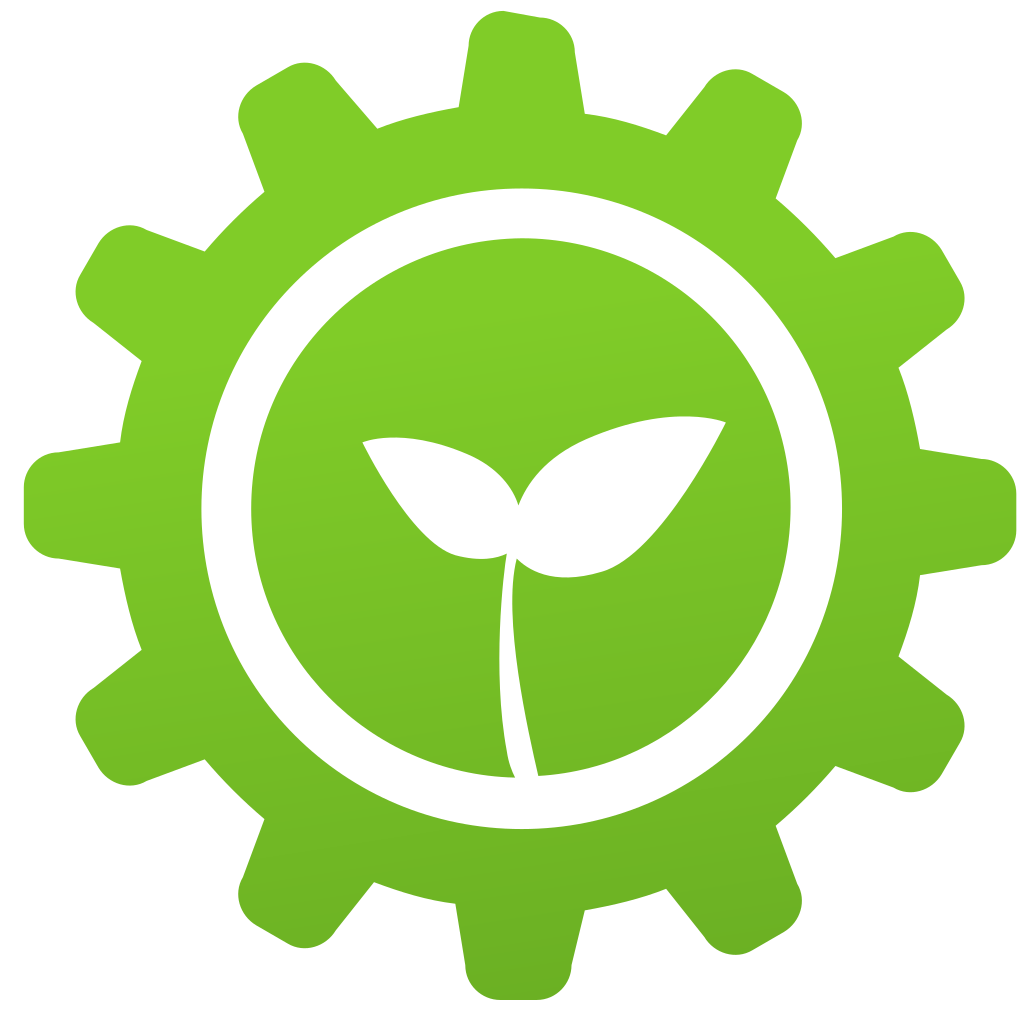
Cas Pratiques
Assurer le temps de production au nouveau centre d'estampage
Résumé
La production de l'usine d'emboutissage de New Center dépend fortement de l'accès à une source fiable d'air comprimé. Une réduction de 25 % seulement de la pression disponible entraîne l'arrêt automatique des machines dépendantes de l'air. Lorsque l'alimentation en air ne peut être rétablie immédiatement, la production s'arrête et les travailleurs sont renvoyés chez eux jusqu'à ce que l'alimentation soit rétablie. Une centrale d'air comprimé autonome et personnalisée - une solution unique connue sous le nom de DirectAIR® - a été créée. L'entreprise espère réduire les coûts de maintenance, diminuer sa facture énergétique, améliorer l'environnement de travail et réduire les temps d'arrêt de production d'au moins 1000 minutes par an - sur une seule de ses lignes de production).
La solution a été installée sans aucune dépense d'investissement et, associée à plusieurs autres améliorations au sein de l'usine, elle a permis de bénéficier d'une remise importante de la part des services publics et d'être éligible au financement de Michigan Saves. Il est facile de comprendre pourquoi les mises à niveau abordables d'équipements obsolètes ne sont pas une option - mais une nécessité pour protéger les revenus - et il est également possible d'économiser 150 000 $.
Ouvrir l'article complet
Assurer le temps de production au nouveau centre d'estampage
Assurer le temps de production au nouveau centre d'emboutissage
Lorsque des retards imprévus dans la production représentent une perte importante de revenus, la fiabilité des systèmes faisant partie intégrante de la production devient une nécessité.
