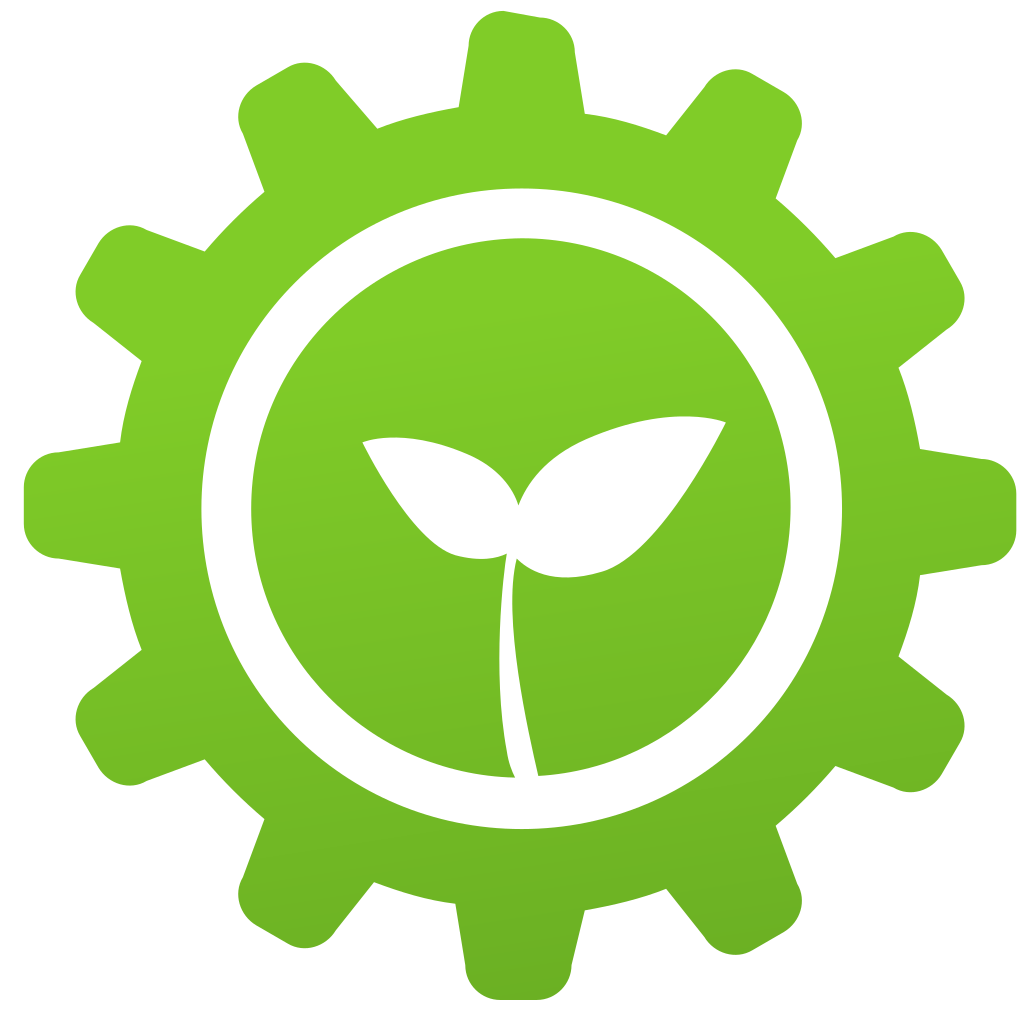
Piccoli sistemi, grandi benefici
Sommario
L'aumento dei prezzi del gas e l'aumento dei costi del carbonio stanno spingendo la domanda per il recupero del calore residuo. ETEKINA ha progettato tre scambiatori di calore a tubi di calore. Hanno installato più di un megawatt di potenza. Le unità su scala di laboratorio sono altamente scalabili e saranno determinanti per lo sviluppo futuro di altri impianti di recupero del calore. E possono essere usate per aiutare a garantire che il sistema finale non abbia un impatto sui processi di produzione esistenti di una struttura. Queste unità forniscono una visione davvero importante del funzionamento di un sistema e della sua controllabilità. E, fortunatamente, gli ingegneri hanno notato che si creano grandi quantità di acqua di condensa che possono essere recuperate per ridurre ulteriormente il consumo energetico e aumentare l'efficienza energetica.
Aprire articolo completo
Piccoli sistemi, grandi benefici
Come gli scambiatori di calore a tubi di calore progettati dai partner di ETEKINA stanno dando forma ai sistemi di recupero del calore residuo del futuro.
All'inizio di febbraio di quest'anno, il costo del carbonio ha raggiunto livelli record con cifre per una tonnellata di emissioni di anidride carbonica che sfiorano i 95 euro. Da allora, la sanzione per l'inquinamento stabilita dai sistemi di scambio delle emissioni dell'Unione europea è diminuita, ma i costi del carbonio rimangono decine di euro più alti dei precedenti prezzi di scambio, in un momento in cui anche i prezzi del gas naturale sono incredibilmente alti.
L'implicazione per i progetti di recupero del calore dei rifiuti, come ETEKINA, è profonda. Come sottolinea Mark Boocock, amministratore delegato di Econotherm, Regno Unito: "L'aumento dei prezzi del gas e i costi più alti del carbonio stanno spingendo significativamente la domanda di recupero del calore di scarto, in tutto il mondo".
"I progetti energetici che in passato facevano fatica ad essere firmati, ora stanno volando e stiamo anche vedendo una maggiore attenzione alla governance ambientale in molte aziende", aggiunge. "Abbiamo visto molte aziende globali implementare il recupero del calore di scarto negli impianti esistenti e allo stesso tempo renderlo obbligatorio nei nuovi impianti - questo è un grande momento per progetti come ETEKINA".
