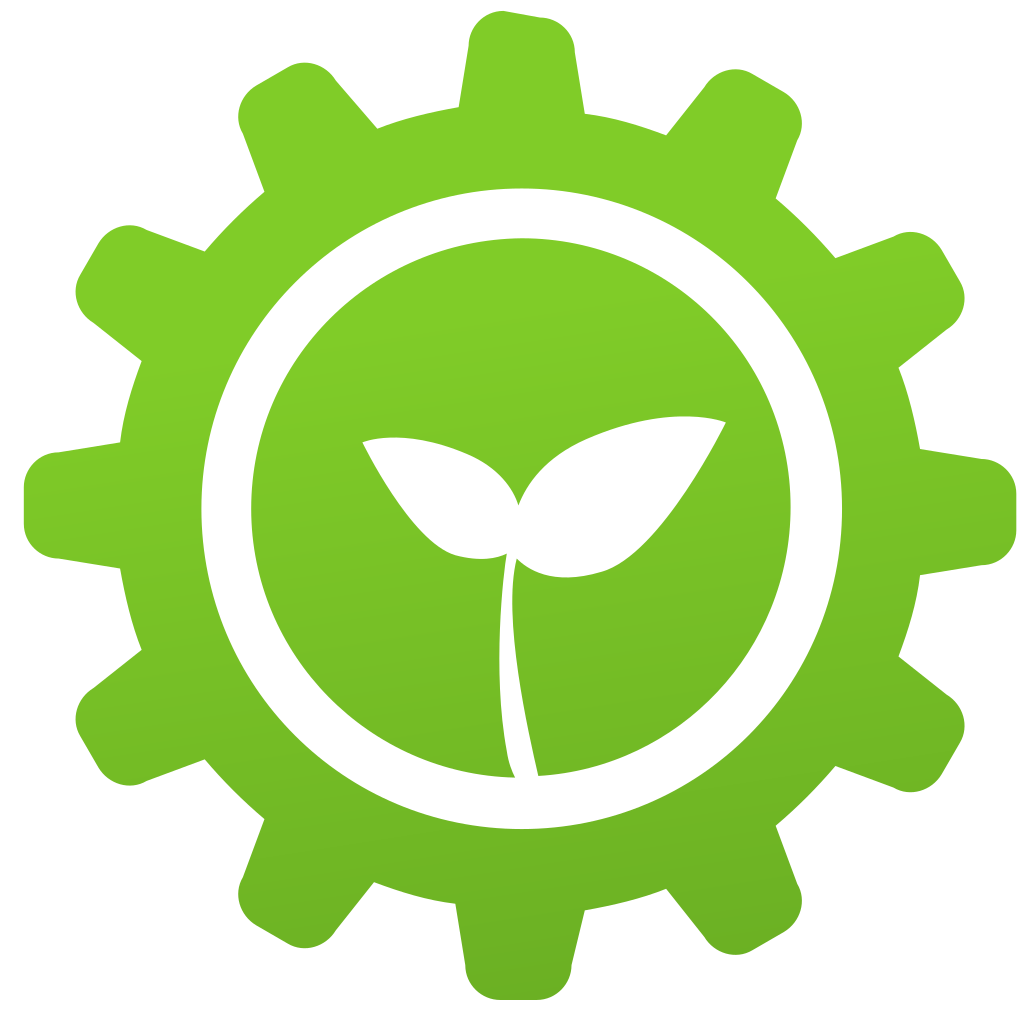
Casos Prácticos
Cómo la reutilización del calor residual puede hacer que el aluminio esté más cerca de convertirse en una industria más ecológica
Resumen
Las nuevas tecnologías de recuperación del calor residual pueden acercar a la industria a la consecución de métodos de producción más limpios. El aluminio es el segundo metal más producido y una de las materias primas más recicladas del mundo. En algunas industrias, más del 90% se recicla y el 75% del aluminio que se ha producido sigue en circulación hoy en día. La producción de aluminio deja huellas en el medio ambiente que incluyen emisiones de acidificación. Los recuperadores, los precalentadores de aire o las bombas de calor son algunas de las alternativas que mencionan. Los intercambiadores de calor por tuberías son el corazón del proyecto ETEKINA, que pretende recuperar más del 40% de
del contenido de calor residual accesible en los flujos que se pierden en la atmósfera de las industrias de alto consumo energético. El proceso requiere un nivel de energía tan intenso que, en Estados Unidos, consume aproximadamente el 5% de toda la electricidad generada en ese país, según la American Aluminium Association. La mayoría de los procesos utilizan altas temperaturas, lo que significa que una gran parte de esta energía.
