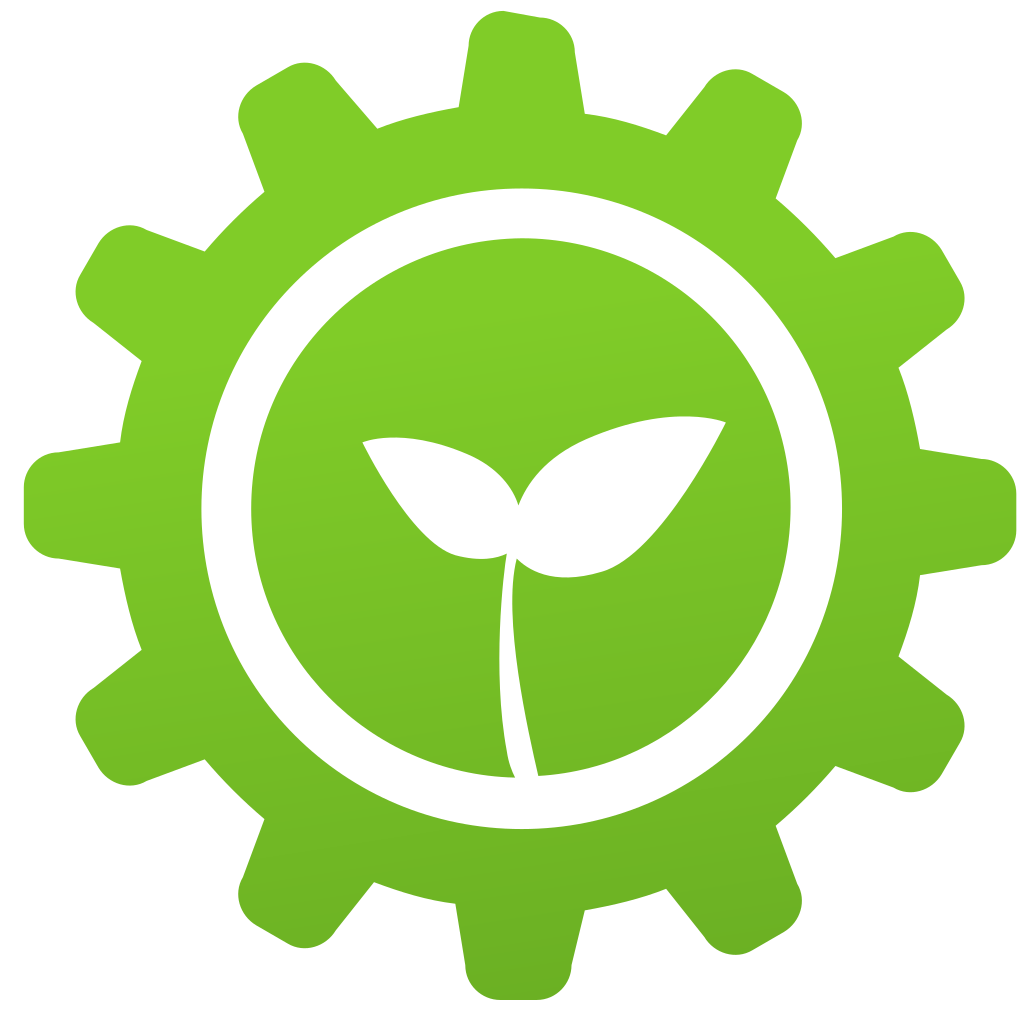
Utilize all the available energy — Heat recovery
Summary
Brazed Plate Heat Exchanger (BPHE) technology offers the most efficient recovery of heat. BPHEs are an integral tool that allow extra heat to be extracted from the refrigeration system. It enables users to transfer the waste heat to different parts of the production chain or to an exterior facility, utilizing almost all the energy produced. Other advantages of BPHEs include their compact size, increased efficiency and reliability. In many cases, the reduction in wasted energy combined with lowered utility costs optimizes the payback period, so that in many cases it can be as short as six months. BAPHE technology is virtually maintenance-free, with reduced lifecycle costs compared to other heat exchanger technologies while offering the most effective recovery. This can be short-term cost savings while also lowering CO emissions. Back to Mail Online home. For confidential support call the Samaritans in the UK on 08457 90% on 0844.
