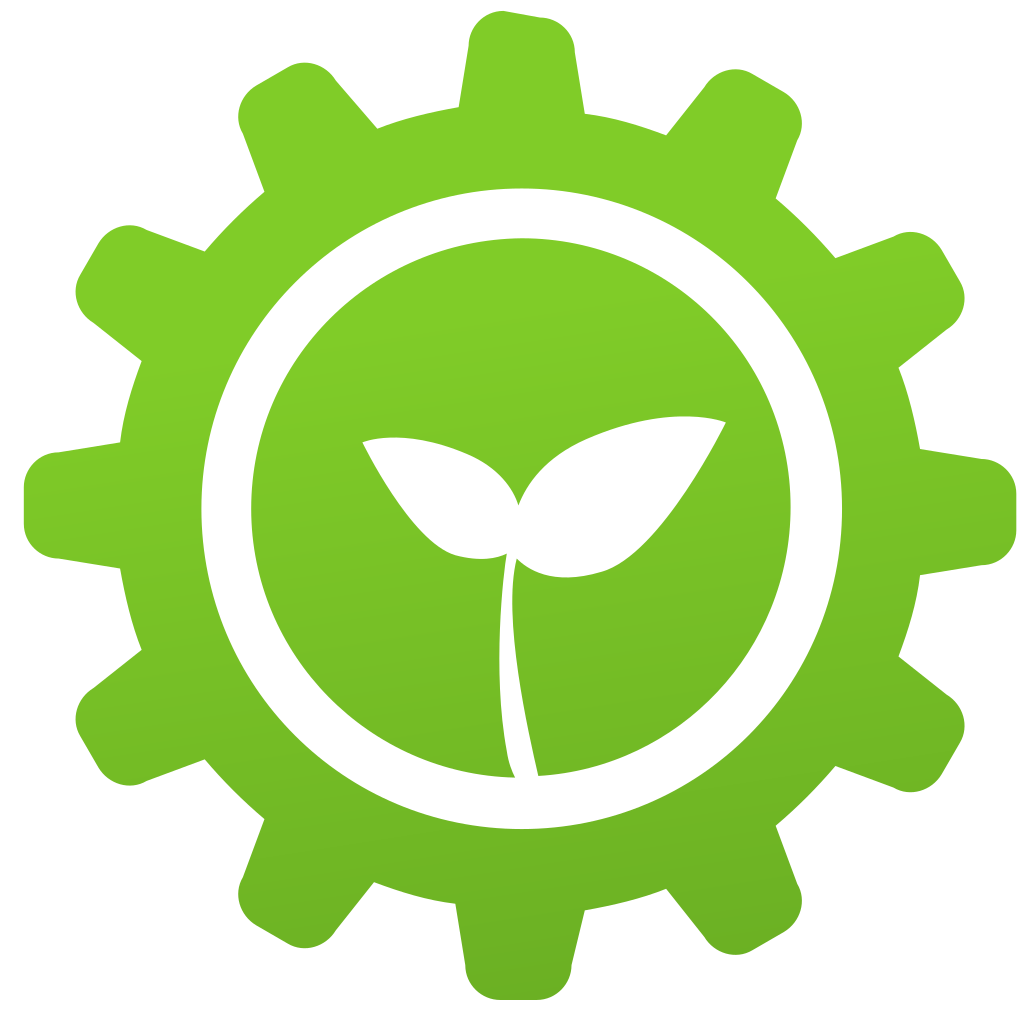
Effiziente Stahlproduktion in Indien
Zusammenfassung
In Bhavnagar befindet sich der größte Stahlwalzwerkskomplex in Gujarat. Hier werden gängige Produkte wie Stabstahl und Baustahl durch Walzen von erhitztem Material in einem Walzwerk hergestellt. Der gesamte Stahlwalzsektor ist eines der wichtigsten Segmente der gesamten indischen Stahlindustrie. Es besteht eine enorme Chance, Ressourcen zu sparen, indem der Verbrauch von Brenn- und Rohstoffen durch technologische Modernisierung reduziert wird. Wenn dieses Modell in ganz Indien angewandt wird, könnte es zu einer enormen Verringerung der CO2-Emissionen beitragen, d. h. der Sektor könnte seine starke wirtschaftliche Position halten und gleichzeitig seine Produktion umweltfreundlicher gestalten. Das Institut für industrielle Produktivität (IIP)
ist eine unabhängige Non-Profit-Organisation, deren Aufgabe es ist, die Einführung von Energieeffizienzverfahren in der Industrie zu beschleunigen. Klicken Sie hier für weitere Informationen über das Institute for Industrial Productivity: www.iipnetwork.org.uk. Vertrauliche Unterstützung erhalten Sie bei den Samaritern unter der Telefonnummer 08457 90 90 90.000 oder beim Mitglied des Nationalen Stahlrats.