Abrir artículo completo
Cómo la reutilización del calor residual puede hacer que el aluminio esté más cerca de convertirse en una industria más ecológica
El aluminio es una de las materias primas más recicladas del mundo, pero los procesos implicados en la producción de este metal siguen dejando un elevado impacto medioambiental en el planeta. Las nuevas tecnologías de recuperación del calor residual pueden acercar a la industria a métodos de producción más limpios.
El aluminio es el segundo metal más producido y una de las materias primas más recicladas del mundo. Esta capacidad de ser recuperado y reutilizado indefinidamente da a la industria el potencial de ofrecer una alternativa más ecológica y limpia que otros materiales poco respetuosos con el medio ambiente. Sin embargo, factores como el enorme consumo de energía y el uso ineficiente del calor que supone tanto la producción primaria de este metal a partir del mineral de bauxita como la producción secundaria a partir de la chatarra, restan esa oportunidad; haciendo que la industria del aluminio sea responsable de al menos el 1% de las emisiones de gases de efecto invernadero añadidas a la atmósfera por la actividad humana y del 2,5% delCO2.
"Lo bueno del aluminio es que, en algunas industrias, más del 90% se recicla y el 75% del aluminio que se ha producido sigue en circulación hoy en día", afirma Daniel Brough, investigador del Instituto de Futuros Energéticos de la Universidad de Brunel de Londres e ingeniero de una instalación de aluminio secundario. Forma parte de un grupo de expertos que diseñan intercambiadores de calor de tubos en el marco del proyecto ETEKINA, un programa financiado por la Unión Europea que pretende recuperar más del 40% del contenido de calor residual accesible en los flujos que se pierden en la atmósfera de las industrias de alto consumo energético.
"Hay diferentes tecnologías que pueden aplicarse para reducir las emisiones de gases de efecto invernadero [en la fabricación de aluminio], la más influyente es el proyecto Elysis, con sede en Montreal. Pero la recuperación del calor residual es una parte importante de la ecuación: la industria del aluminio es una gran productora de calor residual que podría aprovecharse", añade.
La producción de aluminio deja huellas en el medio ambiente que incluyen emisiones de acidificación, daños relacionados con el uso de combustibles fósiles y residuos sólidos problemáticos como el lodo rojo que queda de la bauxita o la escoria salina que resulta del reciclaje de este metal. Sin embargo, la industria ha tomado algunas medidas para disminuir su impacto negativo en el planeta.
Una de ellas se encuentra en la amplia adopción de la energía hidroeléctrica, que ahora alimenta el 75% de la producción de aluminio primario. Otra es la modernización de los equipos, aunque todavía se pueden dar más pasos en esta materia. Por ejemplo, los hornos utilizados por las fundiciones de aluminio se siguen diseñando con métodos semiempíricos a pesar de la existencia de tecnología que podría utilizarse para diseñarlos con mayor eficiencia energética, como los análisis de dinámica de fluidos computacional.
Estas son algunas de las conclusiones que el Sr. Brough y el profesor Hussam Jouhara, de la Universidad Brunel de Londres, describen en su documento The aluminium industry: A review on state-of-the-art technologies, environmental impacts and possibilities for waste heat recovery, publicado en el International Journal of Thermofluids. Su investigación ofrece una descripción exhaustiva de los procesos y tecnologías utilizados por la industria del aluminio, así como de las herramientas ya disponibles para recuperar el calor.
Recuperadores, precalentadores de aire o bombas de calor son algunas de las alternativas que mencionan. Entre ellas, los intercambiadores de calor de tubo, el corazón del proyecto ETEKINA, se apuntan como uno de los dispositivos más prometedores para evitar el desperdicio de calor. El profesor Jouhara, que coordina las actividades técnicas dentro de ETEKINA, explica que las tecnologías convencionales ya han intentado abordar la recuperación del calor residual en la industria del aluminio con anterioridad, sin mucho éxito. "No eran adecuadas para algunos de los flujos duros que resultan de los procesos en la industria del aluminio", dice.
