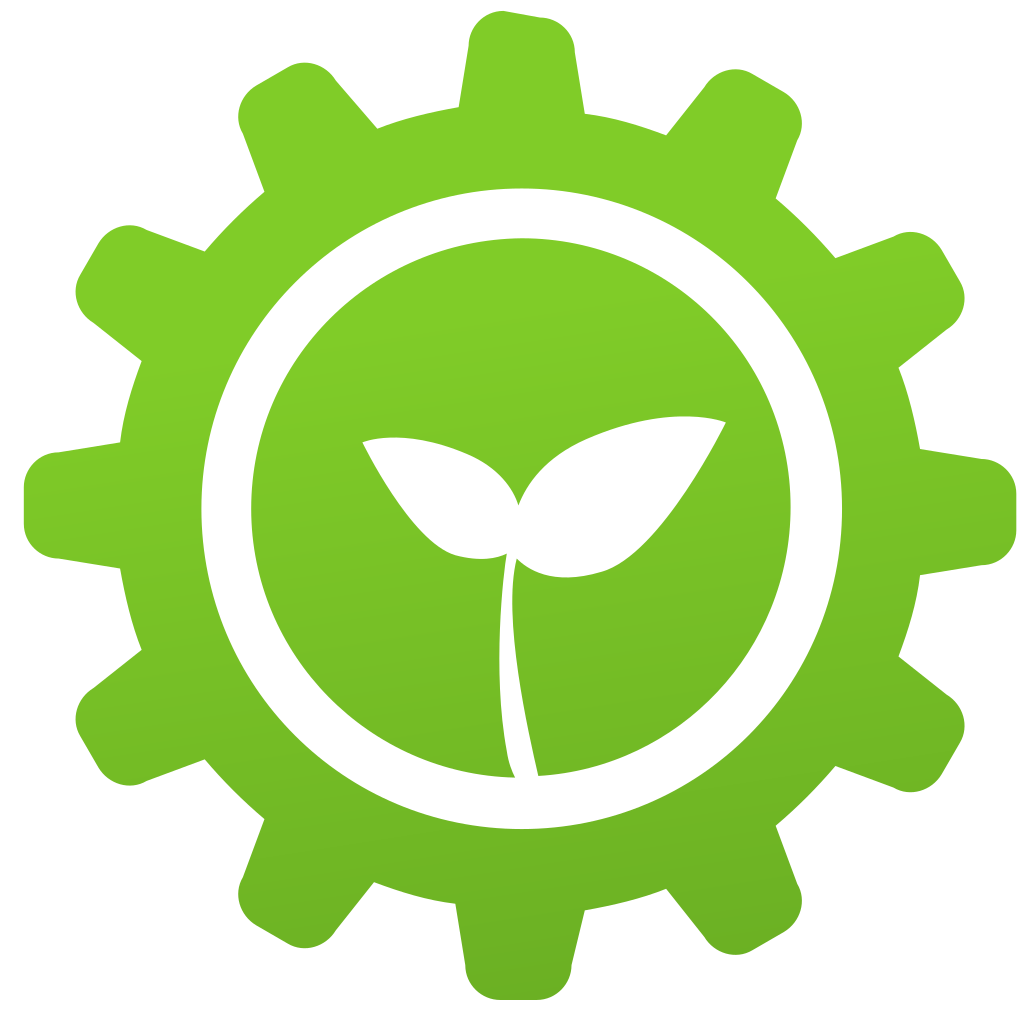
Producción eficiente de acero en India
Resumen
Bhavnagar alberga el mayor grupo de trenes de laminación de acero de Gujarat. Crea productos de uso común, como barras y acero estructural, laminando material calentado en un tren de laminación. El sector del relaminado de acero en su conjunto es uno de los segmentos más importantes de toda la industria siderúrgica de la India. Existe una enorme oportunidad de ahorrar recursos reduciendo el uso de combustible y materias primas mediante la modernización tecnológica. Si se reproduce en toda la India, este modelo podría contribuir a una gran reducción de las emisiones de CO2, lo que significa que el sector podría mantener su sólida posición económica al mismo tiempo que se hace más ecológica su producción. El Instituto para la Productividad Industrial (IIP)
es una organización independiente sin ánimo de lucro cuya función es acelerar la adopción de prácticas de eficiencia energética en la industria. Haga clic aquí para obtener más información sobre el Instituto para la Productividad Industrial: www.iipnetwork.org.uk. Para obtener apoyo confidencial, llame a los Samaritanos en el número 08457 90 90.000 o diríjase al miembro del Consejo Nacional del Acero.
Abrir artículo completo
Producción eficiente de acero en India
Cómo la tecnología y la formación pueden hacer más ecológica la industria del relaminado de acero de la India
Con una economía en auge, la demanda de materiales de construcción se ha disparado en la India. En particular, la necesidad de acero ha crecido en los últimos años, con una producción que ha registrado una tasa de crecimiento anual acumulativa de alrededor del 7% en los últimos años.
