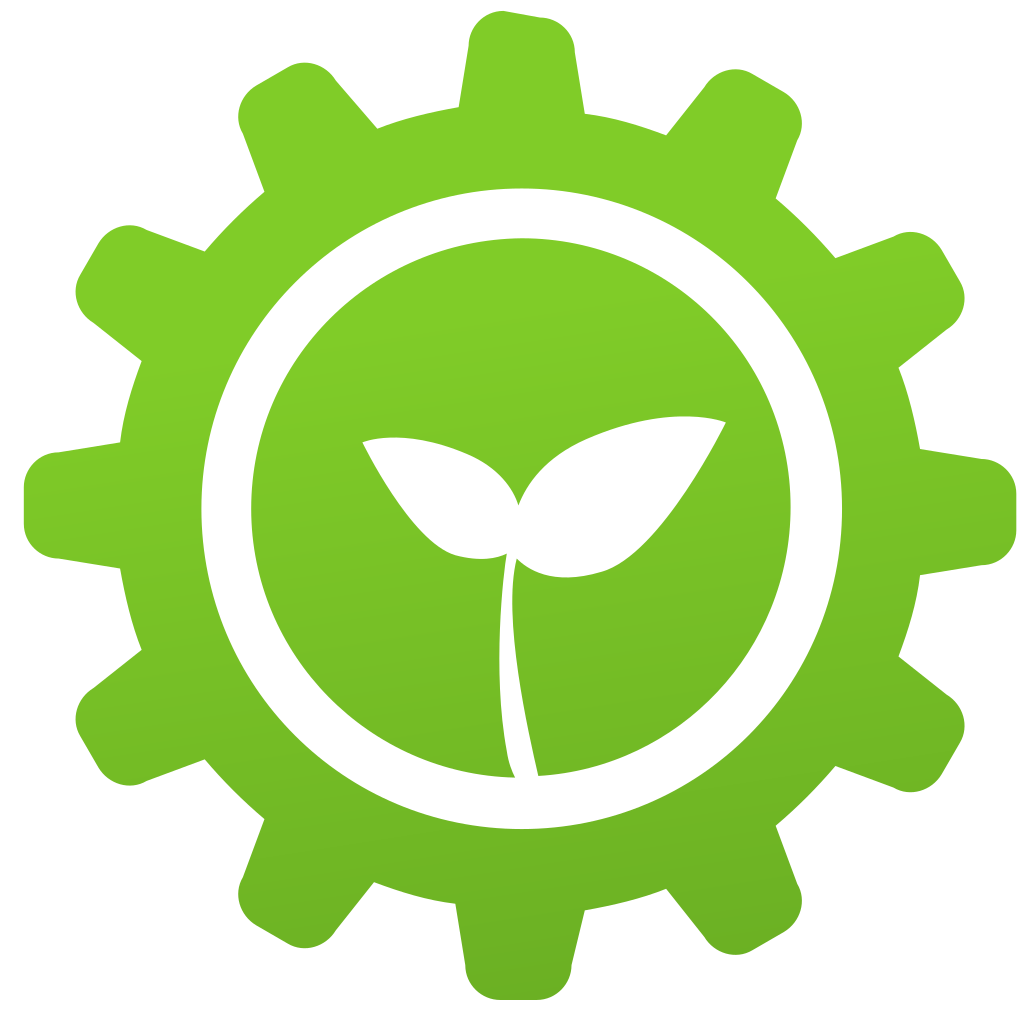
La transformación de las industrias de alto consumo energético
Resumen
El proyecto ETEKINA pretende recuperar entre el 57 y el 70% del flujo de calor residual de las industrias que consumen mucha energía y que hasta ahora sólo sale por la chimenea. Los nuevos intercambiadores de calor de tubo son una herramienta eficaz para recuperar el calor de los procesos industriales. Están sellados y llenos de un líquido volátil que transfiere el calor de forma rápida y pasiva de la parte inferior a la superior. Y de hecho, ya tenemos algunas ideas para optimizar la eficiencia del sistema. Esto también puede reproducirse en industrias similares, afirma la Dra. Nerea Nieto. Afirma que la transición a procesos neutros en carbono es real y que la recuperación del calor residual será sin duda parte de la solución. Pero añade que otras industrias tendrán que cumplir los objetivos de la transición para limpiar y reducir la pérdida de calor residual y reducir el uso de energía.
Abrir artículo completo
La transformación de las industrias de alto consumo energético
Los últimos registros son alucinantes: hasta un 50% de ahorro energético y posiblemente incluso más. En los últimos cuatro años y medio se han implantado nuevos intercambiadores de calor de tubo de calor en tres emplazamientos industriales de demostración: una planta de producción de fundición de aluminio en España(Fagor Ederlan), una acería en Eslovenia(SIJ Metal Ravne) y un productor de cerámica en Italia(Atlas Concorde). Todo ello coordinado por el consorcio ETEKINA, un proyecto de investigación europeo dirigido por el centro de investigación tecnológica Ikerlan en España y la Universidad Brunel de Londres. La Dra. Nerea Nieto, ingeniera química y experta en gestión de energía eléctrica y térmica, formó parte del equipo de coordinación y desveló a ESCI algunas interioridades del complejo proceso de transformación.