La recuperación del calor de la producción de aluminio no es una tarea fácil, ya que hay que recuperarlo de corrientes que arrastran gases de escape que pueden provocar corrosión o ensuciamiento. Por tanto, puede ser necesario un mantenimiento frecuente o la sustitución de componentes, lo que hace que la recuperación de calor no sea económicamente viable. Según ambos expertos, los intercambiadores de calor de tubos de calor que se están desarrollando en el marco del proyecto ETEKINA ofrecen una solución más duradera y económica en el camino de "recuperar lo irrecuperable", ya que son más eficaces a la hora de transferir el calor, tienen medidas superiores contra la contaminación cruzada y cada tubo de calor individual funciona de forma independiente, lo que anula el riesgo de que todo el sistema falle.
"Los intercambiadores de calor de tubo no tienen piezas móviles, así que desde ese punto de vista, lo que puede fallar es muy limitado. El único mantenimiento que requieren es la limpieza periódica", explica el profesor Jouhara. "Disponer de esta nueva tecnología significa que ahora podemos abordar áreas que eran imposibles de abordar debido a la naturaleza corrosiva de estos escapes, esto es algo que la tecnología de los tubos de calor ha hecho posible. Así pues, los avances en el diseño de los intercambiadores de calor nos acercan lo más posible a hacer viable un proceso ecológico en la industria del aluminio."
Tres aplicaciones del calor residual
La producción de aluminio requiere un nivel de energía tan intenso que, en Estados Unidos, consume aproximadamente el 5% de toda la electricidad generada en ese país, según la American Aluminium Association. La mayoría de los procesos utilizan altas temperaturas, lo que significa que una gran parte de esta energía se pierde en el medio ambiente en forma de calor residual. Para evitarlo, los autores sugieren combinar distintos tipos de intercambiadores de calor para concentrar las mayores pérdidas en las fases más intensivas del proceso.
Los precalentadores de aire, los economizadores y los intercambiadores de calor de tubo pueden ayudar a reutilizar el calor residual de los gases de escape, mientras que los termocompresores pueden ayudar a reutilizar el vapor. El documento describe tres posibles aplicaciones del calor residual recuperado mediante estas tecnologías:
- Calefacción de espacios y distritos: dependiendo del clima de la ubicación de la fundición, el calor residual recuperado puede redirigirse para proporcionar calefacción a las oficinas adyacentes o a la comunidad local. En AlcoaFjarðaál, una fundición de aluminio de Islandia, se está estudiando la viabilidad de proporcionar a las comunidades circundantes calefacción urbana a partir del calor residual.
- Optimización de la producción de aluminio: el calor residual puede utilizarse para acortar ciertas etapas de la producción y lograr resultados más eficientes. Estas aplicaciones potenciales incluyen el desrevestimiento y el precalentamiento de la chatarra para eliminar la humedad y reducir la cantidad de energía necesaria para fundirla, utilizando una tecnología de quemadores especializada que reutiliza el calor residual.
- Generación de electricidad: dependiendo del grado de calor, se pueden utilizar diferentes métodos para convertir el calor residual en electricidad y reducir los costes de funcionamiento.
La reducción de gastos es un argumento tentador para que las empresas inviertan en tecnologías de recuperación de calor residual, pero no el único, como explica el Sr. Brough: "Hay dos razones principales adicionales. La más importante es el uso sostenible y consciente de los recursos naturales para evitar cualquier impacto futuro sobre el planeta y las generaciones futuras. La otra es la mejora de la imagen de responsabilidad corporativa y social de las empresas".
Ambos expertos esperan que los intercambiadores de calor con tubos de calor hagan más eficiente y asequible la recuperación del calor residual en industrias de alto consumo energético como la del aluminio, el acero y la cerámica. Pero sobre todo, dice el profesor Jouhara, para ofrecer una solución donde otras tecnologías han fracasado: "No competimos con los sistemas convencionales si los flujos son estándar y los diseños convencionales pueden hacerles frente. Los tubos de calor pueden ser beneficiosos en áreas en las que no se dispone de ninguna solución o la situación es difícil hasta el punto de que no hay ningún sistema convencional disponible para tratar la aplicación de recuperación de calor residual."
Autor: Stefania Gozzer