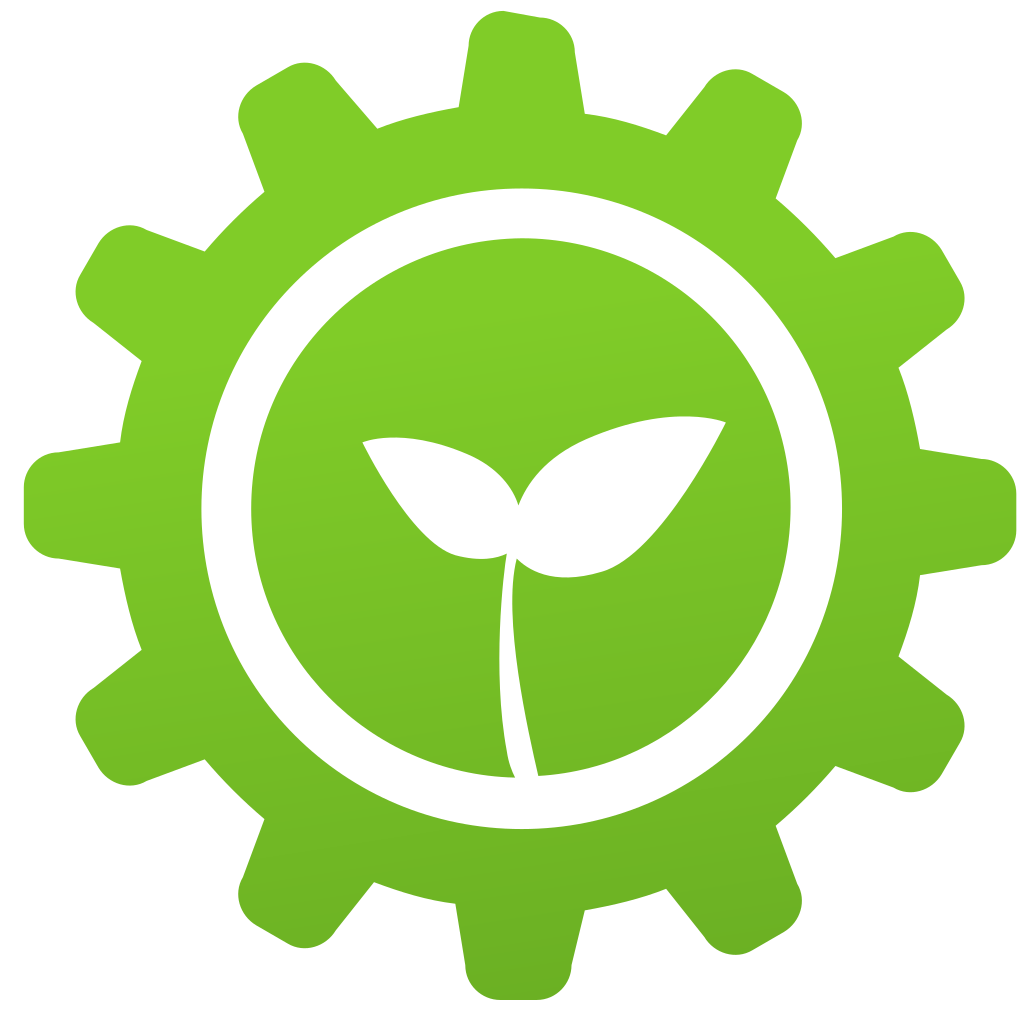
The Unprecedented Race: How AI is Reshaping Our Digital and Physical Worlds
The paper reveals that by 2030, $7 trillion investment will be needed to support data centers for the rise in AI processing demand. McKinsey research predicts $5.2 trillion of this will be for AI-data centers, with $1.5 trillion for traditional IT applications. The investment will primarily support the technology developers, power generation, and construction elements of these facilities. AI data centers require significantly more energy and cooling due to higher power densities and heat generation than traditional centers. This demand is driving energy consumption rates higher and necessitates advanced cooling solutions like liquid cooling. The semiconductor supply chain is under pressure from the high demand for AI components such as HBM, GPUs, and SSDs, leading to resource shortages and long lead times. Geopolitical factors, such as U.S. tariffs, could exacerbate these challenges, raising costs and adding complexity. In response, procurement strategies must evolve to ensure longer-term planning and supply chain resilience. AI and ML-based demand forecasting tools are vital for managing the uncertainty in demand and supply, offering potential to increase accuracy and automate decisions previously hindered by legacy systems. These tools enable better inventory planning, and have proven beneficial in cases like a global fashion retailer seeing revenue and margin improvements. In conclusion, the AI revolution is prompting massive investments, creating opportunities and extraordinary energy and infrastructure challenges. Addressing these will require innovation in hardware efficiency, renewable energy, and smart grid technologies, alongside advanced demand forecasting and planning. The capacity to anticipate compute power demand is crucial for stakeholders across the AI value chain.
Read Full articleConnecting the dots of Energy Efficiency Directive with sustainable finance reporting. The full potential unlocked.
The European Commission issued guidelines to aid EU member states in adopting the Energy Efficiency Directive by October 2025. Recommendation 2024/2002 promotes an integrated approach to energy audits, management systems, and sustainability reporting, supporting compliance with broader EU directives.
Read Full articleSpotlight on EU funded project – Unlocking SME potential: Financing energy efficiency for a sustainable future
The paper emphasizes the importance of energy efficiency in European SMEs, which are crucial to the continent's economy and competitiveness. The EU-funded DEESME 2050 project highlights the potential benefits of improving energy performance in the furniture industry. Investments and policy implementation must accelerate to meet the EU's 2030 climate goals, and new initiatives like EEEFC aim to support this transition. Financial intermediaries are identified as vital for SMEs to access funds, leveraging experiences from organizations like EEIP and state-owned banks to facilitate this process.
Read Full articleHow Global Energy Investment Transformed from 2019 to 2025
From 2019 to 2025, global energy investment shifted dramatically towards clean energy, with investments doubling and surpassing fossil fuels. Solar power, driven by cost declines and technological advances, became the largest investment segment. However, while investment in renewables aligned with climate goals, grid investments lagged, creating bottlenecks. Surprisingly, AI data centers increased demand for reliable baseload power, reviving interest in nuclear and gas. Distributed solar grew in emerging markets independently of policy, reshaping economic dynamics, yet clean energy deployment remained unequal globally.
Read Full article⚙ Business Practices
ORC-systems are helping to create a sustainable energy future
Organic Rankine Cycle (ORC) technology is being used in Sweden to transform waste heat into renewable electricity. The high efficiency and low maintenance way to produce sustainable electricity is being adopted by district heating systems around the world. Read how Ronneby.
Read Full Business PracticeRank Organic Rankine Cycle Technology with applications in Heat Recovery solution
ORC RANK has worked with SWEP to implement a heat recovery solution for electricity power generation. The activation range for the low-temperature equipment starts at just 85 °C. SWEPs heat exchangers are installed as economizers,.
Read Full Business Practice