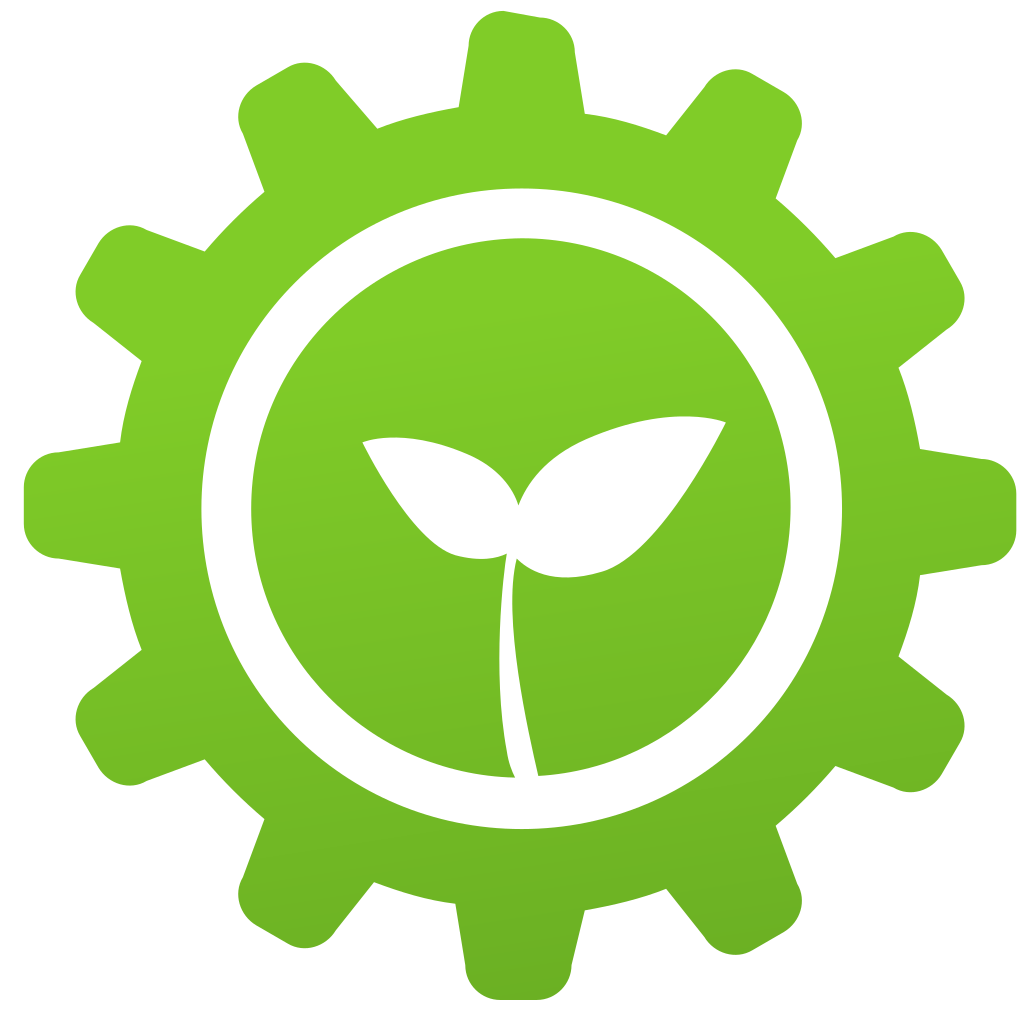
HPHE and greener furnaces: a combo that can make emissions plunge in the aluminium industry
Summary
Insertec is a leading manufacturer of industrial furnaces based in the Spanish province of Biscay. It is a crucial partner in one of the three case studies where ETEKINA is testing a new range of heat pipe heat exchangers. The combination of HPHE and adjustments in furnaces to increase their energy efficiency will help the aluminium industry improve its carbon footprint around the world. The demand to reduce the carbon footprint in these processes is not the same in every single continent. There are increasing requirements from the European Union to make the industry greener. And, of course, there are at least
at least five large EU customers with worldwide operations asking for improvements in equipment to make it cleaner. And how can furnaces help reduce the total carbon footprint. And how can the industry reduce emissions in a factory reduce thetotal carbon footprint? And it has become a marketing issue and sales argument: If you are able to reduce this. to make it greener furnaces.
Open full article
HPHE and greener furnaces: a combo that can make emissions plunge in the aluminium industry
Furnaces can account for more than 70% of energy consumption in plants dedicated to secondary aluminium production, releasing 25%-35% of the heat they generate. This is why Insertec, a leading manufacturer of industrial furnaces based in the Spanish province of Biscay, has been a crucial partner in one of the three case studies where the European Union funded project ETEKINA is testing a new range of heat pipe heat exchangers (HPHE). The combination of HPHE and adjustments Insertec is making in furnaces to increase their energy efficiency will help the aluminium industry improve its carbon footprint around the world.
The company’s Corporate Key Accounts Manager, Ignacio Yebra, explains in this interview Insertec’s role in ETEKINA.
