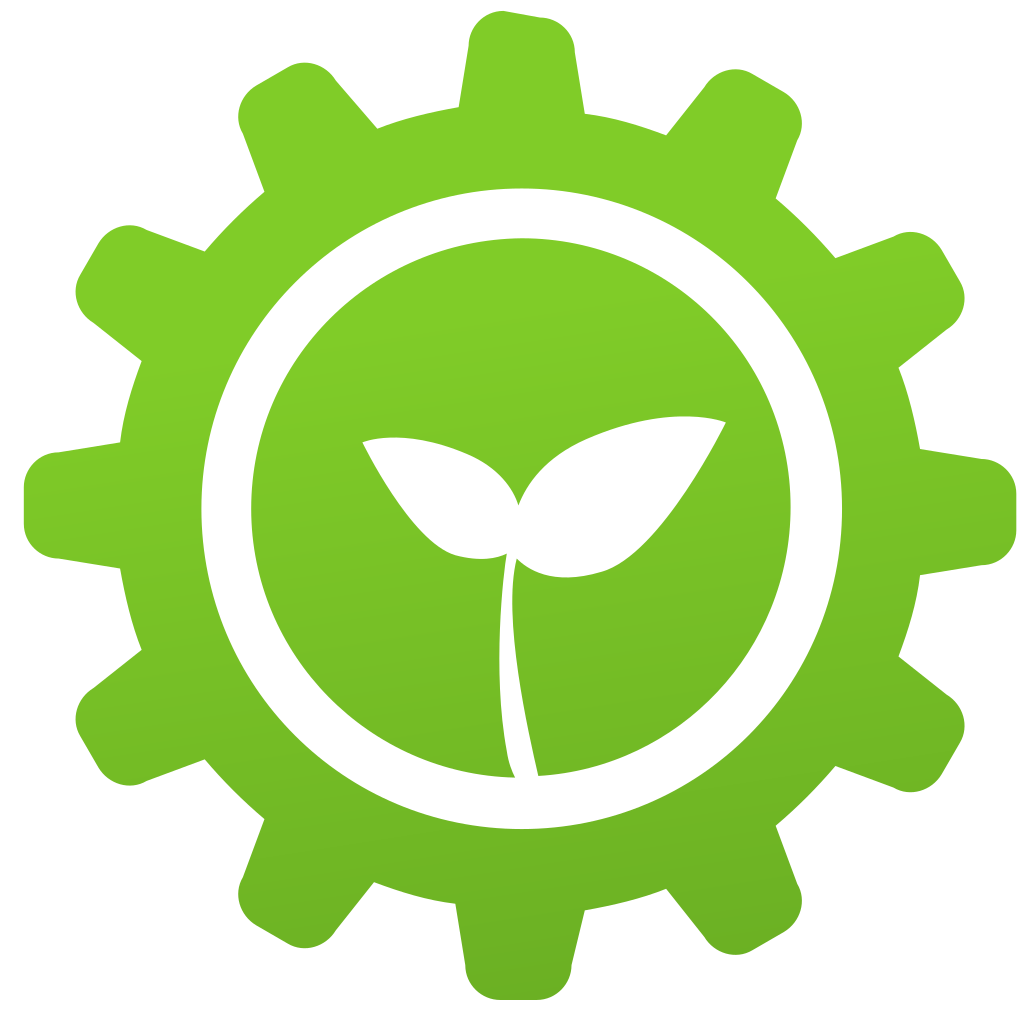
The benefit of compressed air systems becoming smart - a Boge example
Summary
The BOGE continuous improvement programme (CIP) is already a reality today. It reduces the loss of efficiency in a compressor due to wear and tear in operation. This can only be achieved through regular maintenance carried out by specialists. In a standardised process, there is always the question of whether the components used by the customer can be improved by developments that have already occurred. With the use of innovative data glasses, conversions can be carried out on-site by staff without special training or even by customers employees. The support comes from video instructions or relevant documents on a display built into the glasses. After successful commissioning of the now optimised compressed air station there is a detailed analysis of the actual energy savings for the customer, for: the installation of the software or hardware updates is free of charge for the user. Only the actual measured savings are shared by the user, for. the customer. only the service-free of charge.
Open full article
The benefit of compressed air systems becoming smart - a Boge example
The continuous improvement programme – a smart service – considerably improves the efficiency and life cycle of compressed air systems based on continuous Improvements.