Boocock è stato coinvolto in ETEKINA fin dall'inizio, lavorando a stretto contatto con il coordinatore scientifico del progetto, il professor Hussam Jouhara, della Brunel University di Londra. Jouhara ha guidato la progettazione dei tre sistemi di recupero del calore di scarto del progetto, con Boocock e i colleghi di Econotherm che hanno prodotto e installato i sistemi presso la linea di produzione di leghe di alluminio di Fagor Ederlan in Spagna, l'acciaieria SIJ Metal Ravne in Slovenia e l'impianto di produzione di ceramica Atlas Concorde in Italia.
Sia Jouhara che Boocock sono entusiasti dei risultati del progetto. L'obiettivo iniziale di ETEKINA era quello di recuperare il 40% del calore disperso nei flussi di scarico di ogni impianto - dopo quattro anni, tutti i siti hanno superato questo obiettivo. "Con tutti e tre i sistemi di tubi di calore, abbiamo installato più di un megawatt di potenza", sottolinea Jouhara. "In seguito al nostro successo, ora stiamo passando la mano a Econotherm, che sarà in grado di replicare questi sistemi in tutto il mondo".
Ottenere il giusto risultato con unità su scala di laboratorio
Una parte critica del progetto ETEKINA era lo sviluppo di tre unità di scambiatori di calore a tubi di calore (HPHE) su scala di laboratorio a Brunel, per convalidare i modelli HPHE e anche per servire da banco di prova per le unità in scala reale che sarebbero state installate nei tre siti in Spagna, Slovenia e Italia. Secondo Jouhara, lui e i colleghi hanno ideato dei modelli termici generali per gli scambiatori di calore e hanno anche effettuato una modellazione aggiuntiva per ottimizzare i complessi progetti delle unità. Questi modelli sono stati testati sulle unità in scala di laboratorio.
Per esempio, la fluidodinamica computazionale è stata usata per modellare il flusso dei gas di scarico nell'impianto di produzione della ceramica Atlas Concorde in Italia, e garantire che qualsiasi particella pesante rimanesse sospesa nel gas mentre scorreva attraverso il sistema. "Se il flusso di gas dovesse ristagnare all'interno dello scambiatore di calore, queste particelle pesanti potrebbero depositarsi, accumularsi e infine bloccare il sistema", spiega Jouhara. "Così abbiamo sviluppato alcuni design innovativi [per evitare il deposito di particelle] e li abbiamo testati nel sistema su scala di laboratorio".
Durante i loro primi modelli e test, gli ingegneri si sono anche resi conto che anche se queste particelle rimanevano sospese durante il flusso di gas, si sarebbero comunque attaccate alle pareti del tubo quando le temperature di scarico scendevano sotto un certo livello. Dato questo, hanno aggiunto porte d'ispezione di facile accesso al sistema finale in modo che le particelle potessero essere rimosse durante la manutenzione regolare.
"Siamo stati in grado di convalidare questo progetto [con le porte] in situ presso Atlas Concorde, il che è stato incredibile", dice Jouhara. "Le unità in scala di laboratorio hanno assicurato che qualsiasi intoppo iniziale fosse stato rilevato".
Sia Jouhara che Boocock sottolineano anche come le unità su scala di laboratorio siano altamente scalabili e saranno strumentali al futuro sviluppo di più impianti di recupero del calore in tutto il mondo. Per di più, possono essere utilizzate per garantire che il sistema finale non abbia un impatto sui processi di produzione esistenti di una struttura.
"L'implementazione di un sistema di recupero di calore convenzionale, o non-heat pipe, può portare molti benefici, ma c'è sempre il rischio che possa interferire con la produzione - qualsiasi guadagno sarà rapidamente perso se un guasto allo scambiatore di calore interrompe la produzione", dice Boocock. "Ma se si guarda alle nostre tre installazioni - queste sono invisibili ai processi di produzione ma hanno avuto un enorme impatto sul consumo energetico e sull'efficienza".
Più modi con il calore di scarto
Guardando al futuro, le unità su scala di laboratorio saranno fondamentali per la progettazione di futuri sistemi HPHE. Come sottolinea Jouhara: "[Queste unità] possono fornirci una visione davvero importante del funzionamento di un sistema e della sua controllabilità".
E piacevolmente, Jouhara e Boocock stanno già implementando questa conoscenza, e le molte lezioni apprese durante ETEKINA, in altri progetti. Nell'impianto di produzione della ceramica Atlas Concorde, gli ingegneri hanno notato che si creavano grandi quantità di acqua di condensa che potevano essere recuperate per ridurre ulteriormente il consumo energetico e aumentare l'efficienza energetica. Il progetto finanziato dall'UE, Innovative Water recoverY Solutions through recycling of heat, materials and water across multiple sectors - iWAYS - è stato lanciato per sviluppare tecnologie basate su heat-pipe per processi industriali, per recuperare acqua e calore dai flussi di scarico.
"Vedo ETEKINA come il progetto madre di iWAYS, e ora stiamo spingendo le nostre tecnologie oltre per recuperare il calore latente e riciclare l'acqua dai flussi di scarico presso Atlas Concorde e altri impianti", dice Jouhara. "Quindi vedete, la nostra storia di successo non si ferma ai prodotti che abbiamo sviluppato in ETEKINA - ora li stiamo spingendo al livello successivo e porteranno un cambiamento drastico nei sistemi di recupero del calore residuo del futuro".