Según la Dra. Nieto, más del 30% de la demanda mundial de energía primaria está relacionada con el sector industrial, incluyendo el hierro, el acero, el cemento, los productos químicos y los petroquímicos (fuente: iea). Por lo tanto, es inevitable un cambio hacia la eficiencia energética y hacia oportunidades de producción más sostenibles. En este sentido se enmarca el proyecto ETEKINA, cuyo objetivo es recuperar entre el 57 y el 70% del flujo de calor residual de las industrias de alto consumo energético que hasta ahora sólo sale por la chimenea.
Nieto: Sí. Nunca antes la eficiencia energética había sido tan importante para la industria intensiva en energía. Los tres socios industriales que participan en ETEKINA están consiguiendo ahorros significativos gracias al proyecto y eso es un hito muy importante. A los gestores energéticos les suele resultar difícil justificar una inversión para la recuperación de calor residual debido al alto rendimiento de la inversión que se espera. Sin embargo, el proyecto ETEKINA ha demostrado que es posible.
De hecho, los cálculos confirman que la inversión para instalar los nuevos intercambiadores de calor de tubo se recupera en cuestión de pocos años. De todos modos, ¿fue difícil convencer a sus socios industriales para que asumieran el riesgo de implantar una técnica completamente nueva?
Nieto: No fue fácil, ya que prefieren implantar cosas que funcionen de forma fiable durante un par de años. Otro reto fue que casi todos los centros de producción tenían que parar la producción para que pudiéramos instalar el nuevo equipo y tenerlo listo para funcionar. Eso afectó a los plazos y, además, teníamos que garantizar que todos los productos de los socios industriales siguieran haciéndose con la misma calidad que antes. Cuando cambias algo, tienes que estar seguro de que obtendrás el mismo perfil de temperatura. Y esto es algo que no se sabe hasta que se realiza la instalación y se hace algún tipo de validación o demostración. No es que nuestros socios no estuvieran seguros, pero este era un punto realmente importante en el procedimiento de puesta en marcha.
Los nuevos intercambiadores de calor de tubo de calor son una herramienta eficaz para recuperar el calor de los procesos industriales, permitiendo que el calor recuperado se utilice en otro proceso. El nuevo invento de los tubos de calor que están implementando en el proyecto ETEKINA es que están sellados y llenos de un líquido volátil que transfiere el calor de forma rápida y pasiva desde la parte inferior a la superior. ¿El desarrollo e implementación de los mismos fue el principal reto técnico del proyecto?
Nieto: Resumiendo, los mayores problemas no han estado relacionados con el intercambiador de calor de tubo de calor en sí, sino con toda la ingeniería que rodea al intercambiador de calor de tubo de calor o el equipo auxiliar, el diseño detallado y el sistema de control. En el sitio de demostración en Fagor Ederlan en España, estos han sido los principales problemas y hemos hecho muchas comprobaciones para ver si las válvulas cierran correctamente y si hay pérdidas de calor. Por lo tanto, esto es algo que realmente hay que tener en cuenta a la hora de planificar una instalación de este tipo, ya que al final es tiempo y también dinero.
Pero, finalmente, en los tres lugares de demostración, ya sea la acería de Eslovenia, la producción de fundición de aluminio de España o el productor de cerámica de Italia, se obtuvieron excelentes resultados en términos de viabilidad, usabilidad y ahorro de energía.
Nieto: Sí, por ejemplo, los últimos datos registrados en la producción de fundición de aluminio en España muestran una reducción del consumo del 48% en la primera zona del horno. Ahora tenemos que hacer un análisis de todo el consumo, pero las cifras iniciales son bastante optimistas. Y de hecho, ya tenemos algunas ideas para optimizar la eficiencia del sistema. Así que estas cifras pueden ser incluso mejores al final del proyecto.
Dado que el proyecto ETEKINA se encuentra en su fase final, ¿cree que los resultados que puede ofrecer convencerán también a otras industrias que consumen mucha energía para que apliquen esta nueva técnica de intercambiador de calor de tubos de calor?
Nieto: Sí, definitivamente, esto puede ser replicado en industrias similares también. Y, de hecho, algunos de nuestros socios industriales ya han mostrado su interés y su compromiso de instalar más intercambiadores de calor de tubo de calor en sus plantas. Y durante la última conferencia, representantes de otras industrias también mostraron su interés por esta solución para la recuperación del calor residual. El compromiso de las industrias que hacen un uso intensivo de la energía para alcanzar los objetivos que se esperan de ellas en la transición hacia procesos neutros en carbono es real y la recuperación de calor residual será sin duda parte de la solución.
Dr. Nieto, usted no sólo ha contribuido al proyecto como experto en el desarrollo de plataformas de gestión de la energía y soluciones de recuperación de calor, sino que también ha asumido el papel de coordinador de su colega Bakartxo Egilegor: ¿cómo ha sido la supervisión de un consorcio de 10 socios en cinco países y tres centros de demostración?
Nieto: Diría que Bakartxo hizo el trabajo más duro para tener un proyecto exitoso al final. Hubo muchos problemas que tuvo que superar, como retrasos, Covid-19, diferentes problemas en los casos de demostración, etc. Cuando asumí la coordinación del proyecto, las tres HPHE estaban en marcha y funcionando. En cualquier caso, siempre es un reto coordinar un consorcio tan grande y creo que el mayor reto al que tendremos que enfrentarnos ahora es el último periodo de informes y la reunión de revisión final con la CE. Afortunadamente, podemos decir que al final tenemos un proyecto exitoso, ¡lo cual es realmente estupendo!