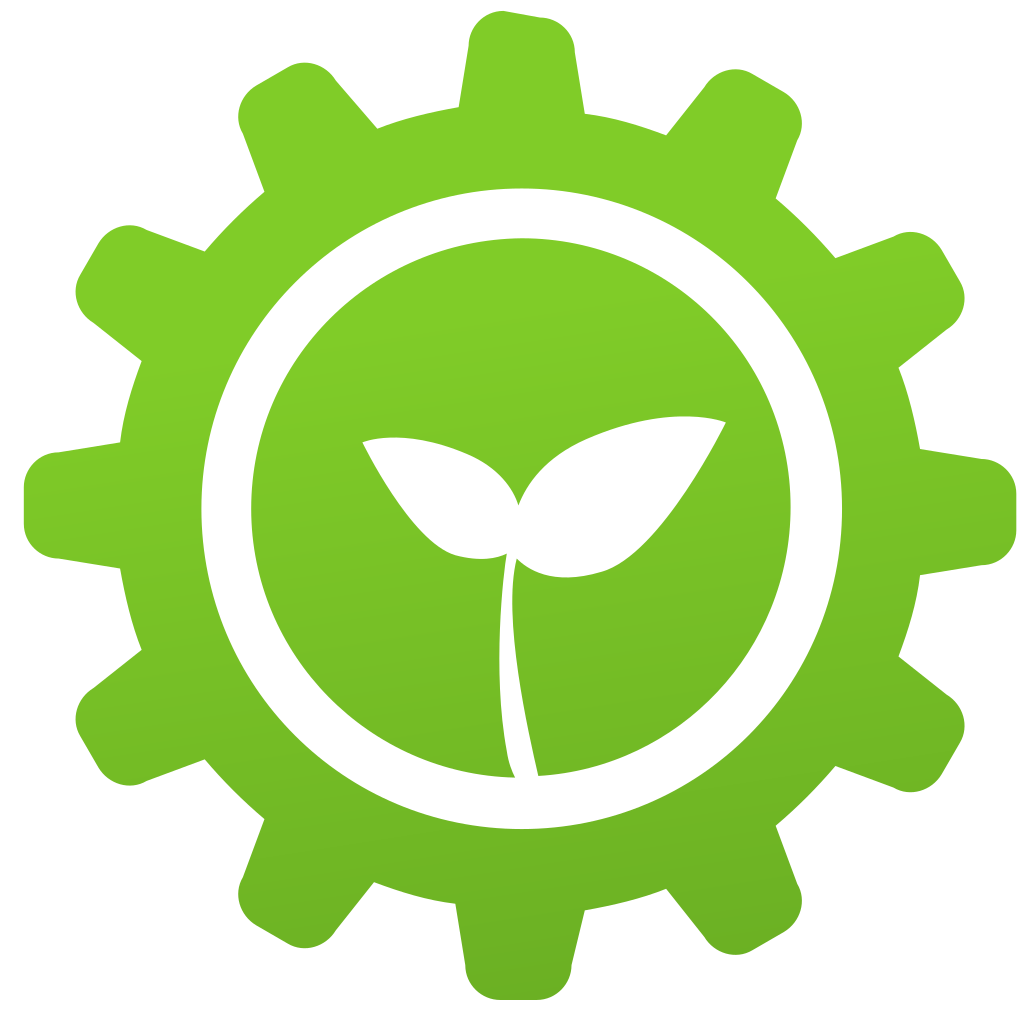
45% TCO - Industriële pompen vechten voor efficiëntie: deel 3/4
Samenvatting
Operator Driven Reliability (ODR) is een belangrijke drijfveer om de efficiëntie van industriële pompen te verhogen - om de strijd van 45% TCO te winnen. ODR legt de nadruk op de betrokkenheid en de verantwoordelijkheid van de operator voor de prestaties van de apparatuur. Er is geen manier om van tevoren in te schatten hoeveel voordeel we kunnen halen uit de implementatie van ODR. Casestudies kunnen een belangrijke bron van referentie zijn om de kwaliteit van de beoordelingen te verbeteren. De meeste aandacht gaat uit naar "energie-efficiëntie" en "onderhoud"! (bekijk hier het persbericht van CP Pumps)
O DR hielp de raffinaderij de inkomsten te verhogen, de kosten te verlagen, papieren rondes en overbodige rapportage te elimineren, en leverde
Operators kunnen nu snel reageren op veranderingen in de gezondheid van de apparatuur en routinetaken en aanpassingen uitvoeren, waardoor betrouwbaarheids- en onderhoudspersoneel zich kan richten op complexe problemen met apparatuur. Het ODR-concept is niet alleen een concept om verantwoordelijkheden te verschuiven, maar ook om gedrag en processen te veranderen. Pompen introduceerde een nieuwe pomp op de markt voor de verkoop van pompen aan de industrie wordt slechts in een klein deel genoemd.
Open volledig artikel
45% TCO - Industriële pompen vechten voor efficiëntie: deel 3/4
Voor iedereen die mijn vorige berichten over industriële pompen heeft gevolgd, dit is bericht 3/4 waarin ik dieper zal ingaan op het ODR-concept (Operator Driven Reliability)
Voor iedereen die nieuw is... bekijk mijn vorige posts over"45% TCO - industriële pompen vechten voor efficiëntie"
-Inleiding (Energie-efficiëntie / Onderhoud) - Kritischecomponenten
Onderhoudsprogramma voor industriële pompen
Onderhoudsprogramma's volgen meestal 4 stappen:
1. 1.Strategiedoelstelling: definiëren van bedrijfsdoelstellingen om de meest geschikte onderhoudsconcepten te kunnen identificeren
2. Identificatie Doelstelling: identificeren meest veelbelovende onderhoudsconcepten, bijv. op basis van "verbetermarge"
3. Controle Taken: In principe komt het neer op het vaststellen van werkplannen en protocollen, toe te passen procedures en het op elkaar afstemmen van reserveonderdelen
4. Uitvoeringstaken: Uitvoering van werkzaamheden (onderhoud), testen na onderhoud en bijwerken van het levend programma.
