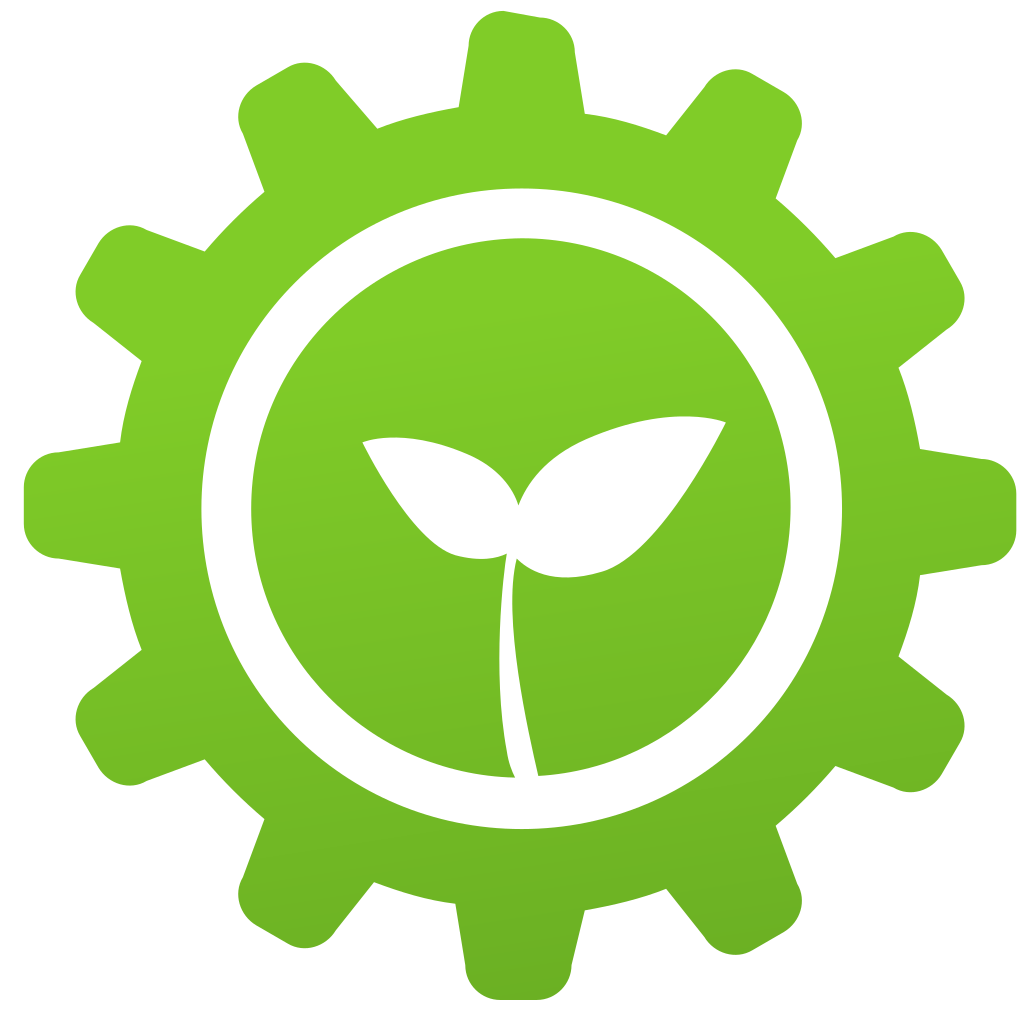
Digital Revolution in Motor Systems: Powering the Future of Energy Efficiency
Summary
The paper discusses the impact of digital technologies in enhancing the energy efficiency of industrial motor systems. It identifies key digital tools such as smart sensors, IoT, continuous monitoring, data analytics, digital twins, AI, and machine learning, which help optimize motor system operations and facilitate real-time performance tracking. Despite these advancements, the industry faces challenges like lack of standardization, skill shortages, resource limitations, low awareness of energy wastage, and cybersecurity risks. Innovations like smart pump monitoring, intelligent ventilation systems, and adaptive compressor control are highlighted, showcasing substantial energy savings. A case study of BMW's Steyr plant indicates a significant drop in energy consumption through data-driven management. The paper also points to opportunities for young professionals in areas such as data science, IoT, sensor technology, energy management systems, and cybersecurity within the industry. It emphasizes the necessity for rapid and effective implementation of digital transformations for future sustainability and efficiency in industrial motor systems.
