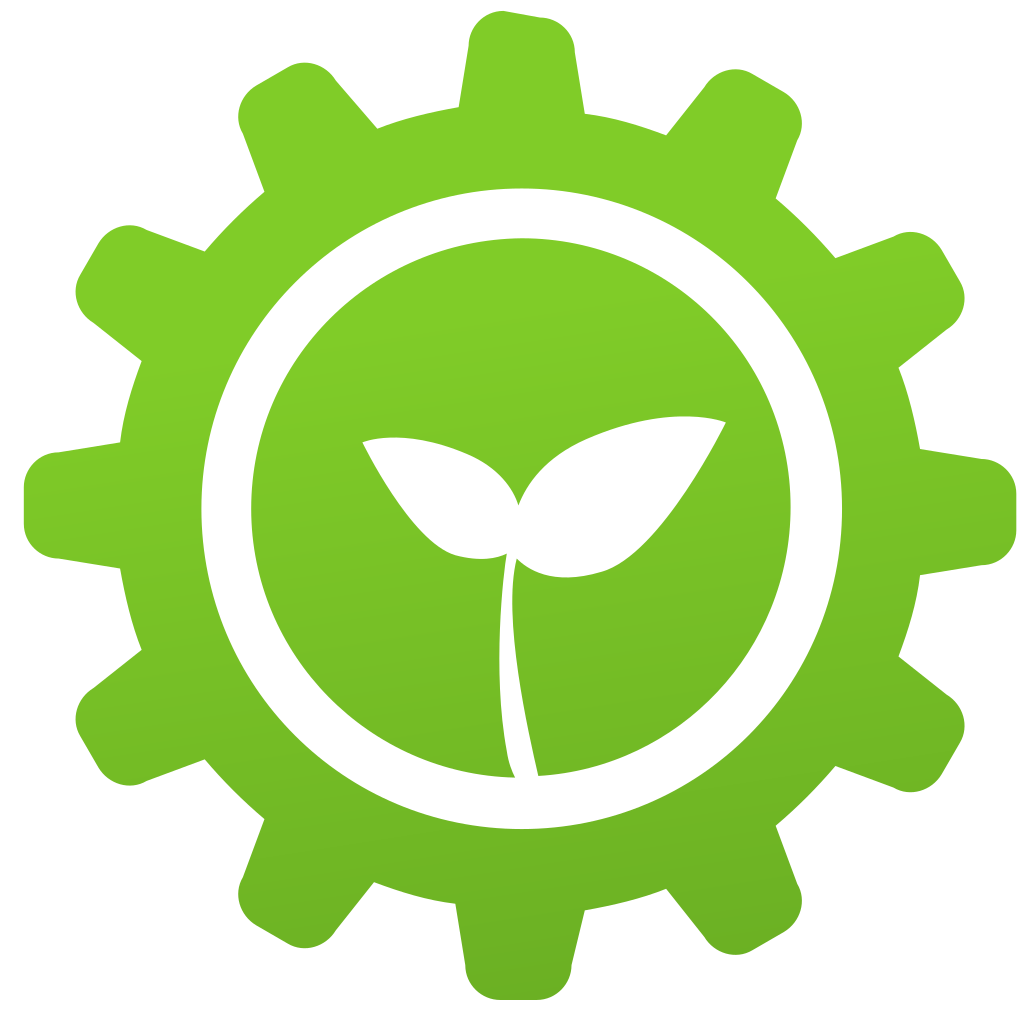
HPHE y hornos más ecológicos: un combo que puede hacer caer las emisiones en la industria del aluminio
Resumen
Insertec es un fabricante líder de hornos industriales con sede en la provincia española de Vizcaya. Es un socio crucial en uno de los tres casos de estudio en los que ETEKINA está probando una nueva gama de intercambiadores de calor de tubo de calor. La combinación de HPHE y los ajustes en los hornos para aumentar su eficiencia energética ayudarán a la industria del aluminio a mejorar su huella de carbono en todo el mundo. La exigencia de reducir la huella de carbono en estos procesos no es la misma en todos los continentes. La Unión Europea exige cada vez más que la industria sea más ecológica. Y, por supuesto, hay al menos
al menos cinco grandes clientes de la UE con operaciones en todo el mundo que piden mejoras en los equipos para que sean más limpios. Y cómo pueden los hornos ayudar a reducir la huella de carbono total. ¿Y cómo puede la industria reducir las emisiones en una fábrica reducir la huella de carbono total? Y se ha convertido en una cuestión de marketing y un argumento de venta: Si usted es capaz de reducir esto. para que sea más verde hornos.
