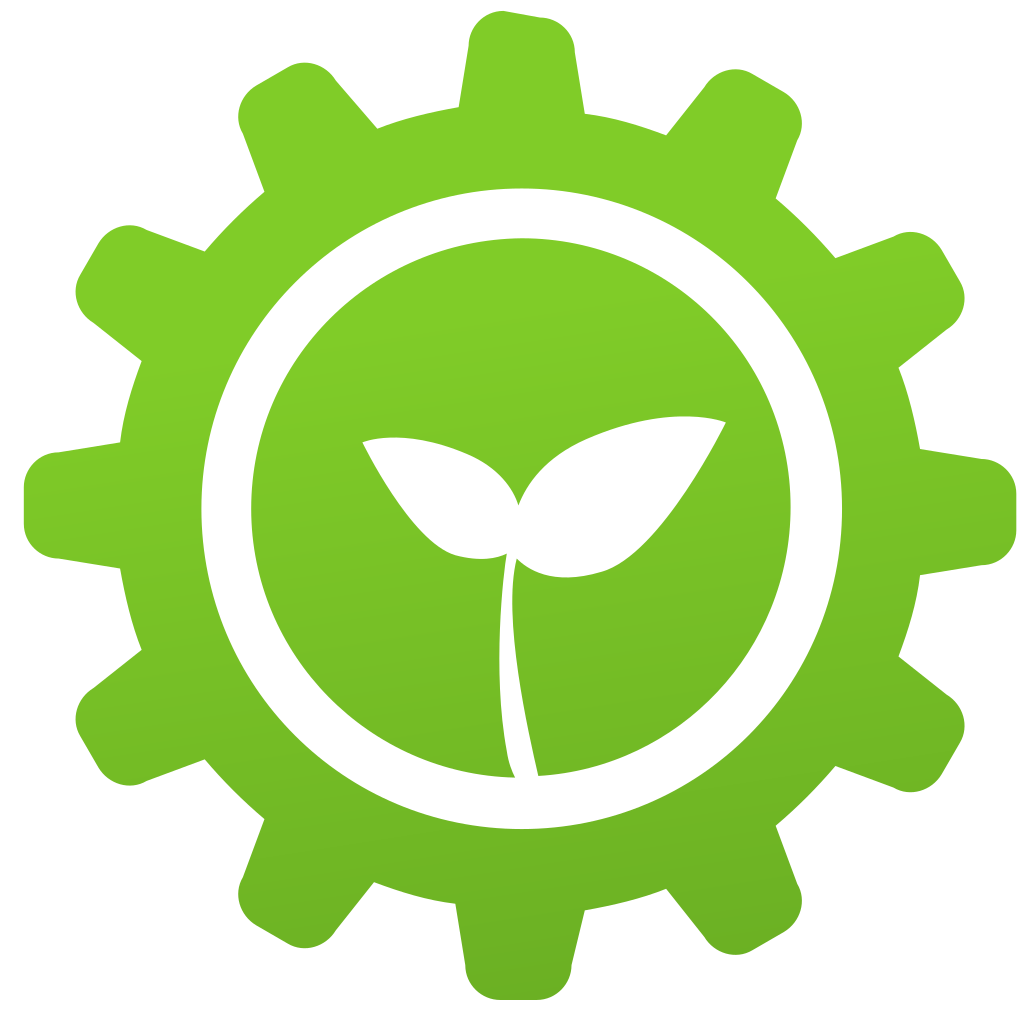
HPHE et fours plus écologiques : une combinaison qui peut faire plonger les émissions dans l'industrie de l'aluminium
Résumé
Insertec est un important fabricant de fours industriels basé dans la province espagnole de Biscaye. C'est un partenaire crucial dans l'une des trois études de cas où ETEKINA teste une nouvelle gamme d'échangeurs de chaleur à caloducs. La combinaison des HPHE et des ajustements des fours pour augmenter leur efficacité énergétique aidera l'industrie de l'aluminium à améliorer son empreinte carbone dans le monde entier. La demande de réduction de l'empreinte carbone dans ces processus n'est pas la même sur tous les continents. L'Union européenne exige de plus en plus que l'industrie devienne plus verte. Et, bien sûr, il y a au moins
au moins cinq grands clients de l'UE ayant des activités dans le monde entier qui demandent des améliorations des équipements pour les rendre plus propres. Et comment les fours peuvent-ils contribuer à réduire l'empreinte carbone totale ? Et comment l'industrie peut-elle réduire les émissions dans une usine réduire l'empreinte carbone totale ? Et c'est devenu une question de marketing et un argument de vente : Si vous êtes capable de réduire cela. pour rendre les fours plus verts.
