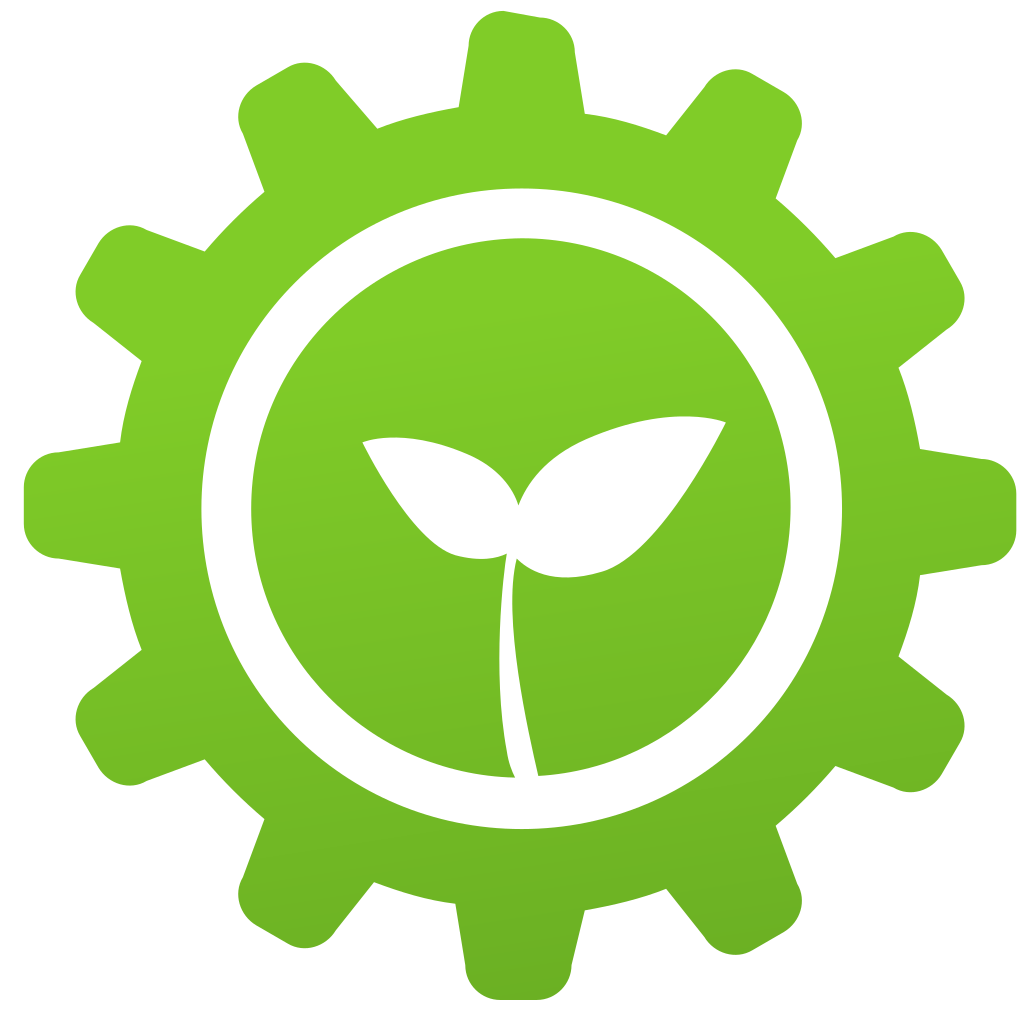
Alimentare l'efficienza: Rivoluzionare i sistemi di aria compressa per un futuro sostenibile
Sommario
I sistemi ad aria compressa (CAS) sono fondamentali per la produzione, ma sono ad alta intensità energetica e rappresentano il 10% dell'elettricità industriale. Offrono un potenziale risparmio energetico del 20-60%, che si traduce in una significativa riduzione dei costi e in benefici ambientali. Nonostante la loro convenienza, la maggior parte dei CAS è inefficiente: solo il 10-30% dell'aria prodotta viene effettivamente utilizzato. Il resto viene perso a causa di perdite, uso inappropriato e altre inefficienze.
I CAS sono costituiti da un lato di fornitura (compressori, serbatoi di stoccaggio, essiccatori, filtri) e da un lato di domanda (controlli di flusso e pressione, rete di distribuzione). L'ottimizzazione di ciascun componente può portare a notevoli risparmi energetici. Le perdite sono un problema importante, che spesso spreca il 20-40% della produzione d'aria, ma possono essere attenuate attraverso il rilevamento a ultrasuoni o i test con acqua e sapone. È importante anche il corretto dimensionamento del serbatoio di stoccaggio, con una capacità consigliata di 12-120 m³/m³/sec di aria erogata, per evitare inefficienze.