Abrir artículo completo
HPHE y hornos más ecológicos: un combo que puede hacer caer las emisiones en la industria del aluminio
Los hornos pueden suponer más del 70% del consumo de energía en las plantas dedicadas a la producción de aluminio secundario, liberando entre el 25% y el 35% del calor que generan. Por eso Insertecfabricante líder de hornos industriales con sede en la provincia española de Vizcaya, ha sido un socio crucial en uno de los tres casos de estudio en los que el proyecto financiado por la Unión Europea ETEKINA está probando una nueva gama de intercambiadores de calor de tubo de calor (HPHE). La combinación de HPHE y los ajustes que Insertec está realizando en los hornos para aumentar su eficiencia energética ayudarán a la industria del aluminio a mejorar su huella de carbono en todo el mundo.
El director de cuentas clave corporativas de la empresa, Ignacio Yebra, explica en esta entrevista el papel de Insertec en ETEKINA.
Yebra: Nuestro papel en el proyecto consiste en adaptar el sistema de Fagor Ederlan, uno de nuestros socios en el proyecto ETEKINA, para integrar la HPHE en un horno existente que fue construido hace unos 10 años por Insertec. Somos los diseñadores y fabricantes, así que lo conocemos mejor que nadie. Ahora mismo estamos en la fase en la que el sistema, todos los tubos y los lazos de control, se han instalado en el horno de la planta y nos estamos asegurando de que todo esté en su sitio antes de empezar las pruebas reales.
El proyecto ETEKINA pretende recuperar hasta el 70% del flujo de calor residual en industrias de alto consumo energético como la siderúrgica, la del aluminio y la de la cerámica. Algunos de estos sectores, especialmente el del aluminio, no son nuevos para Insertec, pero ¿qué hay del componente de recuperación de calor? ¿La reutilización del calor es algo con lo que ya habían trabajado?
Yebra: Intentamos ser lo más ecológicos posible en nuestros diseños, avanzando en cada producto mejorando el propio quemador y su integración en nuestros hornos para reducir el consumo de energía, eso es algo imprescindible para nosotros. También intentamos redirigir parte de los gases de escape hacia otros procesos. Sin embargo, lo que estamos haciendo ahora con el HPHE es completamente nuevo.
¿Qué cambios aporta la HPHE a su sector?
Yebra: Actualmente, los humos van a un sistema de filtros de mangas y a la atmósfera, lo que significa que todo este calor se pierde. Con la HPHE recuperamos todos estos humos calientes y los utilizamos en el siguiente proceso, que tiene lugar en el mismo horno. Tiene dos cámaras principales, y la temperatura puede alcanzar los 500 °C en la primera, donde se produce el tratamiento térmico por disolución. A continuación, el metal se enfría antes de pasar a la segunda cámara, donde se produce el envejecimiento a unos 200 °C. Ambas cámaras necesitan calor y, con la HPHE, utilizaremos el calor de la primera unidad para calentar la segunda en lugar de generarlo con quemadores. Por lo tanto, evitaremos, o al menos disminuiremos sustancialmente, el consumo de gas natural en esa segunda zona del horno.
¿Cuáles son los retos? El primero es que las piezas que tratamos en este tipo de hornos son piezas de seguridad, por lo que la temperatura debe estar muy controlada. Estamos hablando de más-menos 5 °C en todo el proceso. No podemos salirnos de este rango porque tendríamos piezas de baja calidad que no se pueden utilizar para la seguridad. Por lo tanto, al integrar el HPHE estamos añadiendo otro factor externo a controlar, por lo que tenemos que recuperar toda esta energía a la vez que controlamos el proceso y las necesidades de la planta.
La reducción de la huella de carbono se ha convertido en una prioridad para muchas empresas. Como proveedor de equipos de calefacción industrial, que tradicionalmente liberan una gran cantidad de emisiones a la atmósfera, ¿cómo ha evolucionado su tecnología en hornos para la industria del acero y el aluminio para satisfacer estas necesidades?
