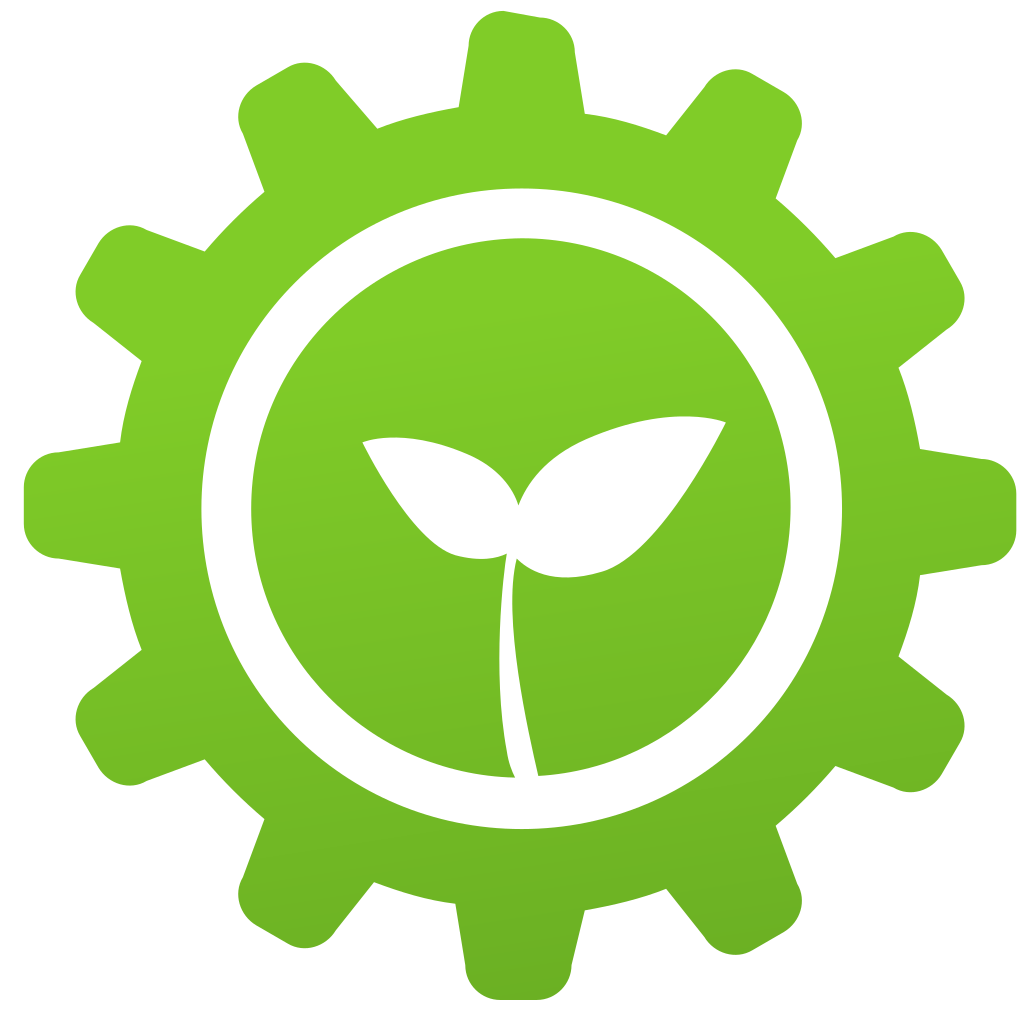
Business Practices
Insuring Production Up-Time at New Center Stamping
Summary
Production at the New Center Stamping plant is highly dependent on access to a reliable source of compressed air. Only a 25% reduction in available pressure causes air - dependent machinery to automatically shut down. When the air supply cannot be restored immediately, production ceases and workers are sent home until it is back up and running. A customized, self contained compressed air plant - a unique solution known as DirectAIR® - was created. The company expects to reduce maintenance costs, lower their energy bill, improve the work environment and reduce production down time by at least 1000 minutes per year - on just one of their production lines)
The solution was installed without any capital outlay and, coupled with several other upgrades within the plant, resulted in a significant utility rebate as well as being eligible for Michigan Saves financing. It is easy to understand why affordable upgrades of outdated equipment is not an option - but a revenue protecting - necessity - and it is also possible to save $150,000.
