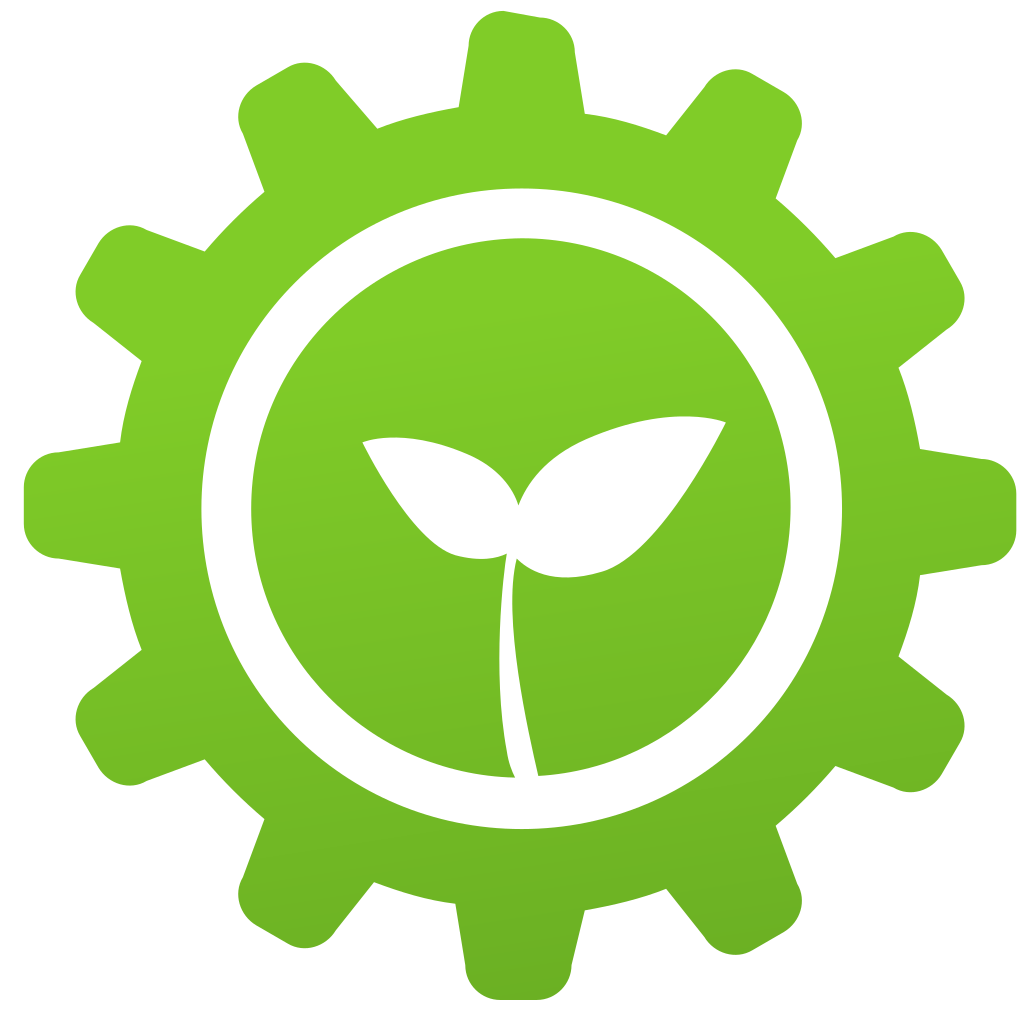
Casos Prácticos
Eficiencia energética: Revolucionando los sistemas de aire comprimido para un futuro sostenible
Resumen
Los sistemas de aire comprimido (CAS) son fundamentales en la fabricación, pero consumen mucha energía: representan el 10% de la electricidad industrial. Ofrecen un ahorro energético potencial del 20-60%, lo que se traduce en importantes reducciones de costes y beneficios medioambientales. A pesar de su comodidad, la mayoría de los CAS son ineficaces, ya que sólo se aprovecha eficazmente entre el 10 y el 30% del aire producido. El resto se pierde por fugas, uso inadecuado y otras ineficiencias.
Los CAS constan de un lado de suministro (compresores, tanques de almacenamiento, secadores, filtros) y un lado de demanda (controles de caudal y presión, red de distribución). Optimizar cada componente puede suponer un importante ahorro de energía. Las fugas son un problema importante, ya que suelen desperdiciar entre el 20% y el 40% de la producción de aire, pero pueden mitigarse mediante detección ultrasónica o pruebas con agua y jabón. También es importante dimensionar correctamente el depósito de almacenamiento, con una capacidad recomendada de 12-120 m³/m³/seg de aire suministrado, para evitar ineficiencias.