Open full article
Utilize all the available energy — Heat recovery
Today, global industry consumes a vast amount of energy. The biggest challenge is that as much as half of it is wasted due to the inefficient and complicated recovery of low-grade energy. Heat in the form of vapor, hot water, or hot air is a result of almost any production cycle, but it does not have to go to waste. With smarter systems, it can be recovered and reused for other purposes, contributing to the reduction of carbon emissions and to significant cost savings for both producers and end users.
Brazed Plate Heat Exchanger (BPHE) technology offers the most efficient recovery of heat across a range of industrial applications, including Process and Comfort cooling Chillers, Combined Heat and Power and compressed air systems.
Utilize the high-temperature energy of superheated refrigerant gas
Industrial refrigeration systems with air-cooled condensers waste energy by emitting condensation energy to the ambient air. By installing a desuperheater, much of this waste energy can be converted to hot water, with a wide range of applications.
Brazed Plate Heat Exchangers (BPHEs) are an integral tool that allow extra heat to be extracted from the refrigeration system. A BPHE, called a desuperheater, is inserted between the compressor and the condenser. This enables the BPHE to extract the heat from the gases or liquids before it goes into the condenser to be condensate (the liquid collected by condensation).
Installing a BPHE increases efficiency levels to help achieve the demanding recent EU Ecodesign Directive that cover high temperature process chillers. Evaporators can operate at a range of temperature levels to meet the required demands for a variety of refrigerants.
Using clean, processed water is essential to prolong the life of all industrial components and is necessary to achieve maximum performance from BPHEs.
![]() |
---|
BPHEs offer copper brazing as standard but also stainless and nickel as alternative brazing materials in order to meet the demands for various corrosive fluids.
Simultaneous production of electricity with the recovery and utilization of heat
Traditional cogeneration systems produce electric power at around 40% efficiency, so there is a lot of waste. A way to improve efficiency is to install cogeneration systems that produce electricity and heat simultaneously. Such plants are called CHP - Combined Heat and Power.
CHP plants are usually built around a gas engine genset. They collect thermal energy from an intercooler, engine jacket water, lubrication oil, and exhaust gas. Hot water can then be produced via heat exchangers, increasing total energy utilization efficiency, often to a level in excess of 90% efficiency.
![]() |
---|
Some CHP plants are connected through an ORC (Organic Rankine Cycle) system where the waste heat of the engine is used to drive the generator. CHP plants are typically embedded close to the end user and therefore help reduce transportation and distribution losses, improving the overall performance of the electricity transmission and distribution network.
Reclaim more energy from compressed air systems
Some 10% of all electricity used in industry derives from compressed air systems. And around 94% of this energy is converted to heat that is not wanted or needed. So with inefficient systems that do not have a heat recovery capability, energy is first used to generate heat and then more energy is consumed to remove the heat using cooling fans. And often there can be several processes producing waste heat within the same facility.
The heat recovery capability of a compressed air system is therefore vital. BPHE technology enables users to transfer the waste heat to different parts of the production chain or to an exterior facility, utilizing almost all the energy produced. Other advantages of BPHEs include their compact size, increased efficiency and reliability.
![]() |
---|
The reduction in wasted energy combined with lowered utility costs optimizes the payback period, so that in many instances it can be as short as six months. Businesses that choose to install a heat-recovery solution for their compressed air systems achieve significant cost savings while also lowering CO emissions.
Brazed Plate Heat Exchangers are virtually maintenance-free, with reduced lifecycle costs compared to other heat exchanger technologies while offering the most efficient recovery of heat across a range of industrial applications. In many cases, the reduction in wasted energy combined with lowered utility costs optimizes the payback period. This can be as short as six months.
Further information about the benefits of BPHE technology in heat recovery can be found here.
About SWEP
Starting from small beginnings in Sweden in 1983, SWEP is now the world's leading supplier of compact brazed plate heat exchangers (BPHEs). These are used where heat needs to be transferred efficiently in air conditioning, refrigeration, heating, and industrial applications.
At SWEP, we believe our future rests on giving more energy than we take - from our planet and our people. That's why we pour our energy into leading the conversion to sustainable energy usage in heat transfer. Over three decades, the SWEP brand has become synonymous with challenging efficiency.
www.swep.net
Stay tuned! Best ideas for energy efficiency and energy transition...