Inoltre, la temperatura di aspirazione influisce sul consumo energetico: ogni aumento di 3°C comporta un aumento dell'1% del consumo energetico. Pertanto, la posizione dei compressori può avere un impatto considerevole sull'efficienza. I miglioramenti del CAS non solo portano a risparmi energetici, ma aumentano anche l'affidabilità della produzione, riducono i costi di manutenzione, migliorano la qualità dei prodotti e riducono l'impronta di carbonio.
Un approccio sistematico all'efficienza del CAS prevede la conduzione di audit dell'aria, la correzione delle perdite, l'ottimizzazione della pressione del sistema, il dimensionamento corretto dei componenti, l'implementazione del recupero di calore e la manutenzione regolare. Il caso di studio evidenziato a Barranquilla, in Colombia, ha mostrato i benefici tangibili di tali misure, con un potenziale risparmio sul consumo energetico del 43,1% e un risparmio sui costi annuali di oltre 25 milioni di pesos colombiani. In generale, l'ottimizzazione del CAS è un modo fondamentale per le industrie di raggiungere la sostenibilità e migliorare l'efficienza dei costi.
Aprire articolo completo
Alimentare l'efficienza: Rivoluzionare i sistemi di aria compressa per un futuro sostenibile
Nella ricerca di pratiche industriali sostenibili, i sistemi di aria compressa (CAS) sono emersi come uno dei principali obiettivi per il miglioramento dell'efficienza energetica. Questi sistemi, vitali per molti processi produttivi, spesso consumano il 10% dell'elettricità industriale a livello mondiale. Tuttavia, con il giusto approccio, le aziende possono ridurre l'utilizzo di energia del 20-60%, ottenendo sostanziali risparmi sui costi e benefici ambientali.
Il consumatore nascosto di energia nella vostra fabbrica
L'aria compressa, spesso definita la "quarta utility" dopo l'elettricità, il gas naturale e l'acqua, è una fonte di energia onnipresente nella produzione. La sua popolarità deriva dalla versatilità, dalla pulizia e dalla sicurezza. Ma questa convenienza ha un costo: l'aria compressa è una delle forme di energia più costose in un impianto a causa di significative inefficienze.
La maggior parte degli impianti industriali utilizza efficacemente solo il 10-30% dell'aria compressa prodotta. Il resto viene perso a causa di perdite, cali di pressione, calore e uso improprio. Questa inefficienza si traduce in spreco di energia e spese inutili, rendendo il CAS un candidato privilegiato per le iniziative di risparmio energetico.
Anatomia di un sistema ad aria compressa
Per capire come ottimizzare questi sistemi, è fondamentale conoscerne i componenti. Un tipico CAS è costituito da due lati principali:
- Lato alimentazione: Comprende il compressore (che aumenta la pressione dell'aria), i serbatoi di stoccaggio (sia umidi che secchi), gli essiccatori e i filtri.
- Lato domanda: Comprende i controlli di flusso e di pressione e la rete di distribuzione che porta l'aria alle varie macchine e agli strumenti.
Ogni componente svolge un ruolo fondamentale nell'efficienza del sistema e l'ottimizzazione di ciascuno di essi può portare a significativi risparmi energetici.
Tappare le falle: Il frutto più facile del risparmio energetico
Le perdite sono l'arcinemesi di un CAS efficiente. In un sistema ben mantenuto, le perdite non dovrebbero rappresentare più del 5-10% della produzione di aria compressa. Tuttavia, in molti ambienti industriali, le perdite possono sprecare il 20-40% dell'aria prodotta e, in casi estremi, fino al 60%.
I punti di perdita più comuni sono i giunti, le connessioni e i gomiti delle tubazioni dell'aria compressa. L'identificazione e la riparazione di queste perdite può portare a un risparmio energetico immediato e sostanziale. Le aziende possono utilizzare tecniche come il rilevamento delle perdite a ultrasuoni o semplici test con acqua e sapone per individuare le perdite.
In un caso di studio, un impianto di produzione di vetro a Barranquilla, in Colombia, ha scoperto che le perdite erano responsabili del 33% del consumo di aria compressa. Riducendo questo dato a un accettabile 5%, l'azienda ha potuto risparmiare oltre 3.000 kWh al mese, che si traducono in un risparmio annuale di oltre 16 milioni di pesos colombiani.
