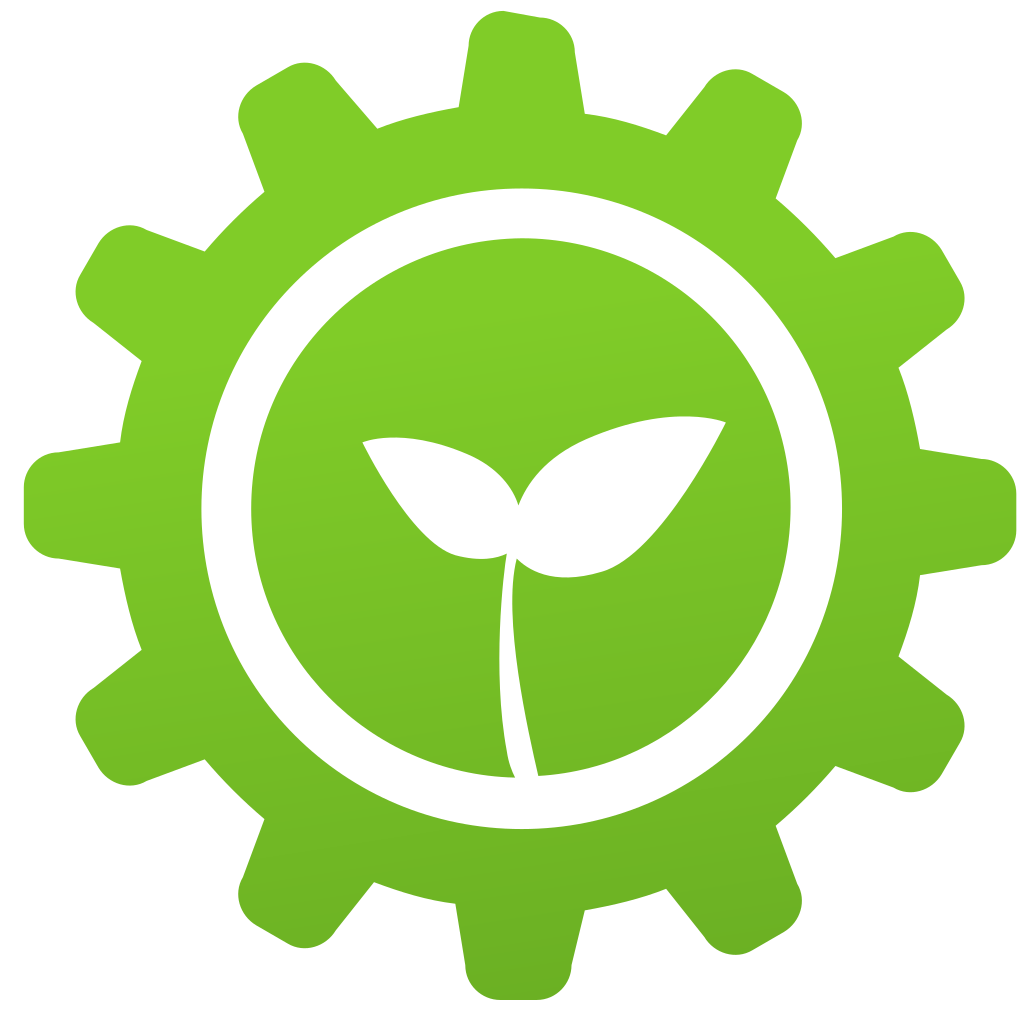
Kraftvolle Effizienz: Revolutionierung von Druckluftsystemen für eine nachhaltige Zukunft
Zusammenfassung
Druckluftsysteme (CAS) sind in der Fertigung von entscheidender Bedeutung, aber energieintensiv, denn sie verbrauchen 10 % des industriellen Stroms. Sie bieten ein Energieeinsparungspotenzial von 20-60 %, was zu erheblichen Kostensenkungen und Umweltvorteilen führt. Trotz ihrer Zweckmäßigkeit sind die meisten CAS ineffizient, da nur 10-30 % der erzeugten Luft effektiv genutzt werden. Der Rest geht durch Leckagen, unsachgemäße Nutzung und andere Ineffizienzen verloren.
CAS bestehen aus einer Versorgungsseite (Kompressoren, Lagertanks, Trockner, Filter) und einer Nachfrageseite (Durchfluss- und Druckregelung, Verteilungsnetz). Die Optimierung der einzelnen Komponenten kann zu erheblichen Energieeinsparungen führen. Leckagen sind ein großes Problem, durch die oft 20-40 % der Luftproduktion verloren gehen, können aber durch Ultraschalldetektion oder Seifenwassertests eingedämmt werden. Auch die richtige Dimensionierung der Lagertanks ist wichtig, wobei eine Kapazität von 12-120 m³/m³/sec der gelieferten Luft empfohlen wird, um Ineffizienzen zu vermeiden.
