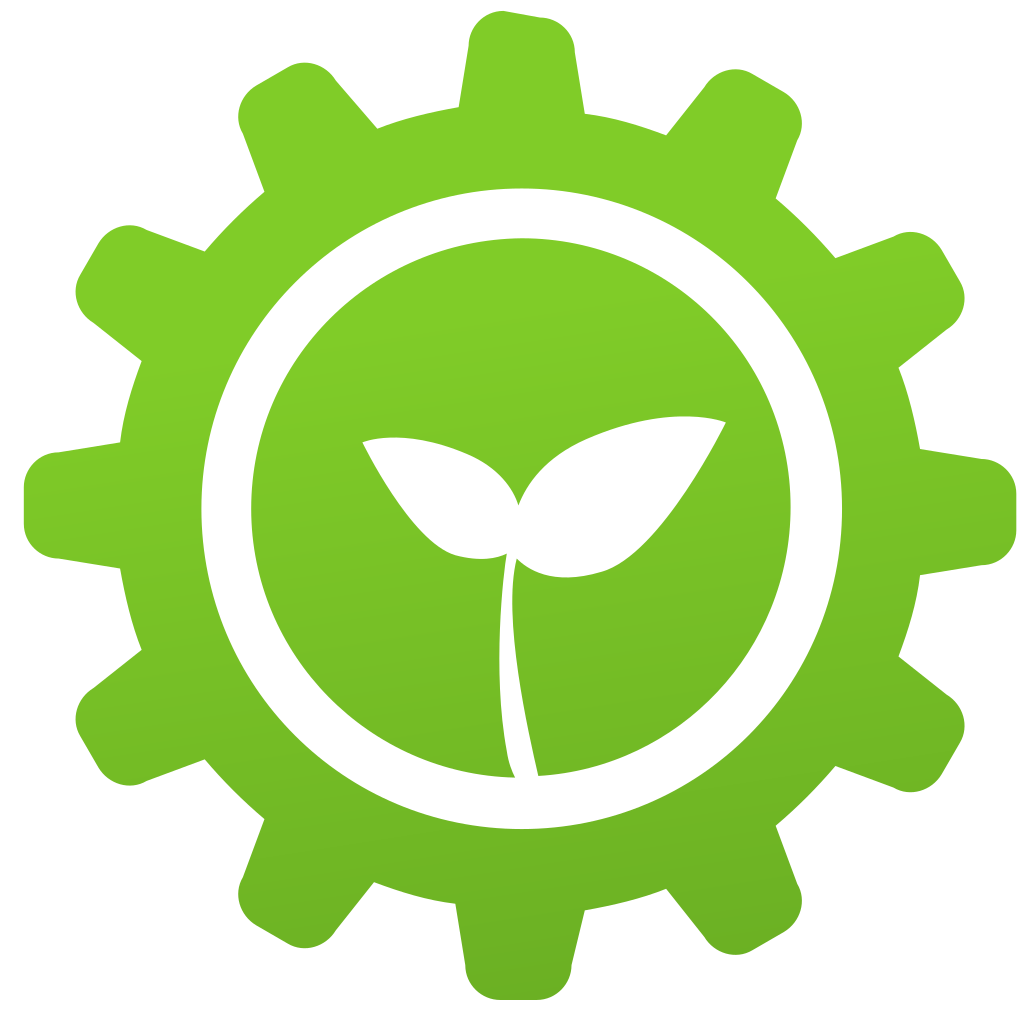
Business Practices
Optimizing Electrical Motor Efficiency: Get More Bang for Your Buck
Summary
Electrical motors are devices that convert electrical energy into mechanical force. They operate on the principles of electromagnetism, using the interaction between winding currents and magnetic fields. Some motors, like those used in the transportation industry can reverse the effect and generate electricity too, converting force into electricity. A slight increase in efficiency can dramatically cut energy spending and improve profits too. There are a number of ways you can increase the life period of motors in your facility, and thus their operational efficiency too: Lamination - Instead of cheaper carbon steels, lamination containing steels that have a little silicon can be used. Using thinner lamination and increasing their length reduces the length reduces core losses by limiting the effects of saturation and hysteresisisis. Lubrication - The lubrication interval is decided by a combination of various factors, so you should use to improve your facility's lubrication and prolong the life periods and prolonging the motor's life period.