Le dimensioni contano: L'importanza di uno stoccaggio adeguato
I serbatoi di stoccaggio svolgono un ruolo cruciale nell'efficienza CAS. Forniscono la capacità di evitare brevi cicli di avvio/arresto, condensano l'umidità dell'aria, coprono i picchi di pressione, mantengono la pressione del sistema e consentono un controllo più efficiente del sistema.
Gli esperti raccomandano una capacità di stoccaggio di 12-120 m³ per ogni metro cubo al secondo di aria erogata dal compressore a pieno carico. Tuttavia, molti sistemi sono sottodimensionati, con conseguenti inefficienze.
Nel nostro caso di studio, il serbatoio di stoccaggio del produttore di vetro era notevolmente sottodimensionato. Aumentando la capacità di stoccaggio per soddisfare le raccomandazioni del produttore, l'azienda avrebbe potuto risparmiare il 12% sul consumo energetico di aria compressa, pari a oltre 7 milioni di pesos colombiani all'anno.
Mantenere il freddo: L'impatto della temperatura di aspirazione
La temperatura dell'aria in ingresso al compressore ha un impatto significativo sull'efficienza. Per ogni aumento di 3°C della temperatura dell'aria in ingresso, il consumo energetico aumenta dell'1%. Molti compressori sono situati in aree calde dell'impianto, aspirando aria calda e riducendo l'efficienza.
Nel nostro caso di studio, il compressore era mal posizionato al secondo piano, sopra un forno e vicino a un motore elettrico caldo. La temperatura media di aspirazione era di 10°C sopra l'ambiente, con picchi di 15°C di differenza. Ricollocando il compressore per aspirare aria più fresca, l'azienda ha potuto risparmiare il 3,1% sul consumo di energia per l'aria compressa - circa 1,8 milioni di pesos colombiani all'anno.
Oltre l'energia: Gli effetti a catena dell'efficienza
Sebbene i risparmi energetici derivanti dall'ottimizzazione del CAS siano significativi, i vantaggi vanno ben oltre la riduzione delle bollette elettriche. Una maggiore efficienza può portare a:
- Aumento della produzione: Una fornitura di aria compressa più affidabile ed efficiente può aumentare la produttività e ridurre i tempi di inattività.
- Riduzione dei costi di manutenzione: Sistemi ben mantenuti, con meno perdite e un dimensionamento più appropriato, richiedono riparazioni e sostituzioni meno frequenti.
- Migliore qualità del prodotto: Una pressione e una qualità dell'aria costanti possono migliorare i processi di produzione, portando a prodotti finali migliori.
- Riduzione dell'impronta di carbonio: Un minor consumo energetico si traduce direttamente in una riduzione delle emissioni di CO2, aiutando le aziende a raggiungere gli obiettivi di sostenibilità.
La strada verso l'efficienza: Un approccio passo dopo passo
Il miglioramento dell'efficienza CAS non deve essere scoraggiante. Le aziende possono seguire questi passi:
- Condurre un audit dell'aria: Comprendere il sistema attuale, compresi i tassi di perdita, i requisiti di pressione e i modelli di utilizzo.
- Correggere le perdite: Questo è spesso il miglioramento più rapido ed economico.
- Ottimizzare la pressione del sistema: molti sistemi funzionano a pressioni più elevate del necessario. La riduzione della pressione può portare a un significativo risparmio energetico.
- Dimensionamento dei componenti: Assicuratevi che i compressori, i serbatoi di stoccaggio e le reti di distribuzione siano dimensionati in modo appropriato per le vostre esigenze.
- Implementare il recupero del calore: I compressori generano molto calore. Questo può essere catturato e utilizzato per il riscaldamento degli ambienti o per altri processi.
- Manutenzione regolare: Una manutenzione costante assicura che il sistema continui a funzionare al massimo dell'efficienza.
I sistemi di aria compressa rappresentano un'opportunità significativa di risparmio energetico nel settore industriale. Affrontando problemi come perdite, dimensionamenti errati e condizioni operative non ottimali, le aziende possono ridurre drasticamente il consumo energetico e i costi operativi.
Il caso di studio dell'azienda di Barranquilla ne dimostra il potenziale: implementando solo tre misure di efficienza, è stato possibile ridurre il consumo energetico di aria compressa del 43,1%, con un risparmio annuo di oltre 25 milioni di pesos colombiani.
Mentre le industrie di tutto il mondo si sforzano di raggiungere la sostenibilità e l'efficienza dei costi, l'ottimizzazione dei sistemi di aria compressa offre una chiara via d'uscita. È giunto il momento per le aziende di esaminare più da vicino questa utility spesso trascurata e di sbloccare il potenziale di significativi risparmi energetici e miglioramenti operativi.