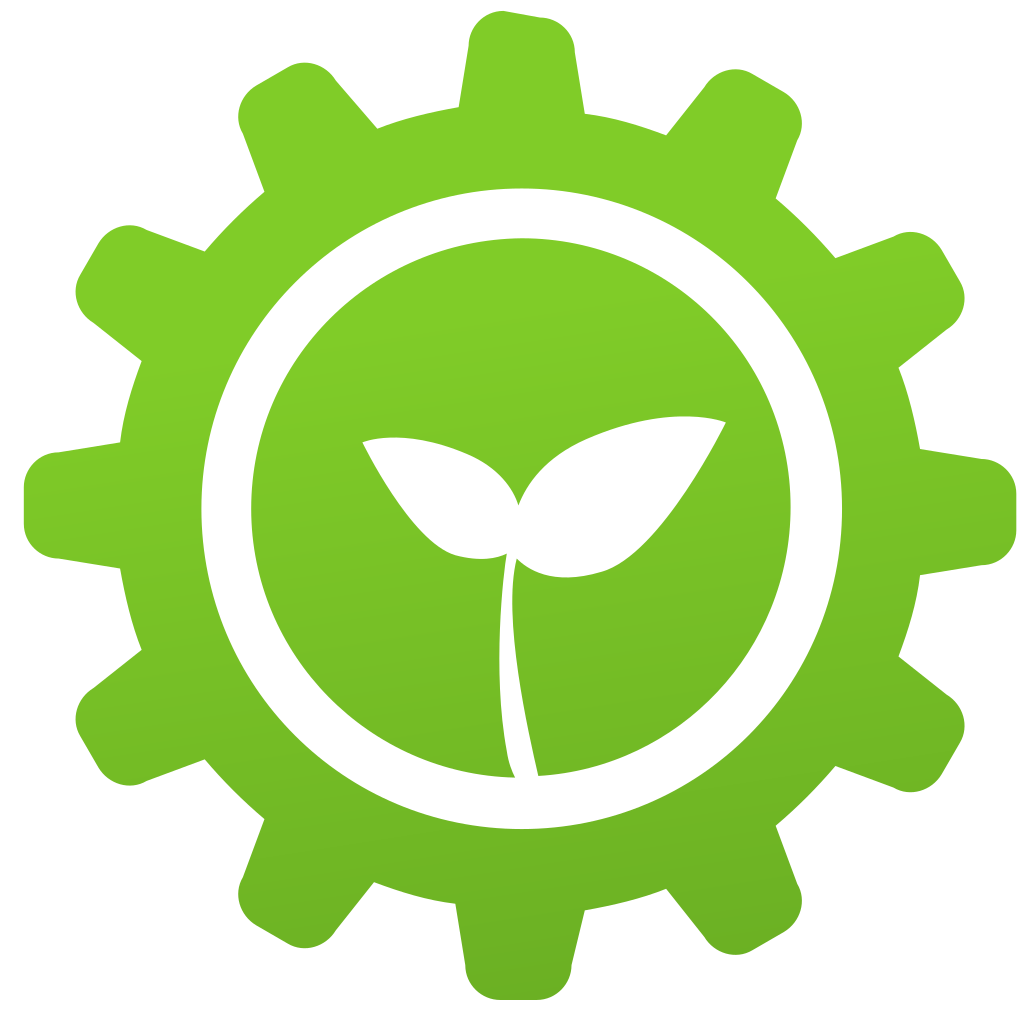
Deep decarbonisation of industry: The cement sector
Zusammenfassung
Fossil fuel combustion to meet heating needs accounts for 35% of cements CO2 emissions. The remaining 65% are due to direct process emissions, which must also be addressed. By 2050, cement production in the EU is expected to remain below pre-2010 levels. In the EU, 90% of clinker is now made via the more energy efficient dry clinker-making process. Older, less efficient wet kilns have almost been phased out. The co-processing of fuels (use of alternative fuels, such as waste and biomass) currently represent nearly half of all fuels used in the EU cement industry, with some cement plants reaching occasional substitution rates of 100%-
While alternative fuels could provide 100% of the thermal energy, full substitution of fossil fuels with truly sustainable biomass is technically challenging due to the lower calorific value of most organic materials.
Kompletten Artikel anzeigen
Deep decarbonisation of industry: The cement sector
Headlines
- Fossil fuel combustion to meet heating needs accounts for 35% of cement’s CO2 emissions. The remaining 65% are due to direct process emissions, which must also be addressed.