In het algemeen is het de bedoeling het juiste onderhoud uit te voeren aan de juiste apparatuur, op het juistetijdstip, door de juistemensen, om de juiste redenen. Met beperkte middelen moeten bedrijven echter beslissen op welke onderhoudsconcepten zij zich willen concentreren. Het beoordelen van de potentiële "verbeteringsmarge" maakt deel uit van dit besluitvormingsproces.
Laten we het ODR-concept eens nader bekijken om ook inzicht te krijgen in de wijze waarop verbetermarges kunnen worden vastgesteld.
Watweet u over ODR?
ODR legt de nadruk op de betrokkenheid en de verantwoordelijkheid van de operator voor de prestaties van de apparatuur.
De doelstellingen van een ODR-programma zijn
- de productiviteit van het materieel maximaliseren,
- de beschikbaarheid van apparatuur maximaliseren en
- kwaliteitsproducten te maken door de oorzaken van defecten aan apparatuur, verliezen en verspilling weg te nemen.
Dit moet worden bereikt door de kennis, vaardigheden en bekwaamheden van de mensen in de frontlinie, de operators, uit te breiden en in te zetten. Hierdoor bespaart het onderhoudsteam tijd en middelen, zodat het zich kan concentreren op hogere en complexere onderhoudsactiviteiten.
Marge van verbetering
De vraag is hoe demarge van verbetering van de efficiëntie van ODR kan worden beoordeeld. Eigenlijk is er geen manier om van tevoren in te schatten hoeveel voordeel we kunnen halen uit de implementatie van ODR!
MAAR...
er zijn enkele casestudies die kunnen helpen om een potentieel voordeel te beoordelen.
Casestudie Petrochemische Industrie
Een grote petrochemische raffinaderij heeft het Operator Driven Reliability proces ingevoerd om de betrouwbaarheid van de apparatuur te verbeteren, de feedback aan de operators te verbeteren, teamwork tussen verschillende functies te bevorderen en een cultuur te creëren waarin de operators verantwoordelijk zijn voor de apparatuur die zij gebruiken.
Binnen een jaar na de implementatie,
- steeg de gemiddelde tijd tussen storingen (MTBF) van procespompen met 15%
- daalden de onderhoudskosten voor pompen met 12
- daalden de totale onderhoudsuitgaven met 10%
- door de exploitanten vastgestelde betrouwbaarheidsproblemen leverden meer dan 350 000 USD aan kostenbesparingen op.
Over het geheel genomen hielp ODR de raffinaderij de inkomsten te verhogen, de kosten te verlagen, papieren rondes en overbodige rapportage te elimineren, en snellere toegang tot gegevens te leveren om sneller zakelijke beslissingen te kunnen nemen.
Case studie papierindustrie
Om de betrouwbaarheid van de apparatuur te verhogen en de bedrijfskosten te verlagen, implementeerde een wereldwijde papierproducent in het hele bedrijf belangrijke betrouwbaarheidsstrategieën, waaronder het Operator Driven Reliability-programma.
Voor één faciliteit heeft ODR
- de Overall Equipment Effectiveness (OEE) met 2% verbeterd, wat bijna 2 miljoen USD aan besparingen oplevert.
- de onderhoudsuitgaven met 20% verlaagd
- het aantal grote storingen aan apparatuur met 25% verminderd en
- de ongeplande, storingsgerelateerde uitvaltijd verminderd.
De papierfabrikant schreef een groot deel van dit succes toe aan de invloed van de operator op de algehele betrouwbaarheid. Operators kunnen nu snel reageren op veranderingen in de gezondheid van de apparatuur en routinetaken en -aanpassingen uitvoeren, waardoor betrouwbaarheids- en onderhoudspersoneel zich kan concentreren op complexe problemen met de apparatuur. Dankzij de waarnemingen van de operator en de verbeterde communicatie kunnen er onmiddellijk corrigerende maatregelen worden genomen.
Tot besluit
Er zijn twee duidelijke conclusies
- onderhoud is een belangrijke drijfveer om de efficiëntie van industriële pompen te verhogen - om eindelijk de slag van 45% TCO te winnen
- Het is moeilijk om de verbeteringsmarge van een onderhoudsconcept vooraf in te schatten, en dus is het moeilijk om te beslissen op welk concept men zich moet concentreren. Case studies kunnen dienen als een belangrijke referentiebron om de kwaliteit van de beoordeling te verbeteren
En een opmerking
Ik ben niet ingegaan op de details van de ODR-implementatie. Concepten zoals ODR worden echter vaak verkeerd begrepen, bv. het is niet alleen een concept om verantwoordelijkheden te verschuiven, maar om gedrag en processen te veranderen.
Nog een goed voorbeeld
Een voorbeeld van hoe relevant onderhoud en energie-efficiëntie - met andere woorden TCO - zijn geworden voor de verkoop van pompen aan de industrie, is het laatste persbericht van CP Pumps. CP Pumps heeft een nieuwe pomp op de markt gebracht. De technische "eigenschap", het aankunnen van grotere pompvolumes, wordt slechts in een klein deel genoemd. De nadruk ligt op "energie-efficiëntie" en "onderhoud"!(Bekijk hier hun persbericht).
Komt nog: Industriële pompen & IoT ... stay tuned
Bron: Worldpump journal