Además, la temperatura de aspiración afecta al consumo de energía, ya que cada aumento de 3 °C supone un incremento del 1% en el consumo de energía. Por tanto, la ubicación de los compresores puede influir considerablemente en la eficiencia. Las mejoras en el CAS no sólo permiten ahorrar energía, sino que también aumentan la fiabilidad de la producción, reducen los costes de mantenimiento, mejoran la calidad del producto y disminuyen la huella de carbono.
Un enfoque sistemático de la eficiencia del CAS implica realizar auditorías del aire, reparar fugas, optimizar la presión del sistema, dimensionar correctamente los componentes, aplicar la recuperación de calor y realizar un mantenimiento periódico. El estudio de caso destacado en Barranquilla (Colombia) mostró los beneficios tangibles de tales medidas, con un ahorro potencial de consumo de energía del 43,1% y un ahorro anual de costes de más de 25 millones de pesos colombianos. En general, la optimización del CAS es una forma clave de que las industrias logren la sostenibilidad y mejoren la rentabilidad.
Abrir artículo completo
Eficiencia energética: Revolucionando los sistemas de aire comprimido para un futuro sostenible
En la búsqueda de prácticas industriales sostenibles, los sistemas de aire comprimido (CAS) se han convertido en un objetivo prioritario para la mejora de la eficiencia energética. Estos sistemas, vitales para muchos procesos de fabricación, suelen consumir el 10% de la electricidad industrial en todo el mundo. Sin embargo, con el enfoque adecuado, las empresas pueden reducir su consumo de energía entre un 20% y un 60%, lo que supone un importante ahorro de costes y beneficios medioambientales.
El consumidor de energía oculto en su fábrica
El aire comprimido, a menudo denominado la "cuarta utilidad" después de la electricidad, el gas natural y el agua, es una fuente de energía omnipresente en la fabricación. Su popularidad se debe a su versatilidad, limpieza y seguridad. Pero esta comodidad tiene un coste: el aire comprimido es una de las formas de energía más caras de una planta, debido a sus importantes ineficiencias.
La mayoría de las instalaciones industriales sólo utilizan eficazmente entre el 10% y el 30% del aire comprimido que producen. El resto se pierde por fugas, caídas de presión, calor y mal uso. Esta ineficacia se traduce en derroche de energía y gastos innecesarios, lo que convierte al CAS en un candidato ideal para las iniciativas de ahorro energético.
Anatomía de un sistema de aire comprimido
Para entender cómo optimizar estos sistemas, es crucial conocer sus componentes. Un CAS típico consta de dos lados principales:
- Lado de suministro: Incluye el compresor (que aumenta la presión del aire), los depósitos de almacenamiento (tanto húmedos como secos), los secadores y los filtros.
- Lado de la demanda: Comprende los controles de caudal y presión, junto con la red de distribución que lleva el aire a las distintas máquinas y herramientas.
Cada componente desempeña un papel vital en la eficiencia del sistema, y la optimización de cada uno de ellos puede suponer un importante ahorro de energía.
Tapar las fugas: La fruta madura del ahorro energético
Las fugas son la archienemiga de un CAS eficiente. En un sistema bien mantenido, las fugas no deberían representar más del 5-10% de la producción de aire comprimido. Sin embargo, en muchos entornos industriales, las fugas pueden desperdiciar entre el 20% y el 40% del aire producido y, en casos extremos, hasta el 60%.
Los puntos de fuga más comunes son las juntas, conexiones y codos de las tuberías de aire comprimido. Identificar y reparar estas fugas puede suponer un ahorro energético inmediato y sustancial. Las empresas pueden utilizar técnicas como la detección de fugas por ultrasonidos o simples pruebas con agua y jabón para localizarlas.
En un estudio de caso, una fábrica de vidrio de Barranquilla (Colombia) descubrió que las fugas eran responsables del 33% de su consumo de aire comprimido. Reduciendo este porcentaje a un 5% aceptable, la empresa pudo ahorrar más de 3.000 kWh al mes, lo que se traduce en un ahorro anual de más de 16 millones de pesos colombianos.