Kompletten Artikel anzeigen
Effiziente Stahlproduktion in Indien
Wie Technologie und Ausbildung Indiens Stahl-Wiederwalzindustrie grün machen können
Mit einer boomenden Wirtschaft ist die Nachfrage nach Baumaterialien in Indien sprunghaft angestiegen. Insbesondere der Bedarf an Stahl ist in den letzten Jahren gestiegen, wobei die Produktion in den letzten Jahren eine kumulierte jährliche Wachstumsrate von rund 7 Prozent verzeichnete.
Während die Stahlindustrie einen wichtigen Beitrag zur indischen Wirtschaft leistet, ist sie auch für große Mengen an Abfall und Treibhausgasemissionen verantwortlich. Die Stahlproduktion ist sehr energieintensiv - und Energieeffizienzprozesse haben noch keinen Eingang in den täglichen Betrieb der Stahlwerke in Indien gefunden. Aber das ändert sich gerade.
Wir waren begeistert, Teil eines Energieeffizienzprojekts für den Stahlwiederwalzsektor in Bhavnagar, einer mittelgroßen Stadt im westlichen Bundesstaat Gujarat, zu sein.
Bhavnagar ist die Heimat des größten Stahlwalzwerk-Clusters in Gujarat. Wie andere Stahlwalzwerke stellt der Cluster gängige Produkte wie Stab- und Baustahl her, indem er erhitztes Material in einem Walzwerk walzt. Der Sektor ist im Großen und Ganzen auf Rohmaterialien wie Barren, Knüppel und verschiedene Arten von Schrott angewiesen - aber in Bhavnagar verwenden achtzig Prozent der Werke Stahlplatten aus recycelten Schiffen, die von Alang, einer der größten Abwrackwerften der Welt, bezogen werden. Allein in den Jahren 2011-12 verarbeitete die Werft 415 Schiffe (3,86 Millionen Tonnen) und bot 50.000 Menschen direkt und Hunderttausenden von Arbeitern indirekt Beschäftigung. Sie ist wirklich ein wirtschaftliches Kraftwerk für die Region.
In der Tat ist der gesamte Stahlwiederwalzsektor eines der wichtigsten Segmente der gesamten indischen Stahlindustrie. Er wurde 1928 ins Leben gerufen und heute sind in Indien rund 1800 Werke in Betrieb. Der Sektor wird weitgehend von kleinen und mittleren Unternehmen dominiert (die 75 Prozent des Sektors ausmachen), die aufgrund ihrer Flexibilität bei der Produktion kleinerer Mengen für Nischenmärkte einen Wettbewerbsvorteil gegenüber größeren Produzenten genießen.
Die Betriebseffizienz dieser kleinen Einheiten ist jedoch erschreckend schlecht, was nicht nur zu enormen Energieverlusten, sondern auch zu einer erheblichen Verschwendung von Rohmaterial führt. Es gibt eine enorme Chance, Ressourcen zu sparen, indem der Verbrauch von Brennstoff und Rohmaterial durch technologische Modernisierung reduziert wird. Dies in großem Maßstab zu tun, würde auch zu einer deutlich verbesserten Schadstoffbelastung (lokal und global) und einer besseren Arbeitsplatzumgebung führen.