- The biomass use in the cement industry has tripled since 2007, currently accounting for 16% of the fuel mix.
- The analysis of decarbonisation scenarios published recently by various sources shows that:
- The role of biomass in decarbonising the sector by 2050 is uncertain due to increased competing demand from other sectors of the economy.
- Deploying carbon capture and storage is unavoidable for deep decarbonisation due to the process emissions inherent to cement making.
Recommendations
- Support the development of large-scale demonstration projects for breakthrough technologies, including the electrification of kilns, carbon capture technologies and novel cements.
- Support the deployment of a CO2 infrastructure, including transport networks, CO2 storage and CO2 valorisation through industrial symbiosis.
- Strengthen green public procurement and accelerate the update of product standards to increase demand for low-carbon building materials.
........................................................................................................................................................................................................
Cement sector overview
Cement is the binding agent of concrete, the most widely used construction material in the world. The cement sector is a major greenhouse gas emitter, responsible for about 7% of CO2 emissions globally (1), and about 4% in the EU.
While global emissions from the cement sector have continually increased, in the EU emissions peaked in 2007 at 170Mt CO2 and have dropped by 40% since then to 105Mt CO2 (2). This is mainly attributable to the sharp decline in cement production over the last 15 years, from a peak of 262Mt in 2007 to 168Mt in 2017, equivalent to a reduction in cement per capita from 0.5 to 0.3 tonnes per person (3). The CO2 intensity of cement production over that period has improved by about 7% (0.6t of CO2 emitted per tonne of cement in 2017) (2).
By 2050, cement production in the EU is expected to remain below pre-2010 levels, ranging between 165Mt and 206Mt in the FORECAST model scenarios (4), which fed the industry analysis of the European Commission’s Long-Term Strategic Vision (5).
Process heat overview
Clinker, and clinker substitutes, are the active components that confer cement its binding properties. Producing traditional cement clinker is an extremely energy and CO2 intensive process. In the EU, 90% of clinker is now made via the more energy efficient dry clinker-making process (2). Older, less efficient wet kilns have almost been phased out. In the more advanced dry process, raw ingredients are calcinated at around 900-1250oC in a precalciner to transform limestone into lime, which releases CO2 as a side product. The materials are then fed into a rotary kiln, where they aggregate to form clinker at 1450oC (and flame temperatures reach 2000oC) (6). The clinker is then cooled, ground and blended with other materials to make cement.
The combustion of fuels to heat cement kilns is responsible for 35% of clinker’s carbon footprint. The other 65% are process emissions, released during the calcination reaction involved in the production of clinker.
Decarbonisation options
Biomass
Currently, the fuels used to provide the necessary process heat are a mix of fossil fuels (mainly petcoke, coal and oil), waste fuels and biomass. While biomass usage has tripled since 2007, it currently only accounts for 16% of the total fuel mix in the EU (Figure 1).
The co-processing of fuels (use of alternative fuels, such as waste and biomass) currently represent nearly half of all fuels used in the EU cement industry, with some cement plants reaching occasional substitution rates of 100% (6). There are however considerable differences between Member States, ranging from 6% (Greece) to 65% (Germany) national average co-processing rates (7).
While alternative fuels could provide 100% of the thermal energy, full substitution of fossil fuels with truly sustainable biomass is technically challenging due to the lower calorific value of most organic materials (8). Moreover, by 2050, competing claims for biomass from other sectors of the economy will limit its availability for cement production. The deep decarbonisation scenarios from the European Commission’s Long-term strategic vision indicate at least half of available biomass being used for the power sector.
Electrification of heat
Using electricity to provide process heat could contribute to decarbonising the sector, if the electricity is 100% fossil fuel free. The cement industry is exploring several technologies to electrify cement production, including generating the heat via plasma generators and microwave energy, which have yet to be developed beyond the laboratory (TRL 3). The construction of a pilot plant that uses plasma technology is currently being investigated (9).
An important possible benefit of electrified heating systems is the much higher concentrations of CO2 in the flue gases than with combustion heating, from an estimated 25% CO2 concentration to close to 100% (10). This would allow easier capture and purification of CO2 from process emissions.
Hydrogen for heat
Combusting hydrogen as a fuel can reach the high temperatures required in the cement manufacturing process, but has not yet been tested. As hydrogen’s combustion and the heat transfer (by radiation) in the kiln would differ significantly from fuels currently used, extensive research into the modifications to the cement kilns would be needed (11). Cement production using a mixture of hydrogen and biomass fuels is currently at an early stage of investigation (TRL 2).
