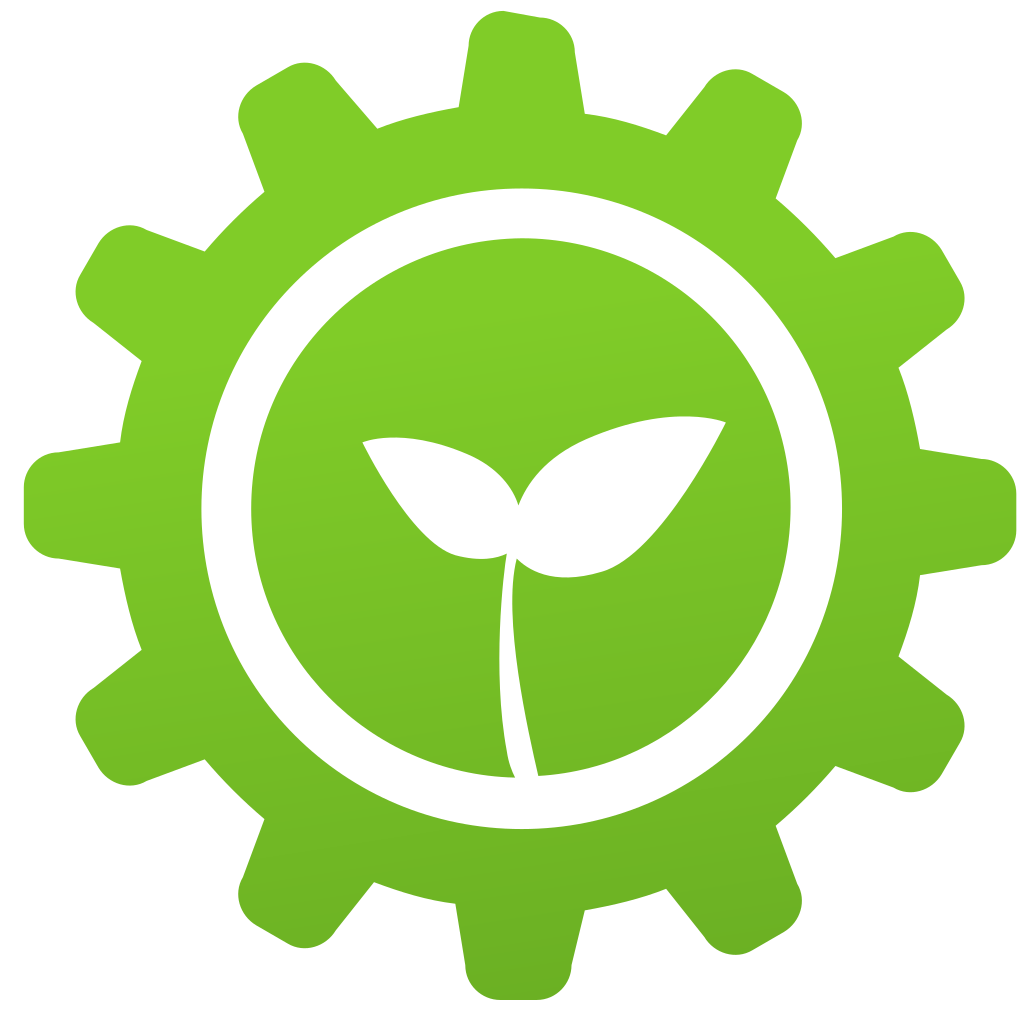
Key findings on digitalisation technologies to increase energy efficiency in electric motor driven systems
Summary
Worldwide, electric motor systems consume about 10,700 TWh annually worldwide and were responsible for 53% of the global electric energy consumption in 2016. This corresponds to approximately the combined electricity consumption of China.
Digitalization technologies for electric motor driven systems will have a significant impact on the motor systems industry, offering vast potential for improvements in performance, efficiency, and cost.
