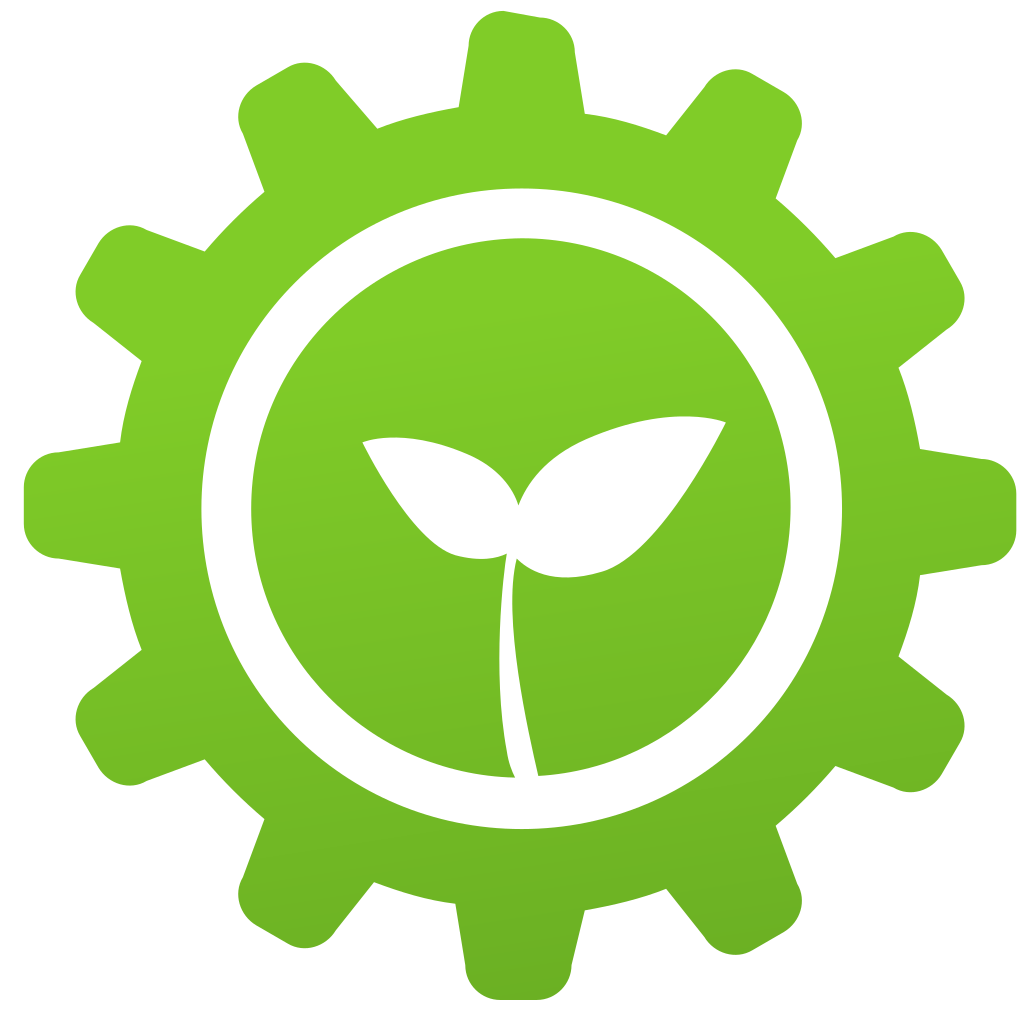
Innovative system recovers heat, water and material from industrial waste streams
Resumo
The paper discusses the successful commissioning of an innovative Heat Pipe Condensing Economiser (HPCE) at Alufluor AB in Sweden, an aluminium fluoride producer. The HPCE enables the recovery of heat, water, and materials from exhaust streams, a process previously thought unviable. The system allows Alufluor to heat all their washing water with recycled energy. This breakthrough in the chemical process industry, regarded as a disruptive innovation, resulted from over three years of engineering, planning, and investment, including facility modifications and pipeline installation. The HPCE has been operational since August 1st, with a 650kW average capacity from the company's exhaust stream. Professor Hussam Jouhara of Brunel University London suggests that while all industries could potentially adopt the technology, the chemical industry, due to its stringent regulations, stands to benefit significantly. The HPCE's design features—such as safety, modularity, and flexible geometry—underscore its adaptability.
Artigo aberto completo
Innovative system recovers heat, water and material from industrial waste streams
We are excited to announce that the first innovative Heat Pipe Condensing Economiser (HPCE) has been commissioned at our project partner Alufluor AB in Sweden and is running. The aluminium fluoride producer is now heating all their washing water with recycled energy!
“Until now, viable indirect condensing economisers from exhaust streams were not available”, explains inventor and technical director of the iWAYS project Prof. Hussam Jouhara from Brunel University London. “What we have demonstrated now is that it is doable to recover heat, water and material using existing materials and knowledge.”
The launch of the iWAYS system at Alufluor is a major milestone for all participants. “In the chemical process industry, everyone works hard to achieve energy savings”, says Hanna Sjöberg, CEO of Alufluor. “And while the small, incremental improvements in energy efficiency we normally see are valuable, there are rare moments when disruptive innovation leads to a substantial breakthrough. This is one of those moments for us.”
The journey to this achievement has been marked by extensive engineering efforts and significant investments. “We have been working with this for more than three years now, and during that time, we have done a lot of engineering,” says Dan Turesson, Technical Director at Alufluor. “We have invested a lot in rearranging our facilities to handle the energy recovery, reinforcing our rooftop to support the HPCE, and installing hundreds of meters of new pipelines throughout our plant.”
These efforts will pay off now. “The unit has been in operation since the 1st of August, with an average capacity of 650kW from the company’s exhaust stream,” says Prof. Jouhara. “With the HPCE we will be able to recover a significant portion of the energy from the stack and reuse it in the process.”
But is this technology also applicable to other industries? “The heat pipes allow safer operation, multiple contingency, modular design, and flexible geometry. You can apply the same thing to any other industry”, explains Prof. Jouhara. “But the heavily regulated chemical industry in particular will benefit the most, I believe.”