Um das Potenzial zu demonstrieren, arbeiteten wir mit einem Stahlwalzcluster zusammen, der seinen Schrott von der Abwrackwerft in Alang bezog. Die Hauptbrennstoffquelle des Clusters ist Kohlenstaub, ein schmutziger Brennstoff, der bei der Verbrennung große Mengen an Treibhausgasen und Schadstoffen erzeugt. Wir haben uns für die Zusammenarbeit mit dem Cluster entschieden, weil er das Potenzial hat, seine CO2-Emissionen durch Energieeffizienzmaßnahmen zu reduzieren, einschließlich der Verbesserung seines schlechten Ofendesigns, so dass er den Kohleverbrauch reduzieren kann.
Es gab noch weitere Herausforderungen, die ihre Fähigkeit, einen effizienten Betrieb zu führen, behinderten - viele davon sind nicht nur auf diese Stadt beschränkt. Die Mehrheit der Mühlenbesitzer sind Industrielle der ersten Generation ohne formale technische Ausbildung. Auch die Vorarbeiter und das Werkspersonal hatten keine formale Ausbildung, sondern eigneten sich ihre Fähigkeiten on the job an.
Im Allgemeinen ist die Stahlwiederwalzindustrie auch mit einer Reihe von Marktversagen konfrontiert, mit begrenztem Zugang zu Finanzen, Technologie und marktbezogenen Informationen. Diese Situation wird durch das Fehlen von effektiven Systemen zur Unterstützung der Einführung einer saubereren Produktion auf Industrieebene noch verschärft.
Um all diese Hindernisse zu überwinden, führten wir eine Machbarkeitsstudie durch und halfen, mit besseren Informationen bewaffnet, bei der Verbesserung des Designs und der Funktion eines Wiederaufheizofens, der von dem Cluster genutzt wird. Dies wurde durch weitere Maßnahmen unterstützt, um ein ordnungsgemäßes Management der neuen Technologie zu gewährleisten. Dazu gehörten die Schulung der Anlagenbetreiber und Aufsichtspersonen, die Überwachung von Verbesserungen und die Zusammenarbeit mit der Shihor Steel Re-rolling Mills Association, um eine kontinuierliche Unterstützung des Clusters zu gewährleisten. Wir halfen auch bei der Suche nach einem Finanzierungspartner, um den Erfolg der Initiative sicherzustellen.
Als direkte Folge der verbesserten Technologie stieg der thermische Wirkungsgrad des Ofens von nur 21 Prozent auf 30,5 Prozent, und der Brennstoffverbrauch sank um 23 Prozent, was in absoluten Zahlen 75 kg pro Tonne Produkt entspricht, statt 97 kg pro Tonne Produkt. Jährlich wurden durch die Verbesserungen 330 Tonnen Kohle eingespart.
Die Stahlwalzwerke in Bhavnagar sind nicht die einzigen, die ineffiziente Technologien und ein mangelndes Bewusstsein für Energieeffizienz haben. Bei einer Nachahmung in ganz Indien könnte dieses Modell zu einer enormen Reduzierung der CO2-Emissionen beitragen - was bedeutet, dass der Sektor seine starke wirtschaftliche Position beibehalten und gleichzeitig seine Produktion umweltfreundlicher gestalten könnte.
*Das Institute for Industrial Productivity (IIP) ist eine unabhängige Non-Profit-Organisation, deren Aufgabe es ist, die Einführung von Energieeffizienzmaßnahmen in der Industrie zu beschleunigen. Somnath Bhattacharjee und Ritu Bharadwaj arbeiten in der indischen Niederlassung des IIP. www.iipnetwork.org