El tamaño importa: La importancia de un almacenamiento adecuado
Los tanques de almacenamiento desempeñan un papel crucial en la eficiencia del CAS. Proporcionan capacidad para evitar ciclos cortos de arranque y parada, condensar la humedad del aire, cubrir los picos de presión, mantener la presión del sistema y permitir un control más eficiente del mismo.
Los expertos recomiendan una capacidad de almacenamiento de 12-120 m³ por cada metro cúbico por segundo de aire suministrado por el compresor a plena carga. Sin embargo, muchos sistemas están infradimensionados, lo que provoca ineficiencias.
En nuestro estudio de caso, el depósito de almacenamiento del fabricante de vidrio era muy pequeño. Aumentando su capacidad de almacenamiento para cumplir las recomendaciones del fabricante, podrían ahorrar potencialmente un 12% en su consumo de energía de aire comprimido, lo que equivale a más de 7 millones de pesos colombianos al año.
Mantener la calma: El impacto de la temperatura de aspiración
La temperatura del aire que entra en el compresor tiene un impacto significativo en la eficiencia. Por cada 3 °C de aumento de la temperatura del aire de entrada, el consumo de energía aumenta un 1%. Muchos compresores están situados en zonas calientes de la planta, por lo que aspiran aire caliente y reducen la eficiencia.
En nuestro estudio de caso, el compresor estaba mal situado en un segundo piso, encima de un horno y junto a un motor eléctrico caliente. La temperatura media de aspiración era 10 °C superior a la ambiente, con picos de 15 °C de diferencia. Reubicando el compresor para que aspirara aire más frío, la empresa pudo ahorrar un 3,1% en su consumo de energía de aire comprimido, unos 1,8 millones de pesos colombianos al año.
Más allá de la energía: El efecto dominó de la eficiencia
Aunque el ahorro de energía derivado de la optimización del CAS es significativo, los beneficios van mucho más allá de la reducción de las facturas de electricidad. La mejora de la eficiencia puede dar lugar a
- Aumento de la producción: Un suministro de aire comprimido más fiable y eficiente puede aumentar la productividad y reducir los tiempos de inactividad.
- Menores costes de mantenimiento: Los sistemas bien mantenidos, con menos fugas y un dimensionamiento más adecuado, requieren reparaciones y sustituciones menos frecuentes.
- Mejora de la calidad del producto: Una presión y calidad de aire constantes pueden mejorar los procesos de fabricación, lo que se traduce en mejores productos finales.
- Reducción de la huella de carbono: Un menor consumo de energía se traduce directamente en una reducción de las emisiones de CO2, lo que ayuda a las empresas a cumplir sus objetivos de sostenibilidad.
El camino hacia la eficiencia: Un enfoque paso a paso
La mejora de la eficiencia de CAS no tiene por qué ser desalentadora. Las empresas pueden seguir estos pasos:
- Realice una auditoría del aire: Comprenda su sistema actual, incluidos los índices de fugas, los requisitos de presión y los patrones de uso.
- Repare las fugas: Suele ser la mejora más rápida y rentable.
- Optimizar la presión del sistema: Muchos sistemas funcionan a presiones más altas de lo necesario. Reducir la presión puede suponer un importante ahorro de energía.
- Dimensionar correctamente los componentes: Asegúrese de que los compresores, tanques de almacenamiento y redes de distribución tienen el tamaño adecuado para sus necesidades.
- Implemente la recuperación de calor: Los compresores generan mucho calor. Puede capturarse y utilizarse para calentar el espacio o para otros procesos.
- Mantenimiento regular: Un mantenimiento constante garantiza que su sistema siga funcionando con la máxima eficiencia.
Los sistemas de aire comprimido representan una importante oportunidad de ahorro energético en el sector industrial. Si se solucionan problemas como fugas, dimensionamiento inadecuado y condiciones de funcionamiento no óptimas, las empresas pueden reducir drásticamente su consumo de energía y sus costes de funcionamiento.
El caso de estudio de la empresa de Barranquilla demuestra el potencial: aplicando sólo tres medidas de eficiencia, podrían reducir su consumo de energía de aire comprimido en un 43,1%, ahorrando más de 25 millones de pesos colombianos al año.
A medida que las industrias de todo el mundo luchan por la sostenibilidad y la rentabilidad, la optimización de los sistemas de aire comprimido ofrece un claro camino a seguir. Ha llegado el momento de que las empresas examinen más de cerca esta utilidad, a menudo ignorada, y descubran el potencial de ahorro energético y de mejora operativa que encierra.