Open full article
Insuring Production Up-Time at New Center Stamping
Insuring Production Up-Time at New Center Stamping
When unexpected delays in production represent a significant loss of revenue, the reliability of systems integral to production becomes a necessity.
The Energy Alliance Group of Michigan’s latest project is very interesting.
It illustrates how cutting edge technology, energy efficiency and appropriate financing all work together to maximize production in a manufacturing environment.
“The cost barrier of upgrading to efficient and dependable production equipment can now be overcome through the use of innovative options!” Scott Ringlein
Production at the New Center Stamping plant is highly dependent on access to a reliable source of compressed air. Only a 25% reduction in available pressure causes air – dependent machinery to automatically shut down. If the air supply cannot be restored immediately, production ceases and workers are sent home until it’s back up and running.
The company’s existing compressed air system was a collection of equipment from various decades. Some of the equipment dated as far back as the 1920’s when the building – made famous in the movie 8 Mile – was constructed. One piece of equipment, still in use far beyond its expected lifespan, had been manufactured by a company long since out of business. When it – a production critical unit – broke down, replacement parts were no longer available to make the necessary repairs. After a replacement unit was priced at more than $150,000, a system – wide upgrade was discussed.
The Energy Alliance Group of Michigan (EAG) was tasked with developing a comprehensive replacement for New Center’s piecemeal and outdated compressed air system. EAG teamed up with one of our alliance partners, Air Technologies. After an extensive “air audit,” the quantity of air needed for full production was calculated. Based on that number, a customized, self contained compressed air “plant” – a unique solution known as DirectAIR® – was created. Installed adjacent to the factory, once electrical power, a heat exchanger and air delivery lines were connected to the “plant”, a completely upgraded, high – tech source of compressed air was online and fully operational. The previous “system” would no longer interfere with production. And, New Center
Stamping only pays for the quantity of compressed air actually used!
The New Center staff was happy to note the solution included a variety of unexpected benefits beyond maintaining reliable production:
- Dramatic noise reduction – with the compressors now housed in a separate structure outside the building, the noise level within the building dropped dramatically.
- Air consumption computer controlled – less waste and a significant reduction in electrical use due to computer monitored air production resulting in optimum air volume with no excess.
- Improved space utilization – the former compressed air equipment will be removed and the now free space will be converted into a new storage area.
- Zero down time – all maintenance and repairs of the DirectAIR® equipment are included with the service and the equipment is constantly monitored offsite. Automated system alerts provide DirectAIR® service technicians with the spontaneous information they need that allows them to show up for service before the New Center staff is even aware a problem is developing. Backup systems are also contained in the unit to guarantee zero downtime.
“DirectAIR® allows us to guarantee the quantity of air, operating pressure and absence of moisture – 24/7 – with ZERO downtime. No more nuisance calls, waiting for parts or waiting for service.” Darryl Kukla, Air Technologies
The DirectAIR® solution was installed without any capital outlay and, coupled with several other upgrades within the plant, resulted in a significant utility rebate as well as being eligible for Michigan Saves financing. The company expects to reduce maintenance costs, lower their energy bill, improve the work environment and reduce production down time by at least 1000 minutes per year – on just one of their production lines.
When production is as dependent on reliable compressed air as most companies are on electricity, it’s easy to understand why affordable upgrades of outdated equipment is not an option – but a revenue protecting – necessity.
See also:
How much energy can New Center Stamping save?
Ten Questions to Ask Before an Energy Efficiency Upgrade!
Kerry Kilpatrick
Email: kkilpatrick(at)energyalliancegroup.org
(originally posted on The Energy Alliance Group of North America)