Darüber hinaus wirkt sich die Ansaugtemperatur auf den Energieverbrauch aus, wobei jede Erhöhung um 3 °C zu einem Anstieg des Energieverbrauchs um 1 % führt. Daher kann der Standort der Kompressoren einen erheblichen Einfluss auf die Effizienz haben. Verbesserungen bei CAS führen nicht nur zu Energieeinsparungen, sondern erhöhen auch die Produktionszuverlässigkeit, senken die Wartungskosten, verbessern die Produktqualität und verringern die CO2-Bilanz.
Ein systematischer Ansatz zur Steigerung der CAS-Effizienz umfasst die Durchführung von Luftprüfungen, die Behebung von Leckagen, die Optimierung des Systemdrucks, die richtige Dimensionierung der Komponenten, die Implementierung von Wärmerückgewinnung und regelmäßige Wartung. Die hervorgehobene Fallstudie in Barranquilla, Kolumbien, zeigte die greifbaren Vorteile solcher Maßnahmen mit potenziellen Energieeinsparungen von 43,1 % und jährlichen Kosteneinsparungen von über 25 Millionen kolumbianischen Pesos. Insgesamt ist die Optimierung von CAS eine wichtige Möglichkeit für die Industrie, Nachhaltigkeit zu erreichen und die Kosteneffizienz zu verbessern.
Kompletten Artikel anzeigen
Kraftvolle Effizienz: Revolutionierung von Druckluftsystemen für eine nachhaltige Zukunft
Auf der Suche nach nachhaltigen industriellen Verfahren haben sich Druckluftsysteme (CAS) als ein Hauptziel für Verbesserungen der Energieeffizienz herausgestellt. Diese Systeme, die für viele Fertigungsprozesse unverzichtbar sind, verbrauchen oft 10 % des industriellen Stroms weltweit. Mit dem richtigen Ansatz können Unternehmen jedoch ihren Energieverbrauch um 20 bis 60 % senken und so erhebliche Kosteneinsparungen und Umweltvorteile erzielen.
Der versteckte Energieverbraucher in Ihrer Fabrik
Druckluft wird oft als "vierte Energiequelle" nach Strom, Erdgas und Wasser bezeichnet, ist eine allgegenwärtige Energiequelle in der Fertigung. Ihre Beliebtheit rührt von ihrer Vielseitigkeit, Sauberkeit und Sicherheit her. Doch dieser Komfort hat seinen Preis: Druckluft ist aufgrund erheblicher Ineffizienzen eine der teuersten Energieformen in einer Anlage.
Die meisten Industrieanlagen nutzen nur 10-30 % der erzeugten Druckluft effektiv. Der Rest geht durch Lecks, Druckabfall, Wärme und Missbrauch verloren. Diese Ineffizienz führt zu Energieverschwendung und unnötigen Ausgaben, was CAS zu einem erstklassigen Kandidaten für Energiesparinitiativen macht.
Anatomie eines Druckluftsystems
Um zu verstehen, wie diese Systeme optimiert werden können, ist es wichtig, ihre Komponenten zu kennen. Ein typisches CAS besteht aus zwei Hauptseiten:
- Versorgungsseite: Dazu gehören der Kompressor (der den Luftdruck erhöht), Lagertanks (sowohl feucht als auch trocken), Trockner und Filter.
- Nachfrageseite: Dazu gehören die Durchfluss- und Druckregelung sowie das Verteilernetz, das die Luft an die verschiedenen Maschinen und Werkzeuge liefert.
Jede Komponente spielt eine wichtige Rolle für die Effizienz des Systems, und die Optimierung jeder einzelnen kann zu erheblichen Energieeinsparungen führen.
Die Lecks stopfen: Die tief hängenden Früchte der Energieeinsparung
Lecks sind die Erznemesis eines effizienten CAS. In einem gut gewarteten System sollten die Leckagen nicht mehr als 5-10 % der Drucklufterzeugung ausmachen. In vielen industriellen Umgebungen können Leckagen jedoch 20-40 % der erzeugten Luft verschwenden, in Extremfällen sogar bis zu 60 %.
Häufige Leckstellen sind Verbindungen, Anschlüsse und Krümmer in den Druckluftleitungen. Das Erkennen und Beheben dieser Lecks kann zu sofortigen und erheblichen Energieeinsparungen führen. Unternehmen können Techniken wie Ultraschall-Lecksuche oder einfache Seifen-Wasser-Tests einsetzen, um Lecks zu lokalisieren.
In einer Fallstudie stellte eine Glasfabrik in Barranquilla, Kolumbien, fest, dass 33 % des Druckluftverbrauchs auf Lecks zurückzuführen waren. Durch die Reduzierung dieses Anteils auf akzeptable 5 % konnte das Unternehmen mehr als 3.000 kWh pro Monat einsparen, was einer jährlichen Einsparung von über 16 Millionen kolumbianischen Pesos entspricht.
Auf die Größe kommt es an: Die Wichtigkeit einer ordnungsgemäßen Lagerung
Speichertanks spielen eine entscheidende Rolle bei der CAS-Effizienz. Sie bieten Kapazität, um kurze Start/Stopp-Zyklen zu vermeiden, Luftfeuchtigkeit zu kondensieren, Druckspitzen abzudecken, den Systemdruck aufrechtzuerhalten und eine effizientere Systemsteuerung zu ermöglichen.
