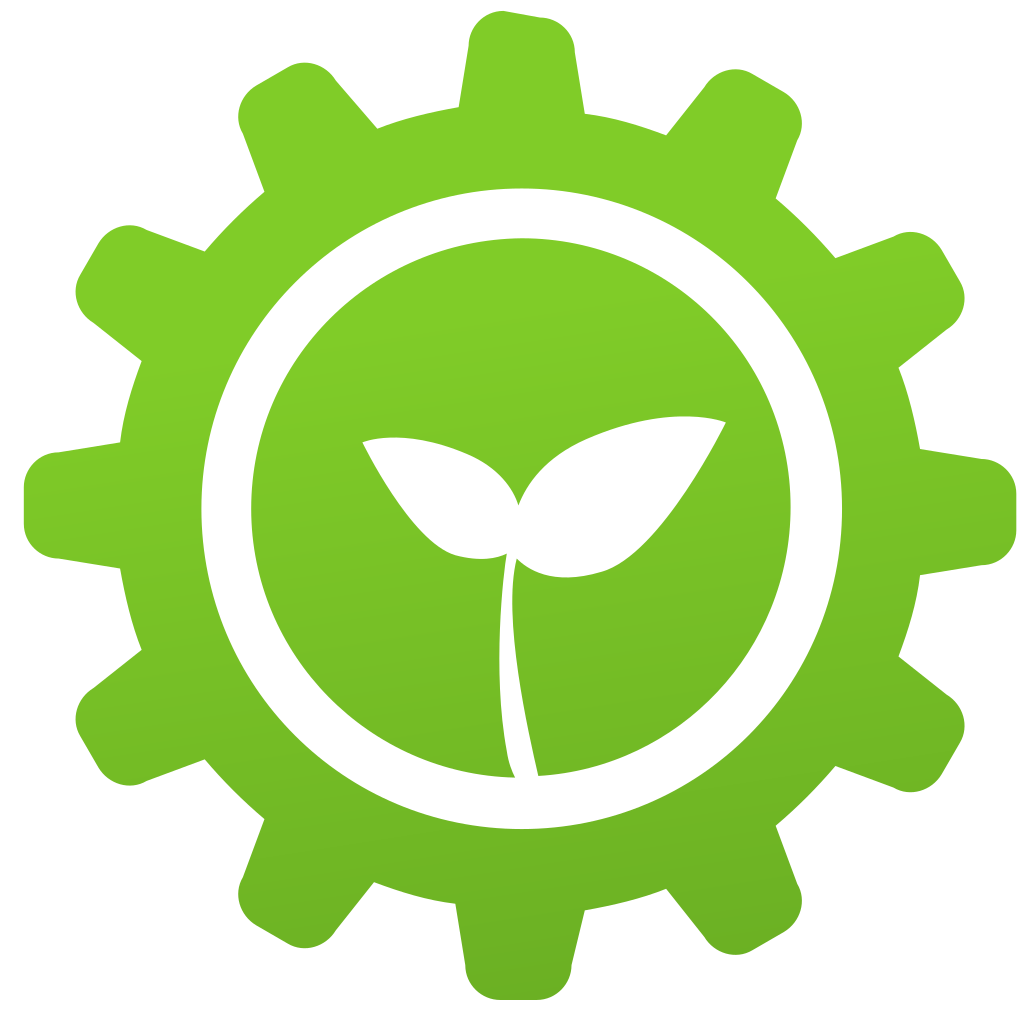
El calor reciclado de las fábricas beneficia a las industrias y al medio ambiente
Resumen
La investigación financiada por la UE está cerrando el círculo con sistemas novedosos que recuperan el calor residual y lo devuelven para su reutilización. La mayor parte del calor de los procesos se pierde en el medio ambiente en forma de corrientes de escape o de descarga. Recuperar y reutilizar este calor reduce el consumo de energía, las emisiones y los contaminantes. El proyecto ETEKINA, financiado por la UE, ha desarrollado unos novedosos intercambiadores de calor de tubo a medida. Estos recuperan con éxito el calor sin contaminación cruzada y lo devuelven a la fábrica para utilizarlo en otros procesos. Una novedosa herramienta de replicabilidad ayudará a evaluar rápidamente el potencial de recuperación de calor residual de futuros clientes. Además de su
su eficacia, que reduce los costes y las emisiones, también tienen un corto retorno de la inversión.