Carbon capture
To fully decarbonise the sector, process emissions from the clinker-making process need to be addressed, regardless of the heat source. Part of the solution will need to be CO2 capture – applied to both the combustion and process emissions, or combining a zero-CO2 heat source with the capture of concentrated process emissions.
Several different breakthrough technologies are currently being investigated in the EU, which are all at TRL 6: (i) post-combustion technologies that separate CO2 from the flue gas; (ii) oxyfuel combustion, where the fuel is burned in oxygen rather than air, providing a much higher concentration of CO2 in the flue gas; (iii) calcium-looping, which can be integrated into the cement plant or used as a tail-end technology; (iv) and direct separation technology, applied in combination with a zero-CO2 heat process. The choice of technologies will depend on their techno-economic competitiveness, and will vary depending on the availability of renewable electricity and waste heat recovery and integration (12).
CO2 storage and utilisation
Beyond the implementation of carbon capture technologies to address the process emissions and the possible remaining fuel combustion emissions, the infrastructure to transport, store or utilise CO2 needs to be developed. As the potential for CO2 valorisation is limited by the resulting products’ market demand (13), and considering the amount of carbon dioxide emitted by cement manufacturing (106Mt in 2016), CO2 storage will likely be an unavoidable route to achieve deep decarbonisation.
Low-carbon cements
The average clinker-to-cement ratio in the EU in 2017 was 75% (2). The European Standards differentiates five main categories of cements based on their clinker composition. The most used cements, Portland and Portland-composite cements, have clinker contents over 95% and 65% respectively. Clinker can be partially substituted by so-called supplementary cementitious materials, such as fly ash from coal power plants and blast furnace slag from steelmaking. Due to the reduced clinker ratio, less energy is required for clinker-burning and some of the process emissions inherent to clinker-making are avoided. Depending on the decarbonisation paths followed by the power and steel sectors, these alternative feedstocks will however become less available in the future.
There is considerable on-going research on alternative clinkers that emit less CO2 than Portland cement. Some are already commercially available (but with limited applications), while a number of other concepts are under research and development (14); however supply side barriers (e.g. availability and cost of raw materials) and demand side barriers (e.g. restrictions in concrete standards) limit their application and diffusion.
The cement industry in 2050 decarbonisation scenarios
To explore different pathways to achieve deep decarbonisation of the sector by 2050, the decarbonisation options in eight scenarios from four publications are compared (see Figure 2). The PRIMES and FORECAST scenarios that fed the European Commission’s Long-Term Strategic Vision consider the whole non-metallic minerals sector jointly (cement, ceramics, glass and lime). Cement production accounts for 40% of the total non-metallic minerals sector’s final energy demand and 60% of its CO2 emissions.
Biomass
There is strong variation in the use of biomass for cement production by 2050 in the examined scenarios. A fully electrified pathway could forego biomass use by 2050 (ECF, New Processes), while in other pathways, up to 4-times more biomass than in 2015 is deployed (EC, 1.5TECH). Negative emissions are included in some scenarios that combine sustainable biomass use with CO2 capture from biogenic sources (IEA, B2DS). In several scenarios, an early fuel switch to biomass allows for early emissions reductions before other breakthrough technologies are deployed (biomass use doubles from 2015 to 2030 in ICF, CCS and Mix95).
Electrification
The use of electricity increases in 7 out of the 8 selected scenarios. Scenarios that deploy carbon capture technologies but little electrified heat see little (or no) increase in electricity demand, with a higher remaining share of fossil fuels (ICF, CCS; ICF, CCS; IEA, B2DS). In a scenario where cement production is fully electrified, the demand for renewable electricity is up to 6-times the 2015 electricity demand (ECF, New Processes).
Hydrogen
The role of hydrogen varies greatly in the scenarios, ranging from no deployment in the final energy mix up to a third of energy demand in scenarios covering the total non-metallic minerals sector (ICF, Mix95; EC, 1.5LIFE and 1.5TECH).
Carbon capture
All the selected scenarios achieving deep decarbonisation of the cement sector include carbon capture technologies, which is seen as the most important technology to reduce process emissions, as well as emissions from industrial heat when those are still present. By 2050, in several scenarios over 90% of cement plants incorporate carbon capture (ICF, CCS and Mix95), with up to 120Mt CO2 captured (ICF, CCS). Where specified, the carbon capture technology deployed varies depending on the decarbonisation pathway, with up to 100% of cement kilns fitted with post-combustion carbon capture in a fully electrified scenario (ECF, New Processes), or 90% of kilns fitted with oxy-fuel technology in combination with fossil fuels (ECF, CCS).