Open full article
Optimizing Electrical Motor Efficiency: Get More Bang for Your Buck
First published here.
Electrical motors are devices that convert electrical energy into mechanical force. They operate on the principles of electromagnetism, using the interaction between winding currents and magnetic fields to generate force. Some motors, like those used in the transportation industry can reverse the effect and generate electricity too, converting force into electricity.
Many industrial plants attribute over 70% of their power consumption to motors, so even a slight increase in efficiency can dramatically cut energy spending and improve profits too.
How to Increase Motor Efficiency
There are a number of areas where losses in motor efficiency can occur. They range from frictional and heat losses to dissipation of the magnetic field within the core of the motor. Even the type of materials used can affect a motor's overall efficiency.
![]() |
---|
Improving the efficiency of motors can be segregated into 3 phases:
Phase 1 - Assessment
The first step is to monitor and document each motor, and assess the current performance level. Gather and record details which are essential for assessing the motor's current efficiency or consumption, like:
- The age of the motor
- How much horsepower the motor is actually generating
- Power and consumption ratings
- What kind of control levels have been implemented in your facility
- Identify the various loads that the motor is subjected to by using a power logger
Once you have all the information, you can use an efficiency calculator system, like motor master, to calculate the efficiency of the motor.
Phase 2 - Improvement
Right away, you can use the information you've gathered during phase 1 to make some immediate improvements. Older motors are inherently inefficient, so they can be replaced with modern higher-efficiency ones. If there are any that are over or under-sized, replace them with better sized models to improve running efficiency.
To optimize the motors you intend on keeping, inspect them for three variables that are known to reduce efficiency and even the life of the motor significantly:
- Voltage Unbalance In a three-phase motor, voltage unbalance is the difference in voltages across the phases. For optimum performance and efficiency, the voltages of the phases should be the same, or as close to it as possible:
Calculating voltage unbalance (Vu) is pretty straightforward:- Average the voltage across all three phases (Va)
- Calculate the highest deviance from the average (Vm)
- Divide the difference by average voltage and multiply it by 100
[(Va-Vm)X100] ÷ Va = Vu
With an average voltage of 460V, just a 5V difference creates a voltage unbalance of 1.1%. While National Electrical Manufacturers Association (NEMA) and Standard EN50160 call for a maximum unbalance of 5% and 2% respectively, a difference of 1% or below is usually recommended.
- Current Unbalance Current unbalance is similar to voltage imbalance. As opposed to the voltage, it is calculated by measuring the difference between the current being drawn at each of a three-phase motor's leg.The method for correcting current unbalance depends on the factors causing it:
- Power-factor correcting device for unbalance caused by the power supply
- Rewinding or replacing the motor for internal faults or faulty installation
- In some cases, buying a new motor is preferred-
- Motors over 15 years old and under 40hp
- Non-specialty motors under 15hp
- Rewinding cost exceeds 50% of purchasing a new motor
- Power Factor The power factor is the ratio (or percentage) of the real power (in KW) of a motor and its apparent (total) power (in KVA). Apparent power is an expression of the real power of the motor and its reactive power in kilovars (kVAR). The power factor should be evaluated on all major loads and circuits, not just motors.An increase in a motor's reactive power increases the apparent power. This causes the power factor to decrease.
The closer the power factor is to 1 (or 100%), the better, so decreasing reactive power is generally better for efficiency.The goal of ascertaining the power factor is to identify which loads cause reactive power to lag and design strategies that can improve the power factor.
Phase 3 - Prolong Life Period
Apart from the methods mentioned above, there are a few more strategies you can use to increase the life period of motors in your facility, and thus their operational efficiency too:
- Lamination - Instead of cheaper carbon steels, lamination containing steels that have a little silicon can be used. Using thinner lamination and increasing their length reduces core losses by limiting the effects of saturation and hysteresis.
- Lubrication - The lubrication interval is decided by a number of factors, so you should be careful while applying lubricants. Different types of grease, even those with the same elements, should never be mixed.
- Insulation - Efficiency can also decrease due to eddy currents. These can be minimized by insulating sheets or lamination properly.
_____________
Stay tuned! Best ideas for energy efficiency and energy transition...