Yebra: Our role in the project consists of adapting the system at Fagor Ederlan, one of our partners in the ETEKINA project, to integrate HPHE in an existing furnace that was built about 10 years ago by Insertec. We are the designers and manufacturers, so we know it better than anyone. Right now, we are in the phase where the system, all the tubes and control loops, has been installed in the plant’s furnace and we are making sure that everything is in place before we begin the actual trials.
The ETEKINA project aims to recover up to 70% of the waste heat stream in energy intensive industries such as steel, aluminium and ceramics. Some of these sectors, especially aluminium, aren't new to Insertec, but what about the heat recovery component? Is heat reutilisation something you had worked with before?
Yebra: We try to be as ecological as possible in our designs, making progress with every product by improving the burner itself and its integration into our furnaces to reduce energy consumption, that is a must for us. We also try to redirect some of the exhaust fumes onto other processes. However, what we are doing here now with HPHE is completely new.
What changes are HPHE bringing to your industry?
Yebra: At the moment, fumes go to one baghouse system and the atmosphere, which means all this heat is lost. With HPHE we recover all these hot fumes and use them in the next process, which happens in the same furnace. It has two main chambers, and the temperature can reach 500 °C in the first one, where solution heat treatment happens. Then the metal is quenched before going into the second chamber, where ageing occurs at about 200 °C. Both chambers need heat and, with HPHE, we will be using the heat from the first unit to heat the second one instead of generating it with burners. Therefore, we will avoid, or at least decrease substantially, natural gas consumption in that second area of the furnace.
Which are the challenges? The first is that the pieces we treat in this type of furnaces are security pieces, so the temperature must be very controlled. We are talking about plus-minus 5 °C throughout the whole process. We cannot get out of this range because we would have low quality pieces that cannot be used for security purposes. Hence by integrating HPHE we are adding another external factor to control, so we need to recover all this energy while controlling the process and the requirements of the plant.
Reducing carbon footprint has become a priority for many firms. As a supplier of industrial heating equipment, which traditionally releases a big amount of emissions into the atmosphere, how has your technology in furnaces for the steel and aluminium industry evolved to meet these needs?
Yebra: The demand to reduce the carbon footprint in these processes is not the same in every single continent. Right now, we feel that Europe and Japan are the main areas where companies feel this has become compulsory. Of course, everybody wants to decrease waste heat, but not everybody is willing to pay for these new technologies. But the demand is growing. For example, some of our customers have already started to promote their products by informing their clients of the footprint left by their processes and products. So, for them, it has also become a marketing issue and a sales argument: if they have cleaner processes, customers will consider them. And, of course, there are increasing requirements from the European Union to make the industry greener. I cannot provide names (confidentiality is a must for us), but we have at least five large EU customers with worldwide operations asking for improvements in equipment to make it cleaner.
And how can furnaces help reduce the total carbon footprint in a factory?
Yebra: For instance, in the aluminium factory where we are testing ETEKINA’s HPHE, furnaces are one of the most natural gas consuming pieces of equipment. So if you are able to reduce this consumption by making greener furnaces, you will be reducing a great percentage of emissions released by the whole plant.
What has the experience of participating in a Horizon 2020 project been like, and what other research projects are you working on at the moment?
Yebra: This is our second Horizon 2020 project, and I would say it has been more challenging because, in the previous one, we were working with a furnace in a “laboratory environment” (out of the production line), while now we are improving an existing furnace that is currently active in an industrial facility. So we have to work on the project in parallel with the plant’s operations. Apart from Horizon 2020, we are actively engaging in research with the Spanish Ministry of Industry and the Centre for the Development of Industrial Technology (CDTI), as well as in local projects with the government of the Basque Country, and institutions in Biscay, since we are based in this region. So I would say we are taking part in 10-12 projects at the moment.
Some of them have the goal of reducing emissions and energy consumption while others are more related to safety, new products, new productive goals, and others. For example, we are applying robotic technologies to processes that are currently being performed by people and where there is a risk factor for the employee. We are also exploring the electrification of existing gas furnaces. Historically in Europe, most furnaces that require a certain level of temperature were built to run on natural gas because of its cost versus electricity’s. In other countries/continents, where electricity was cheaper, or where local natural resources made that possible, the focus was put on electrical equipment. In Europe, natural gas furnaces are the most common models found in plants.
Do you think this is going to change in the near future?
Yebra: Yes, I think so. One of the research and development projects we are involved in is in partnership with an electrical company. We are trying to convert existing natural gas furnaces into electrical furnaces. This cannot always be done with the current technology, but we are also working on this. And if we were to obtain electricity from natural resources, the footprint would be much lower.
What are the challenges of producing energy efficient furnaces?
Yebra: When a burner is on, you will always release emissions. The volume can be lower or higher, but they will always be there. Burner manufacturers are trying to improve that, and we are also doing it by integrating the latest developments, and by having technical control of the whole furnace. Burners tend to be on all the time when heat is demanded by the system, so in the ETEKINA project, we are making the most to switch them off and therefore, reduce the consumption. If HPHE let us reach the temperatures needed by furnaces with heat from fumes stemming from the first chamber, we wouldn’t need to use burners in the second one, so these furnaces will release less emissions, reducing their carbon footprint significantly.
Author: Stefania Gozzer