Ouvrir l'article complet
HPHE et fours plus écologiques : une combinaison qui peut faire plonger les émissions dans l'industrie de l'aluminium
Les fours peuvent représenter plus de 70 % de la consommation d'énergie dans les usines dédiées à la production d'aluminium secondaire, en libérant 25 à 35 % de la chaleur qu'ils produisent. C'est pourquoi Insertecun important fabricant de fours industriels basé dans la province espagnole de Biscaye, a été un partenaire crucial dans l'une des trois études de cas où le projet financé par l'Union européenne ETEKINA financé par l'Union européenne, teste une nouvelle gamme d'échangeurs de chaleur à caloducs (HPHE). La combinaison des HPHE et des ajustements qu'Insertec apporte aux fours pour accroître leur efficacité énergétique aidera l'industrie de l'aluminium à améliorer son empreinte carbone dans le monde entier.
Ignacio Yebra, directeur des grands comptes de la société, explique dans cette interview le rôle d'Insertec dans ETEKINA.
Yebra : Notre rôle dans le projet consiste à adapter le système chez Fagor Ederlan, l'un de nos partenaires dans le projet ETEKINA, pour intégrer le HPHE dans un four existant qui a été construit il y a environ 10 ans par Insertec. Nous sommes les concepteurs et les fabricants, donc nous le savons mieux que quiconque. Actuellement, nous sommes dans la phase où le système, tous les tubes et les boucles de contrôle, ont été installés dans le four de l'usine et nous nous assurons que tout est en place avant de commencer les essais réels.
Le projet ETEKINA vise à récupérer jusqu'à 70 % du flux de chaleur résiduelle dans les industries à forte intensité énergétique telles que l'acier, l'aluminium et la céramique. Certains de ces secteurs, en particulier l'aluminium, ne sont pas nouveaux pour Insertec, mais qu'en est-il de la composante de récupération de la chaleur ? La réutilisation de la chaleur est-elle un sujet sur lequel vous aviez déjà travaillé ?
Yebra : Nous essayons d'être aussi écologiques que possible dans nos conceptions, en progressant avec chaque produit en améliorant le brûleur lui-même et son intégration dans nos fours pour réduire la consommation d'énergie, c'est un must pour nous. Nous essayons également de rediriger une partie des gaz d'échappement vers d'autres processus. Cependant, ce que nous faisons ici maintenant avec le HPHE est complètement nouveau.
Quels changements le HPHE apporte-t-il à votre industrie ?
Yebra : Actuellement, les fumées sont dirigées vers un système de dépoussiérage et l'atmosphère, ce qui signifie que toute cette chaleur est perdue. Avec le HPHE, nous récupérons toutes ces fumées chaudes et les utilisons dans le processus suivant, qui se déroule dans le même four. Le four comporte deux chambres principales, et la température peut atteindre 500 °C dans la première, où le traitement thermique de mise en solution a lieu. Ensuite, le métal est trempé avant d'entrer dans la deuxième chambre, où le vieillissement se produit à environ 200°C. Les deux chambres ont besoin de chaleur et, avec le HPHE, nous utiliserons la chaleur de la première unité pour chauffer la seconde au lieu de la générer avec des brûleurs. Par conséquent, nous éviterons, ou du moins réduirons considérablement, la consommation de gaz naturel dans cette deuxième zone du four.
Quels sont les défis à relever ? Le premier est que les pièces que nous traitons dans ce type de fours sont des pièces de sécurité, la température doit donc être très contrôlée. Nous parlons de plus ou moins 5 °C tout au long du processus. Nous ne pouvons pas sortir de cette fourchette, car nous aurions des pièces de mauvaise qualité qui ne pourraient pas être utilisées à des fins de sécurité. En intégrant le HPHE, nous ajoutons donc un autre facteur externe à contrôler. Nous devons donc récupérer toute cette énergie tout en contrôlant le processus et les exigences de l'usine.
La réduction de l'empreinte carbone est devenue une priorité pour de nombreuses entreprises. En tant que fournisseur d'équipements de chauffage industriel, qui rejettent traditionnellement une grande quantité d'émissions dans l'atmosphère, comment votre technologie dans les fours pour l'industrie de l'acier et de l'aluminium a-t-elle évolué pour répondre à ces besoins ?