Low carbon cements
Clinker substitutes and/or new cements are deployed to reduce the sector’s CO2 emissions to varying extents in the scenarios. Although not explicitly specified in all cases, supplementary cementitious materials are included in all scenarios and could substitute up to 40% of cement clinker in 2050 (ECF scenarios, compared with 26% today). New low-carbon cement types are not included at all (ICF CCS and IEA B2DS) or to a very restricted extent (5% substitution in ECF scenarios) in some scenarios. One scenario deploys new cements to replace 50% of total cement production by 2050 (83Mt out of 166Mt in ICF, Mix95).
Circular economy and material efficiency
Some scenarios (ICF, Mix95 and ECF, Circular Economy) rely on a more efficient use of cement and concrete. Several options are proposed, including optimising the design of structures and concrete specifications, designing infrastructure to allow for disassembly and reuse/recycling of concrete, or substituting concrete with zero-CO2 materials such as wood (up to 5% substitution in ECF scenarios). While not replacing the need for carbon capture in those scenarios, such decarbonisation options could alleviate the deployment and associated costs of carbon capture technologies. Digitalisation is mentioned as potentially playing an important role in optimising the design and use of lower- CO2 options in construction (15). Fully capturing these material efficiency potentials however would require major changes to existing standards and construction processes.
References
1. International Energy Agency. Technology Roadmap - Low-Carbon Transition in the Cement Industry. 2018.
2. WBSCD. Getting the numbers right (GNR) Project. www.wbcsdcement.org/GNR-2016/index.html.
3. Eurostat. Population change - Demographic balance and crude rates at national level [demo_gind].
4. ICF & Fraunhofer ISI. Industrial Innovation: Pathways to deep decarbonisation of Industry. Part 2. 2018.
5. European Commission. In-depth analysis in support of the commission communication COM(2018) 773. 2018.
6. Joint Research Centre. Best Available Techniques (BAT) Reference. European Commission, 2013.
7. Ecofys. Market opportunities for use of alternative fuels in cement plants across the EU. 2016.
8. Murray, A and Price, L. Use of Alternative Fuels in Cement Manufacture: Analysis of Fuel Characteristics and Feasibility for Use in the Chinese Cement Sector. Berkeley National Laboratory, 2008.
9. Vattenfall. Press release - Vattenfall and Cementa take the next step towards a climate neutral cement. January 2019. group.vattenfall.com/press-and-media/news--pressreleases/pressreleases/2019/vattenfall-and-cementa-take-the-nextstep-towards-a-climate-neutral-cement.
10. Wilhelmsson, Bodil, et al., et al. CemZero - A Feasibility Study Evaluating Ways to Reach Sustainable Cement Production via the Use of Electricity. Vattenfall and Cementa, 2018.
11. Hoenig, Volker, Hoppe, Helmut and Emberger, Bernhard. Technical Report: Carbon Capture Technology - Options and Potentials for the Cement Industry. ECRA, 2007.
12. Vatopoulos, Konstantinos and Tzimas, Evangelos. Assessment of CO2 capture technologies in cement manufacturing process. Journal of Cleaner Production, Vol. 32, 2012.
13. Pérez-Fortes , Mar, et al., et al. Methanol synthesis using captured CO2 as raw material: Techno-economic and environmental assessment. Applied Energy, Vol. 161, 2016.
14. Gartner, Ellis and Sui, Tongbo. Alternative cement clinkers. Cement and Concrete Research, Vol. 114, 2018.
15. Lehne, Johanna and Preston, Felix. Making Concrete Change - Innovation in Low-carbon Cement and Concrete. London, Chatham House, 2018.
16. Material Economics. Industrial Transformation 2050 - Pathways to Net-Zero Emissions from EU Heavy Industry. 2019.
17. International Energy Agency (IEA). Energy Technology Perspectives 2017: Catalysing Energy Technology Transformations. 2017.
Contact:
This factsheet by the Joint Research Centre, the European Commission’s science and knowledge service, aims to provide evidence-based scientific support to the European policymaking process. The scientific output expressed does not imply a policy position of the European Commission. Neither the European Commission nor any person acting on behalf of the Commission is responsible for the use that might be made of this publication.