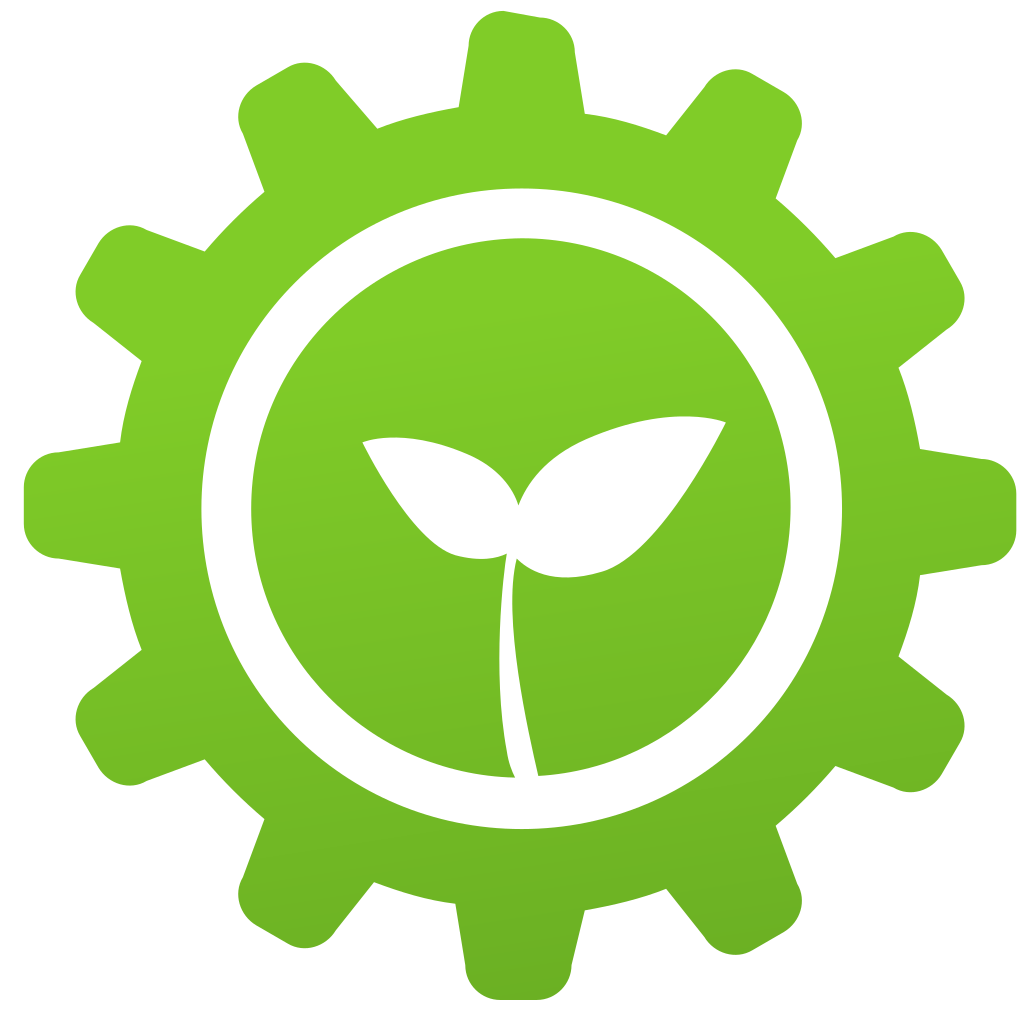
Sistemas pequeños, grandes beneficios
Resumen
El aumento de los precios del gas y de los costes del carbono está impulsando la demanda de recuperación de calor residual. ETEKINA ha diseñado tres intercambiadores de calor residual de tubo de calor. Han instalado más de un megavatio de potencia. Las unidades a escala de laboratorio son altamente escalables y serán fundamentales para el desarrollo futuro de más instalaciones de recuperación de calor. Además, pueden utilizarse para garantizar que el sistema final no afecte a los procesos de fabricación existentes en una instalación. Estas unidades proporcionan una visión realmente importante del funcionamiento de un sistema y su capacidad de control. Además, los ingenieros observaron que se creaban grandes cantidades de agua condensada que, según ellos, podían recuperarse para reducir aún más el consumo de energía y aumentar la eficiencia energética.
Abrir artículo completo
Sistemas pequeños, grandes beneficios
Los intercambiadores de calor diseñados por los socios de ETEKINA están dando forma a los sistemas de recuperación de calor residual del futuro.
A principios de febrero de este año, el coste del carbono alcanzó máximos históricos, con cifras de una tonelada de emisiones de dióxido de carbono que rozaban los 95 euros. Desde entonces, la multa por contaminación fijada por el Sistema de Comercio de Derechos de Emisión de la Unión Europea ha disminuido, pero los costes del carbono siguen siendo decenas de euros más altos que los anteriores, en un momento en el que los precios del gas natural también son desorbitados.
Las consecuencias para los proyectos de recuperación de calor residual, como ETEKINA, son profundas. Como destaca Mark Boocock, director general de Econotherm, en el Reino Unido: "El aumento de los precios del gas y el incremento de los costes del carbono están impulsando significativamente la demanda de recuperación de calor residual, en todo el mundo".
"Los proyectos energéticos que en el pasado tenían dificultades para ser aprobados, ahora se están llevando a cabo con gran éxito, y muchas empresas están prestando más atención a la gestión medioambiental", añade. "Hemos visto que muchas empresas de todo el mundo han implantado la recuperación de calor residual en las instalaciones existentes, al tiempo que la han impuesto en las nuevas; es un gran momento para proyectos como ETEKINA".
