressing issues like leaks, improper sizing, and suboptimal operating conditions, companies can dramatically reduce their energy consumption and operating costs.
The case study company in Barranquilla demonstrates the potential – by implementing just three efficiency measures, they could reduce their compressed air energy consumption by 43.1%, saving over 25 million Colombian pesos annually.
As industries worldwide strive for sustainability and cost-effectiveness, optimizing compressed air systems offers a clear path forward. It's time for companies to take a closer look at this often-overlooked utility and unlock the potential for significant energy savings and operational improvements.