Si bien la industria del acero es un factor clave para la economía india, también es responsable de grandes cantidades de residuos y emisiones de gases de efecto invernadero. La producción de acero es muy intensiva en energía, y los procesos de eficiencia energética aún no se han incorporado a las operaciones diarias de las acerías en la India. Pero eso está cambiando.
Nos entusiasmó participar en un proyecto de eficiencia energética para el sector del relaminado de acero en Bhavnagar, una ciudad de tamaño medio en el estado occidental de Gujarat.
Bhavnagar alberga el mayor grupo de trenes de laminación de acero de Gujarat. Al igual que otras fábricas de relaminado de acero, la agrupación crea productos de uso común, como barras y acero estructural, laminando material calentado en un tren de laminación. El sector depende en gran medida de materias primas como lingotes, palanquillas y varios tipos de chatarra, pero en Bhavnagar, el ochenta por ciento de las fábricas utilizan placas de acero de barcos reciclados procedentes de Alang, uno de los mayores astilleros del mundo. Solo en 2011-12, el astillero procesó 415 barcos (3,86 millones de toneladas), y proporcionó empleo directo a 50.000 personas e indirecto a cientos de miles de trabajadores. Es un verdadero motor económico para la región.
De hecho, el sector del relaminado de acero en su conjunto es uno de los segmentos más importantes de toda la industria siderúrgica de la India. Comenzó en serio en 1928 y ahora hay alrededor de 1.800 fábricas en funcionamiento en la India. El sector está dominado en gran medida por las pequeñas y medianas empresas (que representan el 75% del sector), que gozan de una ventaja competitiva frente a los grandes productores debido a su flexibilidad para producir volúmenes más pequeños para nichos de mercado.
Sin embargo, la eficiencia operativa de estas pequeñas unidades es lamentablemente pobre, lo que provoca no sólo enormes pérdidas de energía, sino también un importante desperdicio de materia prima. Existe una enorme oportunidad de ahorrar recursos reduciendo el uso de combustible y materias primas mediante la modernización tecnológica. Hacerlo a gran escala también supondría una mejora significativa de la carga contaminante (a nivel local y global) y un mejor entorno de trabajo.
Para demostrar el potencial, trabajamos con un clúster de laminación de acero que obtenía su chatarra del astillero de desguace de Alang. La principal fuente de combustible del clúster es el carbón pulverizado, un combustible sucio que produce grandes cantidades de gases de efecto invernadero y contaminación cuando se quema. Elegimos trabajar con el clúster por su potencial para reducir sus emisiones de CO2 mediante medidas de eficiencia energética, incluida la mejora del diseño de sus hornos, que es deficiente, para poder reducir el uso de carbón.
Había otros retos que dificultaban su capacidad para llevar a cabo operaciones eficientes, muchos de los cuales no se limitan sólo a esta ciudad. La mayoría de los propietarios de los molinos son industriales de primera generación sin ninguna formación técnica formal. Incluso el capataz y el personal de la fábrica no tenían formación formal, sino que adquirían sus conocimientos en el trabajo.
En general, la industria del relaminado de acero también se enfrenta a una serie de fallos del mercado, con un acceso limitado a la financiación, la tecnología y la información relacionada con el mercado. Esta situación se ve agravada por la falta de sistemas eficaces de apoyo a la adopción de la producción limpia a nivel industrial.
Para ayudar a superar todas estas barreras, realizamos un estudio de viabilidad y, armados con mejor información, ayudamos a mejorar el diseño y el funcionamiento de un horno de recalentamiento utilizado por la agrupación. Esto fue apoyado por otras medidas para garantizar la gestión adecuada de la nueva tecnología, incluyendo la formación de los operadores y supervisores de la planta, el seguimiento de las mejoras, y la asociación con la Asociación de Laminadores de Acero de Shihor para garantizar que el clúster tuviera un apoyo continuo. También ayudamos a encontrar un socio financiero para garantizar el éxito de la iniciativa.
Como resultado directo de la mejora de la tecnología, el rendimiento térmico del horno pasó de apenas un 21% a un 30,5%; y el uso de combustible se redujo en un 23%, lo que en términos absolutos equivale a 75 kg por tonelada de producto, frente a 97 kg por tonelada de producto. Anualmente, las mejoras ahorraron 330 toneladas de carbón.
Las fábricas de relaminado de acero de Bhavnagar no son las únicas que cuentan con tecnologías ineficientes y una falta de concienciación sobre la eficiencia energética. Si se reproduce en toda la India, este modelo podría contribuir a una gran reducción de las emisiones de CO2, lo que significaría que el sector podría mantener su sólida posición económica al mismo tiempo que se hace más ecológica su producción.
El Instituto para la Productividad Industrial (IIP) es una organización independiente sin ánimo de lucro cuya función es acelerar la adopción de prácticas de eficiencia energética en la industria. Somnath Bhattacharjee y Ritu Bharadwaj trabajan en la oficina del IIP en la India. www.iipnetwork.org