Open full article
Digital Revolution in Motor Systems: Powering the Future of Energy Efficiency
In an era where energy efficiency is paramount, the digitalization of motor systems emerges as a game-changer in the industrial landscape. This transformation is not just about adopting new technologies; it's about reimagining how we approach energy consumption in one of the most power-hungry sectors of industry.
The Digital Toolkit: Transforming Motor Systems
At the heart of this revolution lies a suite of digital technologies that are redefining motor system operations:
- Smart Sensors and Intelligent Control: These technologies form the foundation of digital motor systems, providing real-time data on performance metrics.
- Internet of Things (IoT): Enabling seamless communication between different levels of the system, from individual machines to entire production lines.
- Continuous Monitoring: Offering insights into system performance, energy consumption, and potential issues before they escalate.
- Data Analytics: Transforming raw data into actionable insights for optimization and efficiency improvements.
- Digital Twins: Virtual replicas of physical systems that allow for simulation and predictive maintenance.
- Artificial Intelligence (AI) and Machine Learning: Enhancing decision-making processes and automating complex optimizations.
The Current Landscape: Challenges and Opportunities
The industrial sector stands at a crossroads. While the potential for energy savings through digitalization is immense, several challenges persist:
- Lack of Standardization: The absence of uniform protocols has historically hindered the integration of different machines and systems.
- Competence Gap: The multifaceted nature of digitalization demands a diverse skill set, often lacking in traditional industrial settings.
- Resource Constraints: Particularly for smaller industries, the allocation of time, money, and personnel for digital initiatives can be challenging.
- Awareness Issues: Many in the industry remain unaware of the significant energy consumption of systems like compressed air or ventilation, treating them as negligible costs.
- Cybersecurity Concerns: As systems become more interconnected, the risk of cyber threats increases, necessitating robust security measures.
Despite these challenges, companies are setting ambitious targets. From automated leak detection in compressed air systems to load management based on electricity pricing, the goals are as diverse as they are impactful.
Innovations Driving Change
Let's explore some of the groundbreaking innovations reshaping the landscape of motor systems:
Smart Pump Monitoring
A case study from the United Kingdom showcases how electric signature analysis is revolutionizing pump monitoring. By analyzing current and voltage patterns, this technology can detect issues like cavitation, bearing degradation, and efficiency losses, leading to energy savings of up to 15%.
Intelligent Ventilation Systems
In Switzerland, IoT sensors are being employed to detect clogged air filters in ventilation systems at server sites. This proactive approach not only ensures optimal air quality but also reduces energy consumption by up to 20% by preventing systems from operating with polluted filters.
Adaptive Compressor Control
A Swiss company implemented a central adaptive monitor control system for their compressed air network. This intelligent system optimizes compressor operation based on real-time demand, resulting in a 16% reduction in energy consumption per cubic meter of air produced.
Data-Driven Plant Management
BMW's plant in Steyr, Austria, exemplifies comprehensive data utilization. By monitoring everything from plant-wide energy supply to individual machine consumption, they've achieved a 25% reduction in base load energy consumption since 2016.
The Road Ahead: Opportunities for Young Innovators
The digitalization of motor systems opens up a world of opportunities for students and young professionals in the energy sector:
- Data Science in Energy: As industries generate vast amounts of data, there's a growing need for professionals who can interpret this data and drive energy-efficient decisions.
- IoT and Sensor Technology: The development and implementation of smart sensors offer a fertile ground for innovation and career growth.
- AI and Machine Learning in Industrial Applications: As these technologies become more integral to motor system optimization, expertise in AI and ML will be highly sought after.
- Energy Management Systems: Designing and implementing comprehensive energy management solutions will be crucial as industries strive to meet sustainability goals.
- Cybersecurity for Industrial Systems: With increased connectivity comes the need for robust security measures, creating opportunities in industrial cybersecurity.
The digitalization of motor systems is not just a technological shift; it's a pathway to a more sustainable and efficient industrial future. For young innovators, it presents an opportunity to be at the forefront of this green industrial revolution, driving change that will shape the energy landscape for decades to come.
As we stand on the brink of this digital transformation, the question is not whether to embrace these changes, but how quickly and effectively we can implement them. The future of energy efficiency in motor systems is digital, and it's a future that's being written right now by the innovators of today and tomorrow.
Source: https://youtu.be/-y0wteqY_tk