Le dernier projet du groupe Energy Alliance du Michigan est très intéressant.
Il illustre comment la technologie de pointe, l'efficacité énergétique et un financement approprié travaillent ensemble pour maximiser la production dans un environnement de fabrication.
"Le coûtde la mise à niveau vers des équipements de production efficaces et fiablespeut maintenant être surmonté grâce à l'utilisation d'options innovantes ! Scott Ringlein
La production de l'usine de New Center Stamping dépend fortement de l'accès à une source fiable d'air comprimé. Seule une réduction de 25 % de la pression disponible entraîne l'arrêt automatique des machines dépendantes de l'air. Si l'alimentation en air ne peut être rétablie immédiatement, la production cesse et les travailleurs sont renvoyés chez eux jusqu'à ce qu'elle soit de nouveau opérationnelle.
Le système d'air comprimé existant de l'entreprise était un ensemble d'équipements datant de plusieurs décennies. Certains de ces équipements datent des années 1920, époque à laquelle le bâtiment - rendu célèbre par le film 8 Mile- a été construit. Un des équipements, toujours utilisé bien au-delà de sa durée de vie prévue, avait été fabriqué par une entreprise qui avait cessé ses activités depuis longtemps. Lorsqu'il est tombé en panne - une unité critique de production - les pièces de rechange n'étaient plus disponibles pour effectuer les réparations nécessaires. Après qu'une unité de remplacement ait été évaluée à plus de 150 000 dollars, une mise à niveau du système a été discutée.
L'Energy Alliance Group of Michigan (EAG) a été chargé de mettre au point un remplacement complet du système d'air comprimé fragmentaire et obsolète de New Center. L'EAG a fait équipe avec l'un de nos partenaires d'alliance, Air Technologies. Après un "audit d'air" approfondi, la quantité d'air nécessaire pour une production complète a été calculée. Sur la base de ce chiffre, une "usine" d'air comprimé personnalisée et autonome - une solution unique connue sous le nom de DirectAIR® - a été créée. Installée à côté de l'usine, une fois que l'énergie électrique, un échangeur de chaleur et des lignes de distribution d'air ont été connectés à l'"usine", une source d'air comprimé de haute technologie, complètement modernisée, a été mise en ligne et est devenue pleinement opérationnelle. L'ancien "système" n'interférerait plus avec la production. Et, le nouveau centre
L'estampillage ne paie que la quantité d'air comprimé réellement utilisée !
Le personnel du nouveau centre a été heureux de constater que la solution comprenait une série d'avantages inattendus, au-delà du maintien d'une production fiable :
- Réduction spectaculaire du bruit - les compresseurs étant désormais logés dans une structure séparée à l'extérieur du bâtiment, le niveau de bruit à l'intérieur du bâtiment a considérablement baissé.
- Consommation d'air contrôlée par ordinateur - moins de gaspillage et une réduction significative de laconsommation électrique grâce à une production d'air contrôlée par ordinateur, ce qui permet d'obtenir un volume d'air optimal sans excès.
- Meilleure utilisation de l'espace - l'ancien équipement à air comprimé sera supprimé et l'espace désormais libre sera converti en une nouvelle zone de stockage.
- Zéro temps d'arrêt - tous les entretiens et réparations du DirectAIR® sont inclus dans le service et l'équipement est constamment surveillé hors site. Des alertes automatisées du système fournissent des informations directessur lesAIR® avec les informations spontanées dont ils ont besoin, ce qui leur permet de se présenter au service avant même que le personnel du nouveau centre ne soit conscient d'un problème. Des systèmes de sauvegarde sont également contenus dans l'unité afin de garantir un temps d'arrêt zéro.
“DirectAIR® nous permet de garantir la quantité d'air, la pression de fonctionnement et l'absence d'humidité - 24 heures sur 24, 7 jours sur 7 - avec un temps d'arrêt ZÉRO. Plus d'appels intempestifs, d'attente de pièces ou de service". Darryl Kukla, Air Technologies
Le directAIRCette solution a été installée sans aucune mise de fonds et, associée à plusieurs autres améliorations dans l'usine, elle a permis de bénéficier d'un rabais important sur les services publics et d'être éligible au financement de Michigan Saves. L'entreprise espère réduire les coûts de maintenance, diminuer sa facture énergétique, améliorer l'environnement de travail et réduire les temps d'arrêt de production d'au moins 1000 minutes par an - sur une seule de ses lignes de production.
Lorsque la production est aussi dépendante d'un air comprimé fiable que la plupart des entreprises le sont de l'électricité, il est facile de comprendre pourquoi la mise à niveau à un prix abordable d'équipements obsolètes n'est pas une option, mais une nécessité qui protège les revenus.
Voir aussi :
Combien d'énergie le nouveau centre d'estampage peut-il économiser ?
Dix questions à poser avant de procéder à une mise à niveau de l'efficacité énergétique !
Kerry Kilpatrick Courriel : kkilpatrick(at)energyalliancegroup.org
(initialement publié sur The Energy Alliance Group of North America)