Abrir artículo completo
El calor reciclado de las fábricas beneficia a las industrias y al medio ambiente
Los procesos industriales representan más de una cuarta parte del consumo de energía primaria en Europa y producen una enorme cantidad de calor. La investigación financiada por la UE está cerrando el círculo con sistemas novedosos que recuperan el calor residual y lo devuelven para su reutilización en las líneas de procesos industriales.
La mayor parte del calor de los procesos se pierde en el medio ambiente en forma de corrientes de escape o de descarga. Recuperar y reutilizar este calor reduce el consumo de energía, las emisiones y los contaminantes. Permite a las industrias reducir costes, cumplir la normativa y mejorar su imagen corporativa, con repercusiones más amplias en la competitividad. Uno de los mayores retos es hacer frente a la inmensa variedad de temperaturas y componentes de los gases de escape, lo que dificulta el uso de intercambiadores de calor estándar. El proyecto ETEKINA, financiado por la UE, ha desarrollado novedosos intercambiadores de calor de tubo a medida (HPHE) que se han probado con éxito en las industrias de la cerámica, el acero y el aluminio.
Un amplio espacio de diseño satisface las necesidades de flujos de escape complejos
Los tubos de calor son tubos sellados en ambos extremos que contienen un fluido de trabajo en saturación, lo que significa que cualquier aumento de temperatura provocará su vaporización. Se utilizan para la gestión del calor en aplicaciones que van desde ordenadores hasta satélites y naves espaciales. En un HPHE, los tubos de calor se instalan en haces unidos a una placa y se colocan en una carcasa. Una fuente de calor, como los gases de escape, fluye hacia la sección inferior. El fluido de trabajo se vaporiza y sube por los tubos, donde un disipador de calor, como el aire frío, fluye hacia la parte superior de la carcasa y absorbe el calor. La estructura cerrada minimiza las pérdidas, mientras que la placa minimiza la contaminación cruzada entre el gas de escape y el aire. Las HPHE requieren superficies más pequeñas para una mayor transferencia de calor en relación con los enfoques convencionales. Esto los hace muy eficientes y mitiga el ensuciamiento. El reto consiste en elegir los parámetros de forma que se recupere el mayor calor posible de los complejos flujos de residuos. Hay muchos parámetros, como el número, el diámetro, la longitud y el material de los tubos de calor, su configuración de montaje y el fluido de trabajo.
De los modelos a las fábricas
Dado el inmenso espacio de parámetros, se desarrollaron modelos dedinámica de fluidos computacional y simulación de sistemas transitorios (TRNSYS) para ayudar a los científicos a diseñar HPHE a medida para tres aplicaciones industriales. Por ejemplo, la HPHE de flujo cruzado, con aletas y resistente a las incrustaciones (las aletas aumentan la superficie para aumentar la transferencia de calor) diseñada para recuperar el calor residual de un horno de rodillos de cerámica fue la primera de esta configuración aplicada en la industria cerámica. Las carcasas de los tubos de calor eran de acero al carbono y el fluido de trabajo era el agua. "Hemos superado el objetivo del proyecto de recuperar un mínimo del 40% del calor residual de los flujos de escape. Además, nuestros HPHE son mucho más compactos que los intercambiadores de calor convencionales, lo que permite ahorrar un valioso espacio en la fábrica. Además de su eficiencia, que reduce los costes y las emisiones, también tienen un corto retorno de la inversión", afirma Hussam Jouhara, de la Universidad Brunel de Londres y coordinador técnico y científico del proyecto ETEKINA. Los sistemas recuperaron con éxito el calor sin contaminación cruzada y lo devolvieron a la fábrica para utilizarlo en otros procesos. El concepto de HPHE desarrollado en el contexto de ETEKINA es altamente escalable y puede adaptarse a cualquier tipo de escape industrial en un amplio rango de temperaturas y para una variedad de disipadores de calor, incluyendo aire, agua y aceite. Una novedosa herramienta de replicabilidad ayudará a evaluar rápidamente el potencial de recuperación de calor residual de futuros clientes.
Este artículo ha sido publicado en EN, DE, ES, FR, IT y PL por CORDIS