Yebra : La demande de réduction de l'empreinte carbone dans ces processus n'est pas la même sur tous les continents. Actuellement, nous pensons que l'Europe et le Japon sont les principales régions où les entreprises estiment que cela est devenu obligatoire. Bien sûr, tout le monde veut réduire la chaleur résiduelle, mais tout le monde n'est pas prêt à payer pour ces nouvelles technologies. Mais la demande est croissante. Par exemple, certains de nos clients ont déjà commencé à promouvoir leurs produits en informant leurs clients de l'empreinte laissée par leurs processus et leurs produits. Ainsi, pour eux, c'est aussi devenu une question de marketing et un argument de vente : s'ils ont des procédés plus propres, les clients les considéreront. Et, bien sûr, l'Union européenne exige de plus en plus que l'industrie devienne plus verte. Je ne peux pas donner de noms (la confidentialité est un impératif pour nous), mais nous avons au moins cinq grands clients de l'UE qui ont des activités dans le monde entier et qui demandent des améliorations de leurs équipements pour les rendre plus propres.
Et comment les fours peuvent-ils contribuer à réduire l'empreinte carbone totale d'une usine ?
Yebra : Par exemple, dans l'usine d'aluminium où nous testons le HPHE d'ETEKINA, les fours sont l'un des équipements les plus consommateurs de gaz naturel. Donc, si vous pouvez réduire cette consommation en fabriquant des fours plus écologiques, vous réduirez un grand pourcentage des émissions rejetées par l'ensemble de l'usine.
Quelle a été l'expérience de la participation à un projet Horizon 2020, et sur quels autres projets de recherche travaillez-vous en ce moment ?
Yebra : Il s'agit de notre deuxième projet Horizon 2020, et je dirais qu'il a été plus difficile car, dans le précédent, nous travaillions avec un four dans un " environnement de laboratoire " (hors de la ligne de production), alors que maintenant nous améliorons un four existant qui est actuellement actif dans une installation industrielle. Nous devons donc travailler sur le projet en parallèle avec les opérations de l'usine. Outre Horizon 2020, nous participons activement à la recherche avec le ministère espagnol de l'Industrie et le Centre pour le développement de la technologie industrielle (CDTI), ainsi qu'à des projets locaux avec le gouvernement du Pays basque et des institutions de Biscaye, puisque nous sommes basés dans cette région. Je dirais donc que nous participons à 10-12 projets en ce moment.
Certains d'entre eux ont pour objectif de réduire les émissions et la consommation d'énergie, tandis que d'autres sont davantage liés à la sécurité, aux nouveaux produits, aux nouveaux objectifs de production, etc. Par exemple, nous appliquons des technologies robotiques à des processus qui sont actuellement réalisés par des personnes et où il existe un facteur de risque pour l'employé. Nous étudions également l'électrification des fours à gaz existants. Historiquement, en Europe, la plupart des fours qui nécessitent un certain niveau de température ont été construits pour fonctionner au gaz naturel en raison de son coût par rapport à celui de l'électricité. Dans d'autres pays/continents, où l'électricité était moins chère, ou lorsque les ressources naturelles locales le permettaient, l'accent a été mis sur les équipements électriques. En Europe, les fours à gaz naturel sont les modèles les plus courants que l'on trouve dans les usines.
Pensez-vous que cela va changer dans un avenir proche ?
Yebra : Oui, je le pense. L'un des projets de recherche et développement dans lequel nous sommes impliqués est en partenariat avec une entreprise électrique. Nous essayons de convertir les fours à gaz naturel existants en fours électriques. Cela n'est pas toujours possible avec la technologie actuelle, mais nous y travaillons également. Et si nous obtenions de l'électricité à partir de ressources naturelles, l'empreinte serait beaucoup plus faible.
Quels sont les défis à relever pour produire des fours à haut rendement énergétique ?
Yebra : Lorsqu'un brûleur est allumé, il y a toujours des émissions. Le volume peut être plus ou moins important, mais elles seront toujours là. Les fabricants de brûleurs essaient d'améliorer cette situation, et nous le faisons également en intégrant les derniers développements et en ayant un contrôle technique de l'ensemble du four. Les brûleurs ont tendance à rester allumés en permanence lorsque le système a besoin de chaleur. Dans le cadre du projet ETEKINA, nous faisons tout notre possible pour les éteindre et réduire ainsi la consommation. Si le HPHE nous permettait d'atteindre les températures requises par les fours avec la chaleur des fumées provenant de la première chambre, nous n'aurions pas besoin d'utiliser des brûleurs dans la seconde, de sorte que ces fours rejetteraient moins d'émissions, réduisant ainsi considérablement leur empreinte carbone.
Auteur : Stefania Gozzer