Yebra: La demanda de reducir la huella de carbono en estos procesos no es igual en todos los continentes. Ahora mismo, creemos que Europa y Japón son las principales zonas donde las empresas consideran que esto es obligatorio. Por supuesto, todo el mundo quiere reducir el calor residual, pero no todo el mundo está dispuesto a pagar por estas nuevas tecnologías. Pero la demanda está creciendo. Por ejemplo, algunos de nuestros clientes ya han empezado a promocionar sus productos informando a sus clientes de la huella que dejan sus procesos y productos. Así que, para ellos, también se ha convertido en una cuestión de marketing y un argumento de venta: si tienen procesos más limpios, los clientes los tendrán en cuenta. Y, por supuesto, cada vez hay más exigencias de la Unión Europea para que la industria sea más ecológica. No puedo dar nombres (la confidencialidad es una obligación para nosotros), pero tenemos al menos cinco grandes clientes de la UE con operaciones en todo el mundo que piden mejoras en los equipos para que sean más limpios.
¿Y cómo pueden los hornos ayudar a reducir la huella de carbono total en una fábrica?
Yebra: Por ejemplo, en la fábrica de aluminio donde estamos probando el HPHE de ETEKINA, los hornos son uno de los equipos que más gas natural consumen. Por lo tanto, si se consigue reducir este consumo fabricando hornos más ecológicos, se estará reduciendo un gran porcentaje de las emisiones emitidas por toda la planta.
¿Cómo ha sido la experiencia de participar en un proyecto de Horizonte 2020 y en qué otros proyectos de investigación están trabajando actualmente?
Yebra: Este es nuestro segundo proyecto de Horizonte 2020, y diría que ha sido más desafiante porque, en el anterior, estábamos trabajando con un horno en un "entorno de laboratorio" (fuera de la línea de producción), mientras que ahora estamos mejorando un horno existente que está actualmente activo en una instalación industrial. Así que tenemos que trabajar en el proyecto en paralelo con las operaciones de la planta. Aparte de Horizonte 2020, estamos participando activamente en la investigación con el Ministerio de Industria español y el Centro para el Desarrollo Tecnológico Industrial (CDTI), así como en proyectos locales con el Gobierno del País Vasco, e instituciones de Vizcaya, ya que tenemos nuestra sede en esta región. Por lo tanto, diría que participamos en 10-12 proyectos en este momento.
Algunos de ellos tienen el objetivo de reducir las emisiones y el consumo de energía, mientras que otros están más relacionados con la seguridad, nuevos productos, nuevos objetivos productivos, y otros. Por ejemplo, estamos aplicando tecnologías robóticas a procesos que actualmente son realizados por personas y en los que existe un factor de riesgo para el empleado. También estamos estudiando la electrificación de los hornos de gas existentes. Históricamente, en Europa, la mayoría de los hornos que requieren un determinado nivel de temperatura se construían para funcionar con gas natural debido a su coste frente al de la electricidad. En otros países/continentes, donde la electricidad era más barata, o donde los recursos naturales locales lo hacían posible, se apostó por los equipos eléctricos. En Europa, los hornos de gas natural son los modelos más comunes que se encuentran en las plantas.
¿Cree que esto va a cambiar en un futuro próximo?
Yebra: Sí, creo que sí. Uno de los proyectos de investigación y desarrollo en los que participamos es en colaboración con una empresa eléctrica. Intentamos convertir los hornos de gas natural existentes en hornos eléctricos. Esto no siempre puede hacerse con la tecnología actual, pero también estamos trabajando en ello. Y si obtuviéramos electricidad a partir de recursos naturales, la huella sería mucho menor.
¿Cuáles son los retos de la producción de hornos energéticamente eficientes?
Yebra: Cuando un quemador está encendido, siempre va a liberar emisiones. El volumen puede ser menor o mayor, pero siempre estarán ahí. Los fabricantes de quemadores intentan mejorar eso, y nosotros también lo hacemos integrando los últimos avances, y teniendo un control técnico de todo el horno. Los quemadores tienden a estar encendidos todo el tiempo cuando el sistema demanda calor, así que en el proyecto ETEKINA estamos aprovechando para apagarlos y, por tanto, reducir el consumo. Si la HPHE nos permite alcanzar las temperaturas que necesitan los hornos con el calor de los humos procedentes de la primera cámara, no necesitaríamos utilizar quemadores en la segunda, por lo que estos hornos emitirán menos emisiones, reduciendo su huella de carbono de forma significativa.
Autor: Stefania Gozzer