Boocock ha participado en ETEKINA desde el principio, colaborando estrechamente con el coordinador científico del proyecto, el profesor Hussam Jouhara, de la Universidad Brunel de Londres. Jouhara dirigió el diseño de los tres sistemas de recuperación de calor residual con tubos de calor, y los colegas de Boocock y Econotherm fabricaron e instalaron los sistemas en la línea de producción de aleaciones de aluminio de Fagor Ederlan en España, en la acería SIJ Metal Ravne en Eslovenia y en la planta de producción de cerámica Atlas Concorde en Italia.
Tanto Jouhara como Boocock están encantados con los resultados del proyecto. El objetivo inicial de ETEKINA era recuperar el 40% del calor residual de los flujos de escape en cada instalación; cuatro años después, todos los centros han superado este objetivo. "Con los tres sistemas de tubos de calor, hemos instalado más de un megavatio de potencia", destaca Jouhara. "Tras nuestro éxito, ahora estamos cediendo todo a Econotherm, que podrá replicar estos sistemas en todo el mundo".
Acertar con las unidades a escala de laboratorio
Una parte fundamental del proyecto ETEKINA consistió en desarrollar en Brunel tres unidades de intercambiadores de calor de tubos de calor a escala de laboratorio, para validar los modelos de HPHE y también para que sirvieran de banco de pruebas para las unidades a escala real que se instalarían en los tres emplazamientos de España, Eslovenia e Italia. Según Jouhara, él y sus colegas idearon modelos térmicos generales para los intercambiadores de calor, al tiempo que realizaban una modelización adicional para optimizar los complejos diseños de las unidades. Estos modelos se probaron en las unidades a escala de laboratorio.
Por ejemplo, se utilizó la dinámica de fluidos computacional para modelar el flujo de gases de escape en la planta de producción de cerámica de Atlas Concorde, en Italia, y asegurarse de que cualquier partícula pesada permaneciera suspendida en el gas a medida que fluye por el sistema. "Si el flujo de gas se estancaba en el interior del intercambiador de calor, estas partículas pesadas podían depositarse, acumularse y acabar bloqueando el sistema", explica Jouhara. "Así que desarrollamos algunos diseños innovadores [para evitar la deposición de partículas] y los probamos en el sistema a escala de laboratorio".
Durante sus primeros modelos y pruebas, los ingenieros también se dieron cuenta de que, aunque estas partículas permanecieran suspendidas durante el flujo de gas, seguirían adhiriéndose a las paredes del tubo cuando las temperaturas de los gases de escape descendieran por debajo de un determinado nivel. Por ello, añadieron al sistema final puertas de inspección de fácil acceso para poder retirar las partículas durante el mantenimiento periódico.
"Pudimos validar este diseño [con las puertas] in situ en Atlas Concorde, lo que fue increíble", dice Jouhara. "Las unidades a escala de laboratorio garantizaron que se detectara cualquier contratiempo inicial".
Tanto Jouhara como Boocock destacan que las unidades a escala de laboratorio son altamente escalables y serán fundamentales para el desarrollo futuro de más instalaciones de recuperación de calor en todo el mundo. Además, pueden utilizarse para garantizar que el sistema final no afecte a los procesos de fabricación existentes en una instalación.
"La implantación de un sistema de recuperación de calor residual convencional, o sin tuberías de calor, puede aportar muchas ventajas, pero siempre existe el riesgo de que interfiera en la fabricación: cualquier ganancia se perderá rápidamente si un fallo del intercambiador de calor interrumpe la producción", afirma Boocock. "Pero si nos fijamos en nuestras tres instalaciones, éstas son invisibles para los procesos de producción, pero han tenido un gran impacto en el consumo de energía y la eficiencia".
Más formas de utilizar el calor residual
De cara al futuro, las unidades a escala de laboratorio serán fundamentales para el diseño de futuros sistemas HPHE. Como señala Jouhara: "[Estas unidades] pueden proporcionarnos una visión realmente importante sobre el funcionamiento de un sistema y su capacidad de control".
Y, afortunadamente, Jouhara y Boocock ya están aplicando estos conocimientos, y las numerosas lecciones aprendidas durante ETEKINA, en otros proyectos. Durante su estancia en la planta de producción de cerámica de Atlas Concorde, los ingenieros observaron que se generaban grandes cantidades de agua de condensación que, según se dieron cuenta, podían recuperarse para reducir aún más el consumo de energía y aumentar la eficiencia energética. El proyecto financiado por la UE, Innovative Water recoverY Solutions through recycling of heat, materials and water across multiple sectors - iWAYS - se ha puesto en marcha desde entonces para desarrollar tecnologías basadas en tubos de calor para procesos industriales, con el fin de recuperar el agua y el calor de los flujos de escape.
"Considero que ETEKINA es el proyecto matriz de iWAYS, y ahora estamos impulsando nuestras tecnologías para recuperar el calor latente y reciclar el agua de los flujos de escape en Atlas Concorde y otras instalaciones", afirma Jouhara. "Como ven, nuestra historia de éxito no se detiene con los productos que desarrollamos en ETEKINA: ahora los estamos llevando al siguiente nivel y aportaremos un cambio drástico a los sistemas de recuperación de calor residual del futuro".