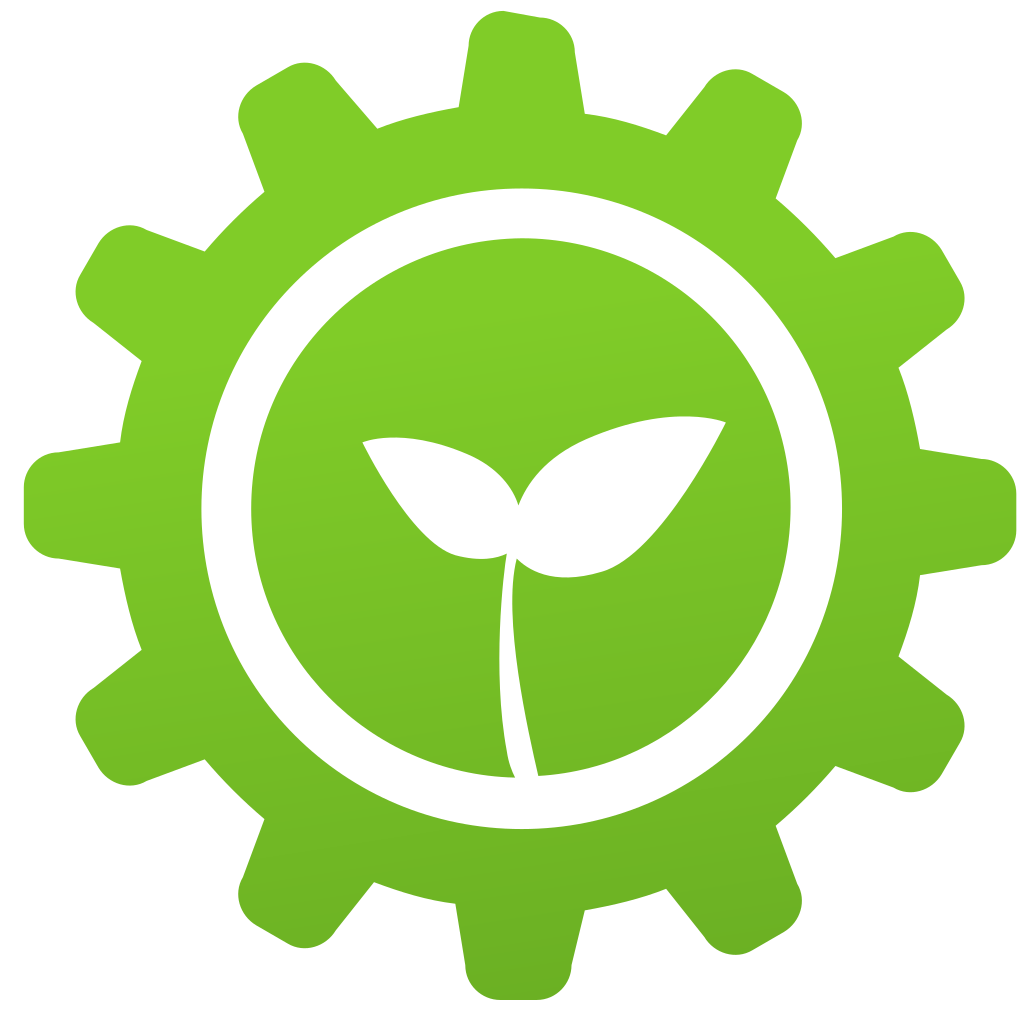
45% TCO – industrial pumps fight for efficiency
Summary
Energy costs represent up to 45 percent of Total Cost of Ownership for industrial pumps. The main lever for companies to get a good return from their pump investment is to maximise the efficiency of an installed pump in any way. This means to minimize the energy consumption as well as maximise availability of the pump - or in other words "energy efficiency" and "maintenance"
This post will give a little overview of what is meant by the two building blocks 'energy efficiency' and'maintenance'
This will then be discussed in more depth in 2 following posts. And I want to conclude this series with
this series with new opportunities arising from industry4.0 or IoT developments. These developments include developments in industry 4.0 and IoT developments, such as I expect to develop new opportunities. I expect this article to be published in the next phase of this article will be published next month. Back to MailOnline.com/IoTOI developments.
Open full article
45% TCO – industrial pumps fight for efficiency
Why Fighting?
Because energy costs represent up to 45 percent of Total Cost of Ownership for industrial pumps!
[Source: World Pumps Journal]
That said, the main lever for companies to get a good return from their pump investment is to maximise the efficiency of an installed pump in any way. And this means to minimize the energy consumption as well as to maximise the availability of the pump – or in other words "energy efficiency" and "maintenance".
As this turns out to be a complex subject with the risk of ending up with a 256 pages paper, I am trying to give some insights using a "pumps post series".
This post will give a little overview of what is meant by the two building blocks "energy efficiency" and "maintenance". This will then be discussed in more depth in 2 following posts. Finally I want to conclude this series with new opportunities arising from industry4.0 or IoT developments.
According to many experts the best approach to deal with the energy efficiency improvement is to split the subject into 3 steps following the life time of a pump system.
Another approach is e.g. proposed by the American Society of Mechanical Engineers (ASME) who propose "14 energy efficiency improvement opportunities in pumping systems".
However, I will cluster it broadly into "energy efficiency"and "maintenance".
Energy Efficiency
Pumps selection
Which remains a delicate task to some extent because pumps should be energy efficient while reaching the objectives related to productivity. To do so physical constraints (fluid properties, temperature, pressure,...) should be taken into account
System requirements
Considering the entire pump system. It need to be efficient enough to fit well with peak demand, average demand or potential process changes. A good example of the benefits by adressing system requirements instead of looking at a pump in isolation is provided by this presentation from CP Pumps.
Initial pump design
Pumps are often initially oversized in order to fit peak loads or to leave an error margin for design purposes. In addition, designers sometimes tend to oversize pump for fear of being made responsible for any performance below the one initially estimated. Over sizing pumps is not bad in itself but when the pump is running under peaks load conditions while being in a normal load, there is not only unnecessary wear on components but also wasted energy . This results in operation and maintenance costs that could be avoided.
Increase of pump capacity
Sometimes to respond to a growing demand pumps with higher capacity are required. Pumps initially oversized might be suitable in energy and cost efficient way. Hence there is interest to oversized pump when designing. If this is not the case any pump should be upgraded (to add a branch system) and even in some cases be completely replaced for energy savings purposes.
Maintenance
Although it may have shortcomings in the initial choice of pumps, pumps also have shortcomings which are mainly related to their operation. I mean problems such as cavitation, wear on mechanical components and so on ... that contribute to the degradation of the performance of pumps. Some of its problems are unavoidable and the only thing to do is to reduce their effect in order to be as close to the best efficiency point (BEP) as possible over the lifetime.
This degradation in some cases could be significant from 10 to 25 percent over the lifetime of pump and is not only due to the age of pumps system but also due to mismatch between the pump capacity and its operation and change in process. Keeping pumps in their maximum efficiency (BEP) is a kind of process for which the starting point is the pump selection combined with the way problems (related to the operation) and demand respond will be handled.
Stay tuned…