To enable industry to select the best solutions for their specific needs, a classification of digitalisation technologies is beneficial to map use cases and allow for camparison amongst them.
Open full article
Key findings on digitalisation technologies to increase energy efficiency in electric motor driven systems
Worldwide, electric motor systems consume about 10,700 TWh annually worldwide and were responsible for 53% of the global electric energy consumption in 2016. This corresponds to approximately the combined electricity consumption of China.
Digitalization technologies for electric motor driven systems will have a significant impact on the motor systems industry, offering vast potential for improvements in performance, efficiency, and cost. However, to determine which digital technology is meaningful for whom, let`s start with the electrical motors system itself.
In the IEA report "classification of digitalisation technologies for electric motor driven systems", the following definition is presented:
An optimal motor system includes optimal aligned system components (motor control, motor, mechanical equipment and application) engineered and operated for the right process demands in a specific timeframe. The application of digital technologies to electric motor driven systems can enlarge the scope and accessibility of optimisation, leading to efficiencies in operation (operational cost, flexibility, procurement, footprint), energy, materials (circularity) and emissions.
How to choose a digital technology to improve?
Choosing a certain digital technology solution requires to know the expected benefit for a specific company environment based on the status-quo. But this means you would need first to know how to separate - or classify - the different digitalisation technologies.
A broad classification
A broad classification could look like the following, using 5 categories:
Control Technologies: This includes technologies such as programmable logic controllers (PLCs), variable frequency drives (VFDs), and advanced control systems that are used to control the operation of electric motor driven systems. These technologies enable real-time monitoring and control of motor performance, improving efficiency and reducing energy waste.
Predictive Maintenance Technologies: These include technologies such as machine learning algorithms and data analytics tools that are used to predict potential failures in electric motor driven systems. Predictive maintenance technologies can help organizations to reduce downtime and improve efficiency by preventing failures from occurring.
IoT Technologies: This includes technologies such as sensors, cameras, and cloud-based platforms that enable remote monitoring and control of electric motor driven systems. IoT technologies can improve the reliability and performance of motor systems while reducing energy waste.
Big Data and Analytics Technologies: These include technologies such as data warehousing, data mining, and business intelligence tools that enable organizations to process and analyze large amounts of data generated by electric motor driven systems. Big data and analytics technologies can help organizations to make informed decisions about the performance and maintenance of their systems.
Simulation and Modeling Technologies: These include technologies such as computer-aided design (CAD) and finite element analysis (FEA) that enable organizations to simulate and model the performance of electric motor driven systems. Simulation and modeling technologies can help organizations to optimize performance and reduce energy waste.
More detailed classification
I personally like more the classification prepared under the IEA Technology Collaboration Programme on Energy Efficient End-Use Equipment (4E) – Electric Motor Systems Annex (EMSA) programme. It groups 13 digitalisation technologies into 4 boxes:
Communication between components
- Sensors
- Internet of Things
- Intelligent control
Data analysis & operation optimisation
- Data analytics (equipment level)
- Data analytics (production line / company)
- Real-time monitoring
Technologies adding further advantages
- Artificial Intelligence
- Digital twins
- Cloud-based services
- Augmented reality
Other relevant technologies
- Additive manufacturing
- Advanced robotics
- Drones
What´s next
To support the decision making in industry, the different applications need to be further investigated. Especially the identification of industrial use cases will be an important driver, giving answers to the following questions:
- What is the energy efficiency potential of each solution?
- What are the economics behind, assessing business model and financing routes?
- How easy or complex is the implementation?, e.g. technologies such as digital twins likely offer broader benefits so that increasing the energy efficiency of the motor system becomes a use case amongst many
Call to Action for you
If you know of any industrial use cases using digital technologies as described above, we would be very happy to publish them here to the 150.000 expert reach of EEIP. Please feel free to send them to me via juergen.ritzek@ee-ip.org