Experten empfehlen eine Speicherkapazität von 12-120 m³ für jeden Kubikmeter pro Sekunde Luft, den der Kompressor bei Volllast liefert. Viele Systeme sind jedoch unterdimensioniert, was zu Ineffizienzen führt.
In unserer Fallstudie war der Lagertank des Glasherstellers deutlich unterdimensioniert. Durch eine Erhöhung der Speicherkapazität gemäß den Empfehlungen des Herstellers könnte das Unternehmen 12 % seines Energieverbrauchs für Druckluft einsparen - das entspricht über 7 Millionen kolumbianischen Pesos jährlich.
Einen kühlen Kopf bewahren: Der Einfluss der Ansaugtemperatur
Die Temperatur der in den Kompressor eintretenden Luft hat einen erheblichen Einfluss auf die Effizienz. Pro 3°C Anstieg der Ansauglufttemperatur steigt der Energieverbrauch um 1 %. Viele Kompressoren befinden sich in heißen Bereichen der Anlage und saugen warme Luft an, was die Effizienz verringert.
In unserer Fallstudie befand sich der Kompressor an einem ungünstigen Standort im zweiten Stock über einem Ofen und neben einem heißen Elektromotor. Die durchschnittliche Ansaugtemperatur lag 10 °C über der Umgebungstemperatur, mit Spitzenwerten von 15 °C Unterschied. Durch die Verlegung des Kompressors, um kühlere Luft anzusaugen, konnte das Unternehmen 3,1 % seines Energieverbrauchs für Druckluft einsparen - etwa 1,8 Millionen kolumbianische Pesos pro Jahr.
Mehr als Energie: Die Nebeneffekte der Effizienz
Die Energieeinsparungen durch die Optimierung von CAS sind zwar erheblich, aber die Vorteile gehen weit über niedrigere Stromrechnungen hinaus. Verbesserte Effizienz kann zu folgenden Effekten führen:
- Gesteigerte Produktion: Eine zuverlässigere und effizientere Druckluftversorgung kann die Produktivität steigern und Ausfallzeiten reduzieren.
- Geringere Wartungskosten: Gut gewartete Systeme mit weniger Leckagen und einer angemessenen Dimensionierung erfordern weniger häufige Reparaturen und Austauschmaßnahmen.
- Verbesserte Produktqualität: Ein gleichmäßiger Druck und eine gleichbleibende Qualität der Druckluft können die Fertigungsprozesse verbessern und zu besseren Endprodukten führen.
- Geringerer Kohlenstoff-Fußabdruck: Ein geringerer Energieverbrauch führt direkt zu geringeren CO2-Emissionen und hilft Unternehmen, ihre Nachhaltigkeitsziele zu erreichen.
Der Weg zur Effizienz: Ein Schritt-für-Schritt-Ansatz
Die Verbesserung der CAS-Effizienz muss nicht entmutigend sein. Unternehmen können diese Schritte befolgen:
- Führen Sie ein Air Audit durch: Verstehen Sie Ihr aktuelles System, einschließlich Leckraten, Druckanforderungen und Nutzungsmuster.
- Beheben Sie Lecks: Dies ist oft die schnellste und kostengünstigste Verbesserung.
- Optimieren Sie den Systemdruck: Viele Systeme arbeiten mit höherem Druck als nötig. Eine Druckreduzierung kann zu erheblichen Energieeinsparungen führen.
- Komponenten richtig dimensionieren: Stellen Sie sicher, dass Kompressoren, Lagertanks und Verteilernetze für Ihren Bedarf angemessen dimensioniert sind.
- Wärmerückgewinnung einsetzen: Kompressoren erzeugen eine Menge Wärme. Diese kann aufgefangen und für die Raumheizung oder andere Prozesse genutzt werden.
- Regelmäßige Wartung: Eine konsequente Wartung stellt sicher, dass Ihr System weiterhin mit höchster Effizienz arbeitet.
Druckluftsysteme bieten ein erhebliches Potenzial für Energieeinsparungen im Industriesektor. Durch die Behebung von Problemen wie Leckagen, falscher Dimensionierung und suboptimalen Betriebsbedingungen können Unternehmen ihren Energieverbrauch und ihre Betriebskosten drastisch senken.
Das Fallstudienunternehmen in Barranquilla zeigt das Potenzial - durch die Umsetzung von nur drei Effizienzmaßnahmen konnte es seinen Energieverbrauch für Druckluft um 43,1 % senken und damit jährlich über 25 Millionen kolumbianische Pesos einsparen.
Da die Industrie weltweit nach Nachhaltigkeit und Kosteneffizienz strebt, bietet die Optimierung von Druckluftsystemen einen klaren Weg nach vorne. Es ist an der Zeit, dass Unternehmen dieses oft übersehene Hilfsmittel genauer unter die Lupe nehmen und das Potenzial für erhebliche Energieeinsparungen und betriebliche Verbesserungen erschließen.