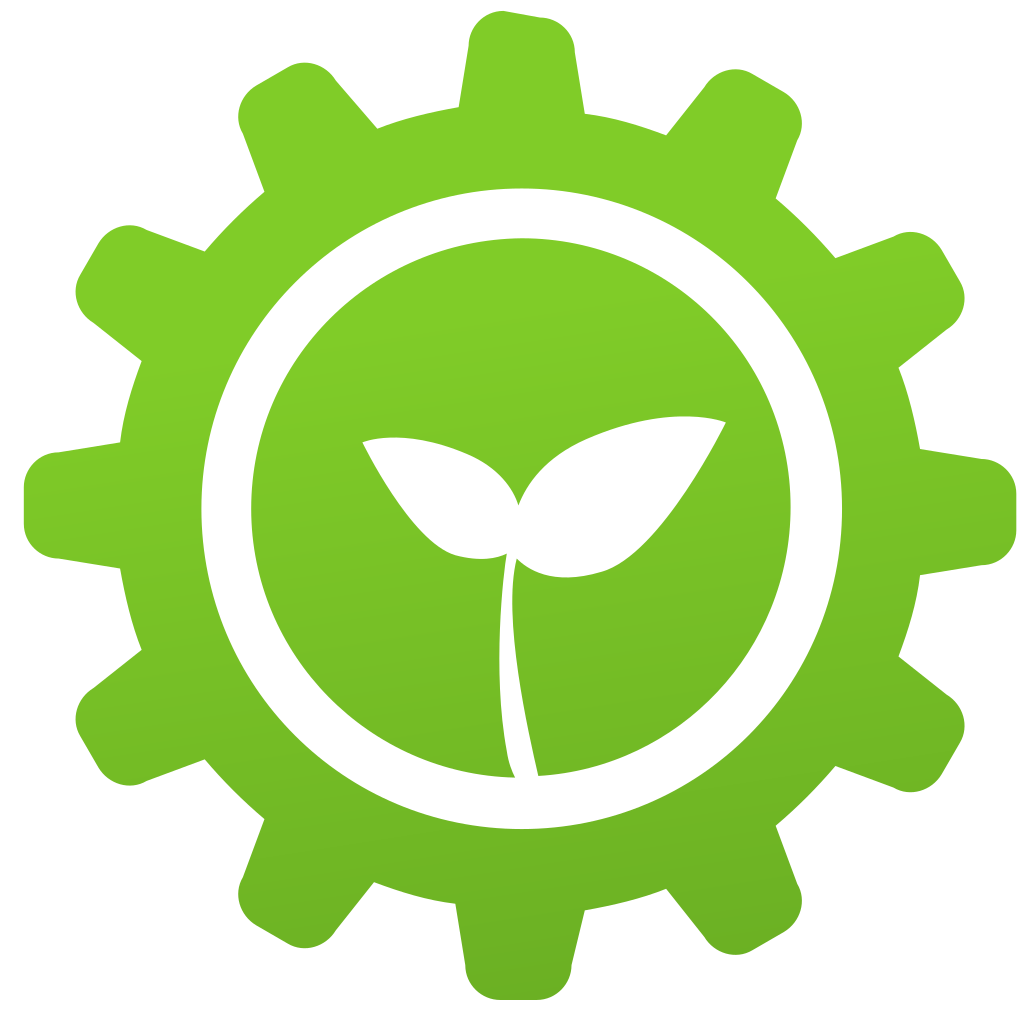
Energy Efficiency
The BOGE continuous improvement programme (CIP) is already a reality today. It reduces the loss of efficiency in a compressor due to wear and tear in operation. This can only be achieved through regular maintenance carried out by specialists. In a standardised process, there is always the question of whether the components used by the customer can be improved by developments that have already occurred. With the use of innovative data glasses, conversions can be carried out on-site by staff without special training or even by customers employees. The support comes from video instructions or relevant documents on a display built into the glasses. After successful commissioning of the now optimised compressed air station there is a detailed analysis of the actual energy savings for the customer, for: the installation of the software or hardware updates is free of charge for the user. Only the actual measured savings are shared by the user, for. the customer. only the service-free of charge.
Read Full articleAluminum Industry: 10 Emerging Technologies for Energy-efficiency and GHG Emissions Reduction
Aluminum production accounts for about 1% of global GHG emissions. Annual world aluminum demand is expected to increase two- to three-fold by 2050. The bulk of growth in consumption of aluminum will take place in China, India, the Middle East.
Read Full articleOur Applications Laboratory – The Gold Standard
Our Applications Laboratory is where we solve our customers most challenging heating applications. Dr. Girish Dahake, Sr. Vice President of Global Applications, leads a worldwide team of elite engineers. We have locations in the United States, United Kingdom and The Netherlands.
Read Full Business PracticeThe technical potential of large and industrial heat pumps
Heat pumps are considered large if they exceed capacities of 100kW. They can easily reach the one to several megawatt range with the largest units providing 35MW in a single machine. Currently available heat pump technology can provide heat up to 100°.
Read Full articleJohn Deere - variable peak load compressor
The John Deere factory in Mannheim, Germany, runs turbo compressors. If you want flexibility, you have to run them idle from time to time. But that is not energy-efficient, says Helmut Rembert, Senior Facilities Engineer.
Read Full Business PracticeDimaro wastewater plant - magnetic screw compressor
ROBOX energy helps a regional wastewater treatment plant achieve maximum effciency and excellent energy savings. The Dimaro plant presents an unusual challenge. While all other treatment plants in the area feature canonical 4.5m-deep oxidation tanks, the Dimaro.
Read Full Business PracticeBakery UK - production air with heat recovery
CompAir is on target to achieve annual energy savings in the region of £188,000. A payback on investment in less than two years is expected. CompAir installed fixed-speed L110s and regulated-speed compressor three months ago.
Read Full Business PracticePlastics: Motan - speed controlled vacuum generators
motan’s METRO G and GRAVICOLOR product lines offer a prime example of how process flow digitalization is improving material flow and productivity across the plastics industry. Flexible, intelligent conveying systems with speed-controlled vacuum.
Read Full Business PracticeGKD - Gebr Kufferath AG - compressed air from the roof
GKD is the world’s leading technical weaver. A compressor station on the factory roof was an innovative solution to the growing demand in production for compressed air. Kufferath AG range from microfilters for inkjet printers to automotive.
Read Full Business PracticeBeverages: Frueh Koelsch - oil free compressed air
The brewery always record the compressed air energy consumption and the volume flow generated. This gives us a precise overview of the. compressional air costs and enables us to carry out targeted optimisation measures. brewery’s decision to improve its compressed.
Read Full Business Practice