The origin of the revolution
Up to now, manufacturers of compressors have reduced the loss of efficiency in a compressor due to wear and tear in operation simply by changing the lubricants and wearing parts. This can only be achieved through regular maintenance carried out by specialists. In the best scenario, the compressor does not deteriorate further. However, what if the compressor had no lubricants and wearing parts at all? If it were to remain consistently effective without maintenance? If we could make it even better? If we were able to introduce new technical developments and even respond to changes in customer requirements? This idea, which is revolutionary in the compressed air industry, is the BOGE continuous improvement programme (CIP) and is already a reality today.
But how can this revolution work? Let us take an example of a customer case to demonstrate this.
Step 1 – the smart product as a basis
With the BOGE HST product innovation, we have developed a turbo compressor that is streamlined for energy efficiency and to be environmentally friendly. The extremely wear-resistant compression process takes place completely free of oil and ensures top values in all areas. BOGE HST compressors (55-220 kW) stand out with their energy values of a marginal 1.9% when idling, for example, in relation to the overall power uptake. Material wear, and therefore the necessity for changing components, is virtually non-existent. Exchanging the old compressor technology for the BOGE HST, which has been honoured with the OWL innovation prize, is therefore the basis for implementing the CIP.
Step 2 – the digital twin of the customer situation
The revolution of industrial service thinking starts here: Due to the ongoing measurement and documentation of all information that is relevant for the running behaviour of the machine, we obtain a precise illustration of the customer situation.
![]() |
---|
What previously necessitated extensive diagnosis with special measuring instruments on-site, is now carried out continuously by the BOGE HST itself. With the help of its own software BOGE airstatus, all machine data required for energy efficiency are recorded and transmitted digitally. The BOGE performance report generated by this, documents the analysis of a variety of running data, such as the capacity of the machine, the energy consumption and motor temperatures. The customer has digital access at all times to the BOGE performance report for their own energy management.
Step 3 – revolution due to smart product, smart service and smart factory in harmony
Based on the BOGE performance report our specialists regularly analyse the operating behaviour of the compressed air station. In a standardised process, there is always the question of whether the components used by the customer can be improved by developments that have already occurred, or even the individual development of parts for the customer.
![]() |
---|
The main criteria here are the improvement of the system energetics and the extension of the modules relevant to the service life. To ensure the economical production of these individualised components alongside this application-related development of parts, new high-tech manufacturing was set up specially for the core components. This enabled the high-quality and efficient production of customer-specific components using assistance systems and intelligent production processes
Step 4: Implementation in practice – risk-free for the customer and simple to handle
The potential identified was implemented practically in consultation with the customer. The newly developed generation of compressor units was installed for the user. The BOGE HST has been designed with a view to maximum modularity and service-friendly handling. Changing a compressor unit is therefore designed to be quick and straightforward. Not only does it weigh 90% less than compression units on the market but it is also considerably smaller. The effort and duration involved in conversions is therefore drastically reduced. Local expert knowledge is also no longer required for this. With the use of innovative data glasses, conversions can be carried out on-site by staff without special training or even by the customer's employees.
![]() |
---|
BOGE smart glasses enable an expert to be connected here via video transmission, and they are able to give instructions remotely. Alternatively, the support comes from video instructions or relevant documents on a display built into the glasses.
Step 5: The customer can only gain
After successful commissioning of the now optimised compressed air station, there is a detailed analysis of the actual energy savings for the customer, for: the installation of the the software or hardware updates is free of charge for the user. Only the actual measured savings are shared by BOGE and the customer over a predefined period. The investment risk for the customer is therefore minimal. The steps outlined in measures 2 and 3 are resumed immediately for continuous optimisation, in accordance with the BOGE CIP customer guarantee: maximum efficient operation of the compressed air station across the entire life cycle.
![]() |
---|
Conclusion
With the BOGE continuous improvement programme BOGE is setting standards in the exploitation of potential for the hybridisation of market performance, and demonstrates impressively how the change from classic engineering company to customer-centred service provider can be a success. The combination of the highest level of engineering skill and intelligent data analysis smooths the way to the next level of customer focus. With its capacity for transfer to other industries, this smart service can be viewed as a milestone for increasing efficiency and energy saving beyond the compressed air industry too.
Related articles
- The 4th utility - compressed air
- Compressed air - Hannover Messe 2017 follow up